Abstract
With the rapid development of construction machinery and the continuous improvement of excavator performance, the demand for high-strength, high-performance, and complex-shaped castings in construction machinery is increasing. Bucket teeth are important safety parts on excavators and also critical vulnerable parts, which have strict requirements for their mechanical performance. Therefore, studying reasonable casting methods for such parts is of great significance for the development of China’s excavator industry.
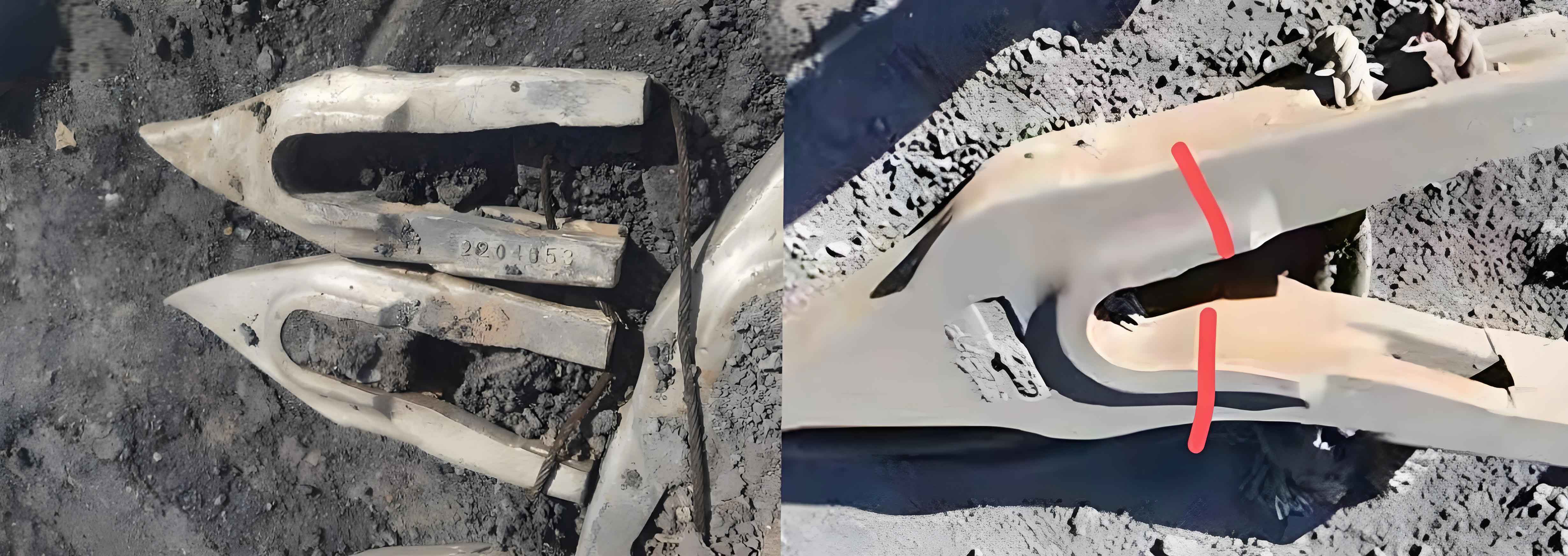
This topic comes from the project “Research and application of improving the wear resistance of castings”, which is jointly carried out by Taiyuan University of Science and Technology and Pingshuo Middling Coal Yuchen Foundry. This paper systematically studies the casting process of P&H2800 bucket teeth through the combination of digital simulation and actual production, which can provide guidance for the casting production of bucket teeth castings. The main research contents of this paper are as follows:
- The selection of casting sand material was completed and experimental measurements were conducted. After measurement, all selected sand materials met the requirements of casting production. The pouring system of P&H2800 bucket teeth was designed, and the initial casting process parameters were determined, including filling time of 45 seconds, pouring temperature of 1600 ℃, and preheating temperature of 600 ℃.
- The 3D modeling of P&H2800 bucket teeth and initial pouring system was completed using Unigraphics NX, and the simulation analysis of the initial casting process was completed by docking with ProCAST. The simulation results showed that although the filling process of the casting was relatively smooth, there was a significant isolated liquid phase zone during solidification, resulting in tissue shrinkage and porosity inside the bucket teeth casting. The simulation results were highly consistent with the actual production situation, and the feasibility of simulating and guiding actual production was verified.
- By setting a single variable control simulation experiment, the casting process parameters were optimized. The results showed that too short or too long the filling time had a negative impact on the quality of the bucket tooth casting. The preheating temperature of the casting should also not be too high or too low. As the pouring temperature decreased, the internal structure of the casting continued to shrink and the volume fraction of shrinkage cavities continued to decrease. However, too low the pouring temperature would affect the fluidity of the molten metal. The optimal process parameter combination was ultimately determined, which is the filling time of 40 seconds, the pouring temperature of 1450 ℃, and the preheating temperature of the casting at 200 ℃.
- After optimizing the process parameters, the volume fraction of tissue shrinkage and porosity decreased from the initial 30.86% to 21.78%. However, tissue shrinkage and porosity still existed inside the casting, and due to the shortened filling time, local eddy currents occurred during the casting filling process. Therefore, the pouring system was optimized. After the optimization of the pouring system, the casting filling process was smooth, and the metal liquid in the riser area finally solidified, achieving the ideal sequential solidification. No tissue shrinkage and porosity occurred inside the casting. Production verification was carried out on the optimized casting process, and a bucket tooth casting with good surface quality and no shrinkage and porosity defects was finally obtained, verifying the feasibility of the process.
The above research content is a major breakthrough in the traditional production process of excavator bucket teeth and has a good guiding role for small and medium-sized casting enterprises. It has great value in both theoretical research and engineering practice.
Keywords: Casting process; P&H2800 bucket teeth; ProCAST; Unigraphics NX; Pouring system; Optimal design
1. Research Background and Significance
In many coal mining industries in China, different mining methods are adopted, such as intermittent mining, continuous mining, and semi-continuous mining. Excavators play a pivotal role in the mining process. For mining operations, high-performance excavator bucket teeth can ensure sufficient safety during excavator operation and bring huge economic benefits. With the development of social productivity and the increasing demand for energy, the scale of open-pit mining has also expanded. Lightweight open-pit mining equipment cannot meet the increased industrial demand and thus requires large-scale development. Bucket teeth, as the core component of excavator operation, are closely connected to the excavator bucket through special pins, and this structural characteristic endows them with the properties of a cantilever beam. During excavator operation, materials such as ore, rock, and sand will impact and wear the bucket teeth. In this process, the bucket teeth will bear huge impact forces. Therefore, in severe working environments, the consumption and wear of bucket teeth are significant. As the scale of open-pit mining expands and large machinery is put into use in large quantities, the demand for bucket teeth in industrial production is also increasing year by year. Since the wear of bucket teeth is fast, it will lead to frequent shutdowns for parts replacement, causing certain economic losses. The main failure modes. Therefore, conducting in-depth research on the manufacturing process of bucket teeth to reduce their wear is of great significance for improving the overall production efficiency and economic performance of excavators.
After entering the 21st century, computer technology has developed rapidly, and microcomputers have become ubiquitous. At the same time, industrial manufacturing and industrial design in various countries around the world have gradually become inseparable from computer technology. In China, many large-scale enterprises and leaders in the casting industry have applied computer technology to actual casting production, thereby giving rise to casting simulation technology. For the optimization design环节, casting simulation technology can qualitatively analyze the temperature changes in various regions of castings and molds, the flow velocity of molten metal during filling, and the filling situation. It can also scientifically and reasonably predict the location and size of defects generated during the casting process. Compared with traditional casting industries, the use of computer simulation technology can more reasonably design molds, reduce trial and error, and achieve cost reduction and efficiency increase.
In addition, the development of casting simulation technology has also reduced the learning cost of mold design to a certain extent. Many beginners can also design a relatively reasonable casting process scheme using casting simulation. By conducting comparative simulation experiments on key process parameters, the optimization of process parameter combinations can be completed, which can take into account both design and production. However, many small and medium-sized casting enterprises in China know little about computer simulation technology or are restricted by other factors. The actual casting production effect largely depends on the level and experience of the mold designer. There is a lack of theoretical understanding of the principles of the casting process. The design of molds usually requires several trial production runs, which are costly and inefficient. Defects generated during the casting process are also analyzed based on experience, and it is impossible to accurately determine the factors causing the defects. The product design and development cycle is too long.
2. Research Status of Bucket Teeth at Home and Abroad
2.1 Research Status of Bucket Teeth Material Selection
In 1873, the United States developed the world’s first excavator, which was powered by steam. In 1900, an excavator powered by a diesel engine was developed and put into production. In 1954, Germany completed the development of a fully hydraulic system excavator. In 1961, Japan conducted in-depth exploration and research on hydraulic technology. In 1985, Japan combined computer technology, hydraulics, and excavators to develop and design a new type of hydraulic excavator. Since the birth of the excavator, enterprises and scholars from all over the world have been researching and exploring the materials of excavator bucket teeth to develop better-performing materials, which is of great significance for promoting industrial production. Currently, according to material composition and organizational differences, bucket teeth materials are classified into the following categories: wear-resistant white cast iron, low-alloy wear-resistant steel, quasi-bainitic steel, high-manganese steel, and modified high-manganese steel.
As the main working parts of excavation work, bucket teeth are the first to come into contact with materials during the excavation operation of an excavator. The frequent impact and friction between bucket teeth and materials cause bucket teeth to bear great impact loads and some bending moments during excavation work. Wear-resistant white cast iron has high hardness but is brittle and prone to brittle fracture. Low-alloy wear-resistant steel has high hardness and good wear resistance. After appropriate heat treatment, it also has good toughness. Quasi-bainitic steel has high hardness but poor toughness. When subjected to severe impact and bending moment, high-manganese steel will greatly increase its hardness. This characteristic is called work hardening and is more suitable for complex excavation work, so it is selected as the traditional bucket teeth material.
However, when bucket teeth made of high-manganese steel excavate softer materials such as soil and coal, the surface of the bucket teeth cannot achieve the ideal hardness through work hardening due to the low impact load. Since the hardness of high-manganese steel bucket teeth is inherently low, their wear resistance is relatively general when excavating low-hardness materials. In addition, recent scientific research has shown that when the impact load is too high, the wear resistance of high-manganese steel will be greatly reduced due to the limited increase in hardness through work hardening. Under ultra-high impact load conditions, abrasive wear with plowing is the main wear form of bucket teeth. At this time, the work hardening layer of high-manganese steel occurs in the subsurface rather than on the top surface, resulting in poor hardness and wear resistance on the top surface. Moreover, although the work hardening mechanism of high-manganese steel brings about an increase in hardness, it has the side effect of reducing toughness. During excavation operations, if the resistance is too great, bending deformation may occur, and the connection between the tail of the bucket teeth and the bucket is also prone to deformation and forking, resulting in reduced service life of the bucket teeth.
Based on the above discussion of the advantages and disadvantages of high-manganese steel bucket teeth, enterprises and scholars at home and abroad have conducted deeper exploration and research on high-manganese steel materials, mainly by alloying high-manganese steel to develop bucket teeth materials with stronger mechanical properties. Some foreign leading enterprises in mining excavators have added alloy elements such as chromium, molybdenum, and nickel to bucket teeth materials. The addition of such elements effectively improves the wear resistance of bucket teeth castings, allowing them to be used for longer under the same working conditions. Domestic excavator enterprises have added different alloy elements such as manganese, vanadium, and titanium to bucket teeth materials after drawing lessons from the processing methods of foreign enterprises for bucket teeth materials. Some enterprises also add expensive rare earth elements to bucket teeth materials. After actual excavation operations, it was found that the above elements can enhance the performance of bucket teeth castings and can reduce the service time to a certain extent, thereby improving economic benefits. At the same time, relevant domestic scholars are also conducting in-depth exploration and research on bucket teeth materials. Wang Xiong added vanadium and rare earth elements to bucket teeth materials and added them in batches during the melting process to ensure that vanadium and rare earth elements can be evenly distributed in the material. In this way, the toughness of the produced material has been improved to a certain extent, and it is not easy to break during excavation operations, thereby extending the service life. Guo Qingfeng et al. also added different alloy elements to the bucket teeth material in the same way and developed a new type of bucket teeth material. Due to the addition of chromium, vanadium, and titanium elements, the hardness and wear resistance of the bucket teeth have been significantly improved, and thermal cracking is less likely to occur during the casting production process, which reduces the scrap rate to a certain extent and improves economic benefits. Zhu Fuhong et al. added various transition metal elements such as chromium, molybdenum, nickel, and niobium to high-manganese steel. The addition of these elements allows the bucket teeth material to have good processing hardening ability while also having good toughness, greatly improving the brittleness of high-manganese steel due to processing hardening.
The bucket teeth produced by Yuchen Foundry are made of ZGMn13Mo. In actual use, it was found that the tail of the bucket teeth is prone to forking and bending at the connection with the bucket. Professor Cai Zhihui from the School of Mechanical Engineering, Taiyuan University of Science and Technology, proposed replacing part of the Mo element in the material with Cu element. After appropriate heat treatment, this material can meet the quality requirements of high wear resistance, high toughness, and high strength. Moreover, due to the reduction in Mo content, material costs are also greatly reduced, resulting in better economic benefits.
2.2 Research Status of Bucket Teeth Manufacturing Methods
There are many types of bucket teeth manufacturing methods, and the mainstream manufacturing methods include the following: sand casting, forging, lost foam casting, bimetallic liquid composite casting, and investment casting.
(1) Sand Casting
To cope with various working conditions, different types and structures of bucket teeth have been derived. Sand casting can meet the manufacturing requirements of most bucket teeth, especially large-volume castings. Sand casting is convenient and efficient for such castings. However, when sand casting is used to produce bucket teeth castings with complex structures, the final product may have significant differences from the part drawing. This is because when the structure of the bucket teeth casting is complex, more sand cores need to be set in the mold to ensure the accuracy of the appearance of the casting. More sand cores mean that more gas will be generated during the pouring process, resulting in poor surface quality of the final produced casting and difficult to ensure the quality of detailed parts, with a high scrap rate.
(2) Bimetallic Liquid Composite Casting
Some bucket teeth work in harsh environments and need to excavate complex materials. For such bucket teeth castings, the bimetallic liquid composite casting method can be used for production. Bucket teeth produced by this manufacturing method have excellent performance but high costs. Japanese researchers have conducted in-depth research on this manufacturing method and developed a new type of bucket teeth. This manufacturing method first covers high-hardness metal over low-hardness metal and then forges the high-hardness metal to the outside and the low-hardness metal to the inside through subsequent forging, resulting in excellent comprehensive performance. This forming process is also mentioned in the literature. Shang Y et al. prepared bimetallic composites using a liquid-liquid composite casting method with a good interface and focused on studying the evolution of the interface with the increase in pouring time interval. The results showed that when the pouring interval is 3 seconds, the melt mixes. When the pouring interval is 10 seconds, a transition zone appears at the interface, and a good metallurgical bond is obtained. When the pouring interval is 20 seconds, a discontinuous oxide layer appears at the interface. The gap in the oxide layer forms a channel for transmitting SiC particles.
(3) Lost Foam Casting
This bucket teeth manufacturing method has many application examples in domestic and foreign excavator enterprises because it has more advantages compared to traditional bucket teeth forming processes. Firstly, modeling is convenient, and the stripping process can be omitted. Moreover, modeling does not need to consider the draft angle, which can better ensure that the appearance of the casting is consistent with the part design drawing, and the efficiency is high. With the development of the mining industry, this process has also been improved. For now, this forming process has become mature. Based on the comprehensive advantages of lost foam casting, this bucket teeth manufacturing method will be adopted by more and more enterprises in the future. The literature mentions that a ZGMn13 bucket tooth with a single piece weight of up to 125 kg was obtained using lost foam casting, and the process performance is relatively good. Ramesh R et al. conducted in-depth research on the lost foam casting process. This casting process eliminates the difficulties of casting product design considerations. The lost foam casting process ensures the quality of castings through flexible methods. It is used to manufacture complex metal parts with less production time. In their experimental research, aluminum 6082 and silicon were prepared by the lost foam casting method. In addition, in the manufacture of low-carbon alloy steel bucket teeth, lost foam casting technology has obvious advantages compared to traditional water glass sand casting.
(4) Investment Casting
Compared with other types of manufacturing methods, this bucket teeth manufacturing method has the following advantages: The produced bucket teeth castings have accurate appearances with small errors, can produce bucket teeth with complex structures, have a low scrap rate, and can meet the production needs of castings made of different materials. Compared with lost foam casting technology, investment casting uses hollow shell pouring, and the carbon content of castings will be more stable, which can effectively reduce casting defects. Foreign enterprises generally use investment casting to produce key parts with high prices and high precision requirements. In contrast, most domestic enterprises use this manufacturing method to produce parts with simple structures, such as bucket teeth. The bucket teeth produced by Sanli Casting Co., Ltd., and Liugong Machinery Co., Ltd., using the investment precision casting process have good mechanical properties. During the investment precision casting process, surface decarburization frequently occurs, which significantly affects the quality of low-carbon steel bucket teeth. In addition, investment casting can also produce castings other than bucket teeth. Ren S et al. produced single-crystal turbine blades by investment casting. The final size of the blade depends on the cumulative effect of thermal contraction at different stages, including high-temperature alloys, mold shells, and ceramic cores. To clarify the influence of these stages on the blade size, first, the heat transfer coefficients calculated by the reverse heat conduction analysis were used to simulate directional solidification. By extracting and mapping the final physical fields from the previous stage to the next stage, four consecutive constraint removal processes were performed at different time points. Subsequently, a time-varying model for the entire process of directional solidification and constraint removal was established. The error of extraction and mapping is always less than 0.002 mm in all three directions, confirming the feasibility of data transmission. Secondly, the size deviation patterns of the castings after sequentially removing the mold shell, process ribs, grain selectors, and ceramic core constraints were analyzed, focusing on the dimensional accuracy of the airfoil while ignoring the dovetail produced by machining. The final average deviations of airfoil sections 1, 2, and 3 are 0.1896 mm, 0.1723 mm, and 0.1909 mm, respectively, and the maximum deviations always occur at the trailing edge near the blade tip.