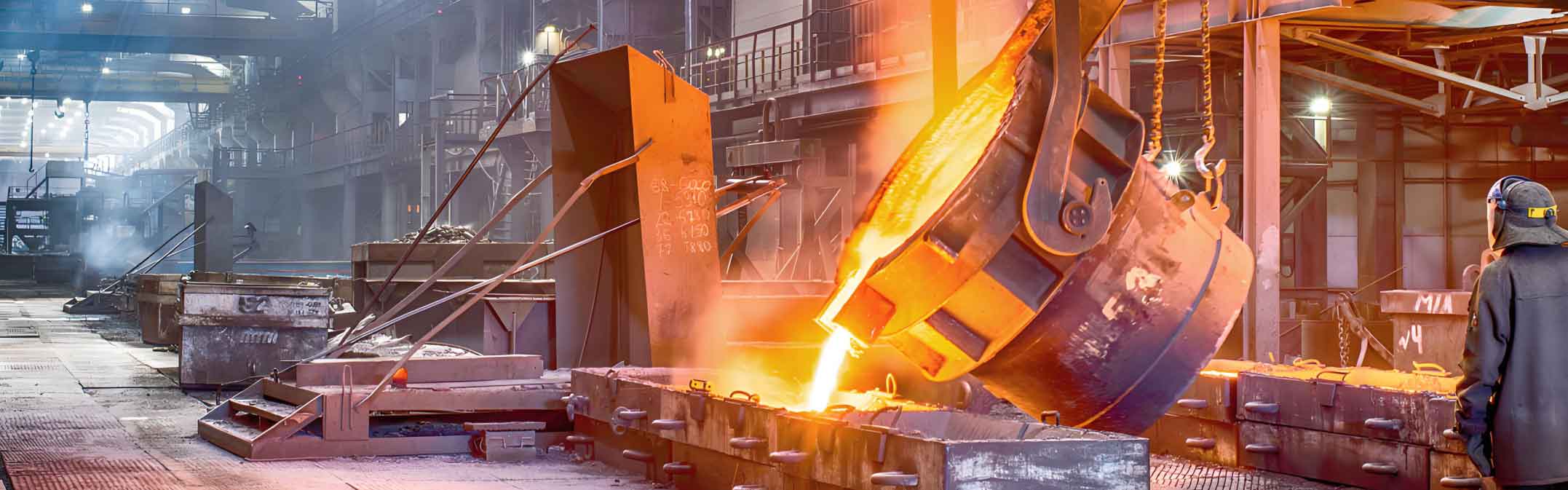
In the realm of metal casting, two prominent techniques stand out for their precision and versatility: lost wax casting and lost foam casting. Both methods are revered for their ability to produce intricate and detailed components, yet they differ significantly in their processes, applications, and benefits. This article provides a comprehensive comparative study of lost wax casting and lost foam casting techniques, highlighting their respective processes, advantages, disadvantages, and typical applications.
Lost Wax Casting
Lost wax casting, also known as investment casting, is a time-honored technique used to create precise and complex metal components. The process involves creating a wax model of the desired component, which is then coated with a refractory ceramic material to form a mold. Once the ceramic shell is hardened, the wax is melted away, leaving a cavity that is filled with molten metal to form the final component.
Process of Lost Wax Casting
- Wax Pattern Creation:
- A wax model is created using either manual sculpting or injection molding techniques.
- Assembly:
- The wax model is attached to a wax sprue, forming a tree-like structure for multiple castings.
- Ceramic Shell Formation:
- The wax assembly is repeatedly dipped in a ceramic slurry and coated with fine sand until a thick shell is formed.
- Wax Removal:
- The ceramic shell is heated to melt and drain the wax, leaving a hollow mold.
- Metal Pouring:
- Molten metal is poured into the ceramic mold to fill the cavity.
- Shell Removal:
- The ceramic shell is broken away to reveal the metal casting.
- Finishing:
- The casting is cleaned, and any excess material is removed to achieve the final product.
Advantages of Lost Wax Casting
- High Precision: Allows for intricate and detailed designs with tight tolerances.
- Excellent Surface Finish: Produces smooth surfaces, reducing the need for extensive machining.
- Versatility: Suitable for a wide range of metals and alloys.
- Minimal Material Waste: The process is highly efficient, with little waste.
Disadvantages of Lost Wax Casting
- Cost: The process can be expensive due to the materials and labor involved.
- Time-Consuming: Creating the wax patterns and ceramic shells takes significant time.
- Size Limitations: Best suited for smaller components due to the fragility of the wax models.
Applications of Lost Wax Casting
- Aerospace: Production of turbine blades and complex engine components.
- Jewelry: Creating intricate and detailed pieces.
- Medical: Manufacturing of orthopedic implants and surgical instruments.
- Art and Sculpture: Producing detailed and intricate artistic works.
