Advances in the processing techniques of Spheroidal Graphite Cast Iron (SGCI), also known as ductile iron, have significantly improved its properties and broadened its range of applications. These advances mainly focus on refining the microstructure and enhancing the mechanical properties such as strength, ductility, and toughness. Let’s explore some of these key advances:
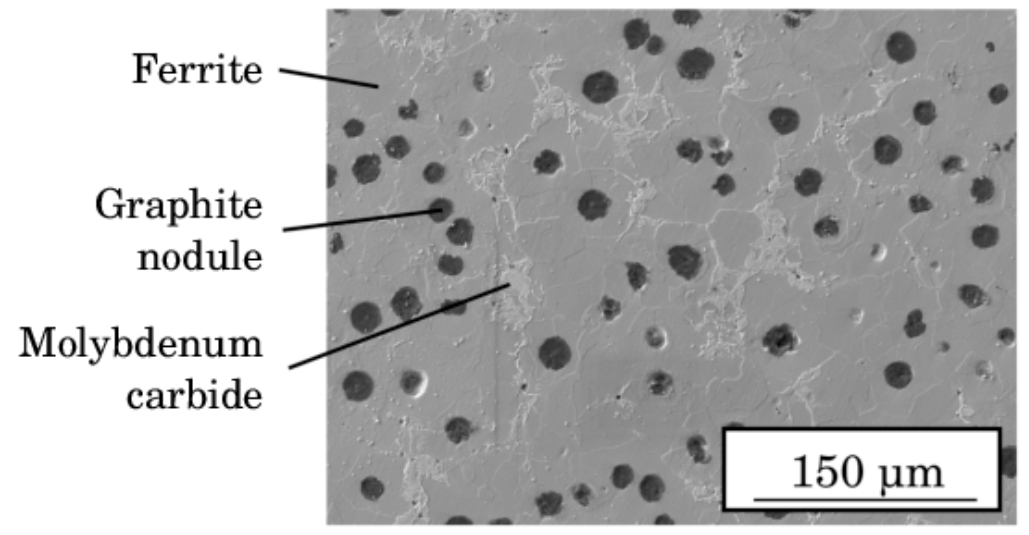
1. Improved Nodulization Techniques
- Enhanced Chemical Additives: The use of advanced nodulizing agents (like magnesium and rare earth elements) has been refined to achieve a more consistent and uniform graphite nodule size and distribution. This uniformity is critical in achieving desired mechanical properties.
- Controlled Processing Environment: Innovations in controlling the melting and casting environment (like inert gas shrouding or vacuum processing) have led to a reduction in impurities and defects, resulting in higher quality Spheroidal Graphite Cast Iron.
2. Advanced Heat Treatment Processes
- Austempering: This process transforms the microstructure to austenite and bainite, enhancing both strength and ductility. Austempered Ductile Iron (ADI) exhibits excellent wear resistance and fatigue strength, making it suitable for demanding applications.
- Ferritizing and Pearlitizing: These heat treatments adjust the ferrite and pearlite content in the matrix, allowing for a tailored balance between strength and ductility.
- Induction Hardening: Used for surface hardening of Spheroidal Graphite Cast Iron parts, this technique increases wear resistance while retaining a ductile core.
3. Alloying for Enhanced Properties
- Microalloying: Small additions of elements like nickel, copper, and molybdenum can significantly impact the mechanical properties and corrosion resistance of Spheroidal Graphite Cast Iron.
- High-Silicon Spheroidal Graphite Cast Iron: Silicon alloys have been developed to improve corrosion resistance, particularly in aggressive environments.
4. Casting Process Innovations
- Computer-Aided Design (CAD) and Simulation: The use of CAD and simulation software in the casting process allows for precision in design and prediction of how the cast will behave, reducing defects and improving quality.
- Improved Mold Materials and Techniques: Advances in mold materials and casting techniques have led to better surface finishes and dimensional accuracy.
5. Additive Manufacturing
- 3D Printing of Spheroidal Graphite Cast Iron: Although challenging due to its unique properties, progress is being made in 3D printing Spheroidal Graphite Cast Iron, allowing for the creation of complex geometries that are difficult to achieve with traditional casting methods.
6. Environmental and Sustainable Manufacturing
- Energy-Efficient Melting Techniques: Adoption of energy-efficient melting furnaces and practices reduces the environmental impact of Spheroidal Graphite Cast Iron production.
- Recycling Practices: Enhancing the recyclability of Spheroidal Graphite Cast Iron, including efficient scrap utilization, aligns with global sustainability goals.
Conclusion
The continuous evolution of processing techniques in Spheroidal Graphite Cast Iron not only enhances its intrinsic qualities but also paves the way for its use in more sophisticated and demanding applications. From automotive and aerospace components to infrastructure and heavy machinery, these advances ensure that Spheroidal Graphite Cast Iron remains a material of choice in various industries, combining performance with cost-effectiveness and sustainability.