This article focuses on the nitrogen porosity defects in gray cast iron produced by iron – clad sand casting. Through EDS spectrometer for qualitative and quantitative analysis, combined with the casting production process, the causes of nitrogen pores are explored. Measures such as replacing coated sand, adjusting new sand proportion, and managing recycled sand separately are implemented. In the production process, improvements like adding exhaust plugs and adjusting temperature and time parameters are made. The results show that these measures effectively reduce the defect risk, as demonstrated by the successful production of a large number of defect – free products.
1. Introduction
Iron – clad sand casting is a widely used casting process that offers certain advantages. However, like any manufacturing process, it is not without its challenges. One of the significant issues faced is the formation of nitrogen porosity defects in the castings. These defects can have a detrimental impact on the quality and performance of the final product. Understanding the root causes of these defects and implementing effective solutions is crucial for the success of the casting operation.
2. Casting Process Overview
2.1 Melting and Molding Process
The casting production utilizes an intermediate frequency induction furnace. The raw materials include recycled materials, scrap steel, and additives. The proportion of scrap steel is about 60% – 70%, with the rest being recycled materials such as risers, gates, and machined parts. The scrap steel has specific quality requirements, including a carbon content fraction greater than 98%, sulfur content ≤ 0.5%, ash content ≤ 2%, volatile matter ≤ 1%, and a particle size of 1 – 5 mm.
The charging sequence of the furnace materials is as follows: 50% recycled material (iron filings) is added to the furnace bottom first, followed by 70% of the carburizing agent and then the scrap steel. During the addition of the scrap steel, the remaining 30% of the carburizing agent is added to the furnace in two portions. The melting temperature is maintained at 1500 – 1530°C, and a high – temperature static treatment is carried out at 1530 – 1550°C for 5 minutes with repeated slag removal. The tapping temperature of the molten iron is 1490 – 1530°C, and a 75″ ferrosilicon is used for inoculation treatment during tapping. The pouring temperature of the last piece is not lower than 1360°C, and the pouring time for the entire ladle does not exceed 15 minutes.
The old sand used is regenerated coated sand, and the new sand is sourced from Tongliao, Inner Mongolia. The coated sand is regenerated using a thermal method, and its main process includes steps such as old sand crushing, screening, magnetic separation, thermal regeneration, micro – powder removal, cooling, storage, and inspection. The coated sand has specific mechanical properties, such as an ambient tensile strength ≥ 2.5 MPa, an ambient flexural strength ≥ 6 MPa, a hot tensile strength ≥ 1.3 MPa, a hot flexural strength ≥ 3.8 MPa, a burning loss ≤ 2.6%, a gas evolution amount ≤ 20 mL, and a melting point of 95 – 110°C.
2.2 Pouring System
The pouring system is designed to ensure a smooth flow of molten iron into the mold cavity. The width of the runner is consistent with that of the ingate, and the thickness is determined according to the wall thickness of the casting flange. A sprue well is provided to buffer the molten iron entering the cavity and prevent turbulent flow. The pouring cup is funnel – shaped, and a 15PPI ceramic filter is installed inside. The pressure angle formed by the cup top and the maximum outer circle of the casting upper plane is not less than 40°. The pouring system is semi – closed, with a ratio of ∑Sₙₑ : ∑Sₑₓ : ∑Sₛₜ = 1:4.17:2.04. Depending on the product structure, 4 or 5 ingates are provided, and the cross – sectional area of a single ingate is not less than 240 mm². The single – type pouring time of the casting does not exceed 25 seconds, and two stress grooves are provided on each side of the ingate for easy removal.
3. Defect Analysis
3.1 EDS Spectrometer Analysis
The defect surface scanning map reveals the presence of dendritic crystals at the defect site. The defect has an irregular shape, is perpendicular to the casting surface, and extends 2 – 5 mm into the casting. EDS analysis shows the presence of elements such as N, C, Fe, O, and Si. The presence of nitrogen is a key indicator of potential nitrogen porosity defects.
3.2 Nitrogen Porosity Formation Mechanism
Nitrogen in the molten iron forms an interstitial solid solution. During the solidification process of the molten iron, as the temperature decreases, the solubility of nitrogen also decreases. In the iron – clad sand casting process, due to the rapid cooling rate, the surface layer of the molten iron solidifies quickly, forming a shell, and the nitrogen gas cannot be discharged smoothly, resulting in the formation of nitrogen porosity defects.
3.3 Causes of Nitrogen Porosity
3.3.1 Raw Materials
- Scrap Steel: Different types of scrap steel contain varying amounts of nitrogen. For example, ordinary carbon steel, high – manganese steel, etc., have nitrogen contents in the range of about 40 – 60 ppm, threaded steel has about 90 ppm, and guide rail steel has about 110 – 120 ppm.
- Carburizing Agent: Different types of carburizing agents also have different nitrogen contents. Coal – based carburizing agents have about 2000 – 7000 ppm (0.2% – 0.7%), ordinary calcined petroleum coke carburizing agents generally have about 1000 ppm, high – temperature calcined petroleum coke carburizing agents have 300 – 500 ppm, and graphitized carburizing agents do not exceed 300 ppm.
- Coated Sand: The coated sand contains phenolic resin, curing agent (usually hexamethylenetetramine), and additives. During the heating and curing process of the coated sand and the pouring process, hexamethylenetetramine decomposes at 230°C and above, releasing a large amount of NH₃, which can contribute to the formation of nitrogen porosity defects.
3.3.2 Production Process
The production process also plays a role in the formation of nitrogen porosity defects. For example, if the gas cannot be effectively discharged during the solidification process of the coated sand, it can lead to the formation of pores. Additionally, if the temperature and time parameters of the casting process are not properly controlled, it can