Advantages of Lost Wax Casting | Disadvantages of Lost Wax Casting |
---|---|
High precision | Expensive |
Excellent surface finish | Time-consuming |
Versatility in metal types | Size limitations |
Minimal material waste | Complex process |
Lost Foam Casting
Lost foam casting is a modern and innovative technique that uses a foam pattern instead of wax. The foam pattern is coated with a refractory material and placed in a sand mold. When molten metal is poured into the mold, the foam pattern vaporizes, leaving behind a metal casting that replicates the original foam pattern.
Process of Lost Foam Casting
- Foam Pattern Creation:
- A foam model is created using polystyrene foam, either by machining or molding.
- Assembly:
- The foam pattern is assembled with a gating system if needed.
- Coating:
- The foam pattern is coated with a refractory material to form a thin shell.
- Mold Preparation:
- The coated foam pattern is placed in a sand mold, and sand is packed around it.
- Metal Pouring:
- Molten metal is poured into the mold, causing the foam pattern to vaporize and be replaced by the metal.
- Mold Breakout:
- Once the metal has solidified, the sand mold is broken away to reveal the metal casting.
- Finishing:
- The casting is cleaned and any excess material is removed to achieve the final product.
Advantages of Lost Foam Casting
- Cost-Effective: Lower tooling costs and reduced labor requirements.
- Simplified Process: Eliminates the need for core making and wax removal steps.
- Flexibility in Design: Allows for complex shapes and thin-walled sections.
- Environmental Benefits: Reduces waste and emissions compared to traditional casting methods.
Disadvantages of Lost Foam Casting
- Surface Finish: May produce rougher surfaces compared to lost wax casting.
- Pattern Fragility: Foam patterns can be delicate and prone to damage.
- Material Limitations: Less suitable for certain high-temperature alloys.
- Dimensional Accuracy: Can be less precise than lost wax casting.
Applications of Lost Foam Casting
- Automotive: Production of engine blocks, cylinder heads, and other complex components.
- Marine: Manufacturing of propellers and other intricate parts.
- Industrial Machinery: Creating components with complex geometries.
- Consumer Goods: Producing decorative items and hardware.
Advantages of Lost Foam Casting | Disadvantages of Lost Foam Casting |
---|---|
Cost-effective | Rougher surface finish |
Simplified process | Fragility of foam patterns |
Flexibility in design | Material limitations |
Environmental benefits | Less precise dimensional accuracy |
Comparative Analysis
Process Complexity
- Lost Wax Casting: Involves multiple steps including wax pattern creation, ceramic shell formation, and wax removal. The process is intricate and labor-intensive.
- Lost Foam Casting: Simplified process with fewer steps. Eliminates the need for core making and wax removal, making it more straightforward.
Precision and Surface Finish
- Lost Wax Casting: Offers high precision and excellent surface finish, ideal for components requiring tight tolerances and smooth surfaces.
- Lost Foam Casting: Provides good flexibility in design but may result in rougher surfaces and less precise dimensional accuracy compared to lost wax casting.
Cost and Efficiency
- Lost Wax Casting: Generally more expensive due to higher material and labor costs. The process is time-consuming and best suited for small, intricate components.
- Lost Foam Casting: More cost-effective with lower tooling and labor costs. The process is faster and suitable for larger components with complex geometries.
Material and Design Flexibility
- Lost Wax Casting: Highly versatile, accommodating a wide range of metals and alloys. Suitable for detailed and intricate designs.
- Lost Foam Casting: Offers flexibility in design, allowing for complex shapes and thin-walled sections. However, it is less suitable for high-temperature alloys.
Environmental Impact
- Lost Wax Casting: Generates waste materials such as used ceramic shells and wax residues. The process may also involve emissions from melting and pouring metals.
- Lost Foam Casting: Environmentally friendly, with reduced waste and emissions. The foam patterns vaporize during the process, leaving minimal residues.
Aspect | Lost Wax Casting | Lost Foam Casting |
---|---|---|
Process Complexity | High | Low |
Precision and Surface Finish | High precision, excellent surface finish | Good flexibility, rougher surface finish |
Cost and Efficiency | Expensive, time-consuming | Cost-effective, faster |
Material and Design Flexibility | Versatile, detailed designs | Flexible design, less suitable for high-temp alloys |
Environmental Impact | Generates waste and emissions | Reduced waste and emissions |
Conclusion
Both lost wax casting and lost foam casting offer unique advantages and are suited to different applications based on their respective processes, precision, cost, and environmental impact. Lost wax casting is ideal for producing highly intricate and precise components with excellent surface finish, making it suitable for aerospace, jewelry, medical, and artistic applications. On the other hand, lost foam casting provides a cost-effective and environmentally friendly alternative for creating complex shapes and larger components, commonly used in the automotive, marine, and industrial machinery sectors.
Understanding the strengths and limitations of each technique allows manufacturers to choose the most appropriate casting method for their specific needs, ensuring optimal performance and efficiency in their production processes.