Lost wax casting is precise and versatile manufacturing process widely used to produce complex metal components with excellent dimensional accuracy and surface finish. While the casting process itself is critical for achieving the desired geometry, heat treatment plays a crucial role in enhancing the mechanical properties of lost wax cast components. This article explores the importance of heat treatment in lost wax casting, various heat treatment processes, and their effects on the mechanical properties of the final products.
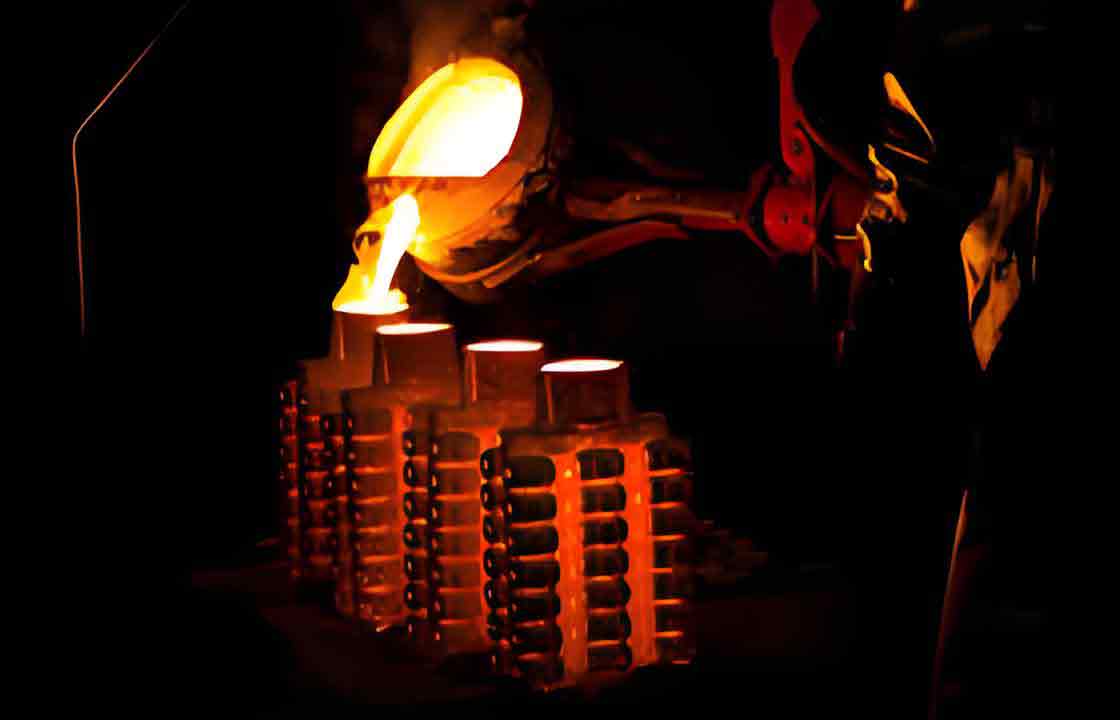
Introduction to Lost Wax Casting
Lost wax casting involves creating a wax model of the desired part, which is then coated with a ceramic shell. The wax is melted out, leaving a cavity that is filled with molten metal. Once the metal solidifies, the ceramic shell is removed to reveal the metal casting. This process is highly advantageous for producing components with intricate geometries and fine details.
Key Steps in Lost Wax Casting
- Pattern Creation: A wax model of the desired part is created using injection molding or hand carving.
- Assembly: Multiple wax models can be assembled onto a wax tree to create multiple parts in a single batch.
- Shell Building: The wax assembly is repeatedly dipped into a ceramic slurry and coated with fine sand to build a ceramic shell.
- Dewaxing: The ceramic shell is heated to remove the wax, leaving a hollow cavity.
- Metal Pouring: Molten metal is poured into the ceramic mold.
- Shell Removal: Once the metal has solidified, the ceramic shell is broken away to reveal the casting.
- Finishing: The casting is cleaned, and any excess material is removed to achieve the final product.
Importance of Heat Treatment in Lost Wax Casting
Heat treatment is a critical post-casting process that involves heating and cooling metal components under controlled conditions to alter their microstructure and improve their mechanical properties. For lost wax cast components, heat treatment can enhance properties such as hardness, strength, ductility, and toughness, making them suitable for demanding applications.
Benefits of Heat Treatment
- Improved Mechanical Properties: Enhances hardness, strength, ductility, and toughness.
- Stress Relief: Reduces internal stresses caused by casting and cooling processes.
- Refined Microstructure: Alters the grain structure to improve overall performance.
- Enhanced Wear Resistance: Increases resistance to wear and abrasion.
Common Heat Treatment Processes
Several heat treatment processes can be applied to lost wax cast components, each with specific effects on the mechanical properties. The choice of heat treatment depends on the material and the desired properties of the final product.
1. Annealing
Annealing involves heating the cast component to a specific temperature and then slowly cooling it. This process is used to soften the metal, improve ductility, and relieve internal stresses.
- Process: Heat to a specified temperature, hold for a certain period, and cool slowly.
- Benefits: Reduces hardness, improves ductility, relieves internal stresses.
- Applications: Components requiring improved machinability and reduced brittleness.
2. Normalizing
Normalizing involves heating the cast component to a temperature above its critical range and then air cooling it. This process refines the grain structure and enhances mechanical properties.
- Process: Heat to a temperature above the critical range, hold for a certain period, and cool in air.
- Benefits: Improves strength, hardness, and toughness, refines grain structure.
- Applications: Structural components requiring uniform mechanical properties.
3. Quenching and Tempering
Quenching involves rapidly cooling the cast component from a high temperature by immersing it in a quenching medium (such as water, oil, or air). Tempering follows quenching and involves reheating the component to a lower temperature and then cooling it. This process improves hardness and strength while reducing brittleness.
- Process: Heat to a high temperature, quench in a medium, reheat to a lower temperature, and cool.
- Benefits: Increases hardness and strength, reduces brittleness, improves toughness.
- Applications: Wear-resistant components, tools, and dies.
4. Solution Treatment and Aging
Solution treatment involves heating the cast component to a high temperature to dissolve alloying elements in the matrix, followed by rapid cooling (quenching). Aging involves reheating the component to a lower temperature to precipitate the alloying elements, enhancing mechanical properties.
- Process: Heat to a high temperature, quench, reheat to a lower temperature, and cool.
- Benefits: Enhances strength and hardness, improves corrosion resistance.
- Applications: Aerospace components, high-performance alloys.
Effects of Heat Treatment on Mechanical Properties
The mechanical properties of lost wax cast components are significantly influenced by heat treatment. The following table summarizes the effects of different heat treatment processes on key mechanical properties.
Heat Treatment Process | Hardness | Strength | Ductility | Toughness | Microstructure |
---|---|---|---|---|---|
Annealing | Decreases | Decreases | Increases | Increases | Coarse grain structure, reduced internal stresses |
Normalizing | Increases | Increases | Moderate | Increases | Refined grain structure, uniform properties |
Quenching and Tempering | Increases | Increases | Decreases | Increases | Fine grain structure, improved wear resistance |
Solution Treatment and Aging | Increases | Increases | Moderate | Moderate | Precipitated alloying elements, enhanced properties |
Case Studies: Heat Treatment in Lost Wax Casting
Case Study 1: Aerospace Components
Aerospace components require high strength, toughness, and corrosion resistance. Lost wax cast components for aerospace applications often undergo solution treatment and aging to achieve the desired properties.
- Process: Solution treatment at 950°C followed by aging at 500°C for 8 hours.
- Results: Improved strength, hardness, and corrosion resistance, suitable for critical aerospace applications.
Case Study 2: Medical Implants
Medical implants require excellent biocompatibility, strength, and fatigue resistance. Lost wax cast components for medical applications undergo annealing to improve ductility and reduce internal stresses.
- Process: Annealing at 750°C for 2 hours followed by slow cooling.
- Results: Enhanced ductility, reduced brittleness, and improved biocompatibility, suitable for medical implants.
Case Study 3: Industrial Tools
Industrial tools require high hardness and wear resistance. Lost wax cast components for industrial tools undergo quenching and tempering to achieve the desired properties.
- Process: Quenching at 900°C followed by tempering at 300°C for 2 hours.
- Results: Increased hardness, strength, and wear resistance, suitable for industrial tools and dies.
Conclusion
Heat treatment is a vital process in enhancing the mechanical properties of lost wax cast components. By carefully selecting and optimizing heat treatment processes such as annealing, normalizing, quenching and tempering, and solution treatment and aging, manufacturers can achieve the desired properties for various applications. Understanding the effects of heat treatment on mechanical properties and addressing common casting defects through improved processes and quality control ensures that lost wax casting remains a reliable and effective method for producing high-quality metal components.
By focusing on advanced heat treatment techniques and strategies, manufacturers can continue to leverage lost wax casting for a wide range of applications, delivering parts that combine intricate designs, excellent mechanical properties, and superior performance.