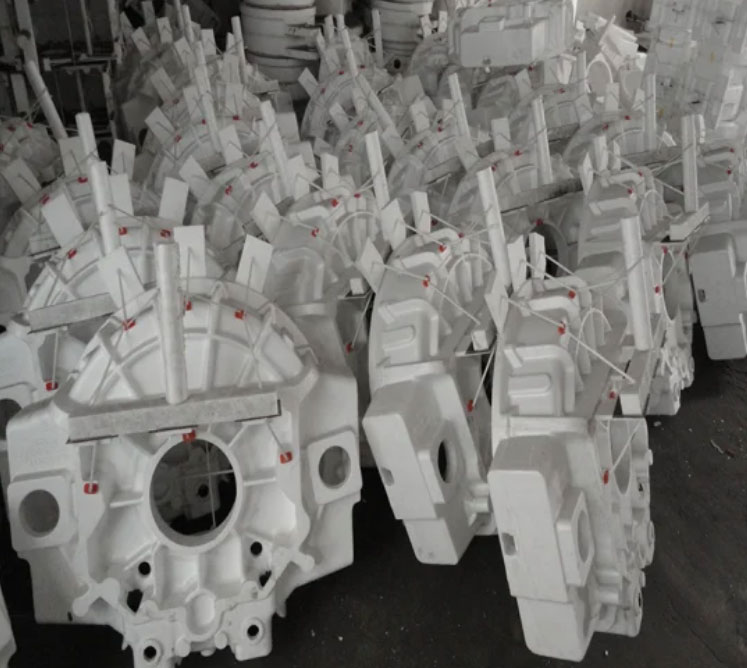
Lost foam casting (LFC) technology offers several opportunities for optimizing foundry operations and improving overall efficiency. By leveraging the advantages of lost foam casting, foundries can streamline their processes, enhance productivity, and reduce costs. Here are some ways to optimize foundry operations with lost foam casting technology:
1. Reduced Tooling Costs:
Lost foam casting eliminates the need for expensive and time-consuming patterns and core boxes used in traditional sand casting. The foam patterns used in LFC are relatively cost-effective to produce, resulting in significant savings on tooling expenses. This reduction in tooling costs can make foundry operations more economically viable.
2. Shorter Lead Times:
The streamlined lost foam casting process, combined with reduced tooling requirements, results in shorter lead times from design to finished parts. The elimination of pattern making and core box preparation allows for quicker production and faster delivery of castings.
3. Design Flexibility and Complexity:
Lost foam casting offers exceptional design flexibility, enabling the production of complex and intricate geometries. Foundries can work closely with designers and engineers to create innovative and customized components with intricate details. This flexibility can lead to unique product offerings and a competitive advantage.
4. Improved Dimensional Accuracy:
The use of precision foam patterns in lost foam casting results in better dimensional accuracy and tighter tolerances in the final cast parts. This reduces the need for extensive post-casting machining and refining, saving time and resources.
5. Enhanced Surface Finish:
The refractory coating on the foam patterns creates smooth and high-quality surface finishes on the castings. This minimizes the need for additional surface finishing operations, such as grinding and polishing.
6. Single-Piece Castings and Reduced Assembly:
Lost foam casting can produce complex parts as single castings, eliminating the need for complex assembly and welding. This simplifies the manufacturing process, reduces labor costs, and minimizes the risk of assembly-related defects.
7. Lightweighting Opportunities:
Lost foam casting allows for the creation of hollow components, enabling foundries to produce lightweight parts with improved strength-to-weight ratios. This is particularly advantageous in industries seeking weight reduction for enhanced performance and fuel efficiency.
8. Waste Reduction and Eco-Friendly Practices:
Lost foam casting generates minimal waste as the foam patterns are easily recyclable. Additionally, the process does not produce harmful emissions, making it an environmentally friendly casting method.
9. Versatility with Materials:
Lost foam casting can be used with various metals and alloys, providing foundries with the flexibility to cater to diverse industrial applications and material requirements.
10. Improved Quality and Consistency:
The precision and repeatability of lost foam casting contribute to improved quality and consistency of castings. This enhances customer satisfaction and reduces the need for rework or rejects.
By embracing lost foam casting technology, foundries can optimize their manufacturing processes, reduce production costs, and deliver high-quality components to meet the demands of modern industries. It is essential for foundries to invest in training their personnel and acquiring the necessary equipment to fully leverage the benefits of lost foam casting and ensure its successful integration into their operations.