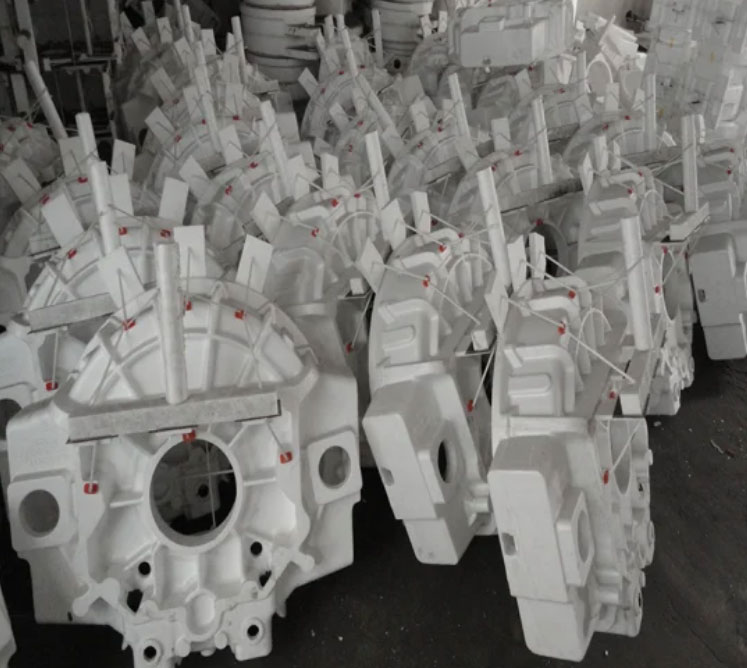
Lost foam casting (LFC) offers several advantages that make it an attractive choice for various manufacturing applications. These advantages include:
1. Design Freedom and Complexity:
Lost foam casting allows for the production of parts with intricate and complex geometries that may be challenging or costly to achieve using traditional casting methods. Designers have the freedom to create parts with undercuts, thin walls, and internal cavities, enabling the production of innovative and unique components.
2. Precision and Dimensional Accuracy:
Foam patterns used in lost foam casting can be accurately shaped, providing excellent dimensional accuracy and repeatability in the final cast parts. This results in precise and consistent components, reducing the need for extensive post-processing and machining.
3. Reduction in Machining and Assembly:
Lost foam casting can produce near-net-shape components, which require minimal or no additional machining or assembly. This results in significant time and cost savings, as there is less material waste and a reduced need for labor-intensive post-processing.
4. Improved Surface Finish:
The refractory coating on the foam pattern results in a smooth and high-quality surface finish on the cast parts. This eliminates the need for extensive surface finishing and polishing, further reducing production time and costs.
5. Single-Piece Designs:
Lost foam casting allows the creation of complex parts as a single piece, eliminating the need for multiple component assemblies. This simplifies the manufacturing process, increases part integrity, and reduces the risk of assembly-related defects.
6. Eco-Friendly and Sustainable:
Lost foam casting is a relatively eco-friendly casting process, as the foam patterns used are made from recyclable materials. Additionally, the evaporated foam does not produce harmful emissions, making the process more environmentally friendly compared to some other casting methods.
7. Shorter Lead Times:
The streamlined process of lost foam casting, along with the elimination of tooling, results in shorter lead times from design to finished parts. This is particularly beneficial for rapid prototyping, custom manufacturing, and time-sensitive projects.
8. Cost Savings:
Lost foam casting can lead to significant cost savings in various aspects of the manufacturing process. The reduced need for tooling and machining, as well as the elimination of assembly and welding, translates to overall cost reduction.
9. Weight Reduction:
The ability to create hollow sections and thin-walled components allows for weight reduction in cast parts. This is particularly advantageous in industries like automotive and aerospace, where lightweighting is a critical consideration for fuel efficiency and performance.
10. Versatility and Material Choices:
Lost foam casting can be used with various materials, including aluminum, iron, steel, and other alloys. This versatility allows manufacturers to choose the most suitable material for specific applications, optimizing part performance and properties.
Lost foam casting’s efficiency, precision, and cost savings make it an excellent choice for a wide range of industries seeking innovative and sustainable manufacturing solutions. By leveraging the advantages of this casting process, manufacturers can achieve high-quality and complex components while optimizing production costs and lead times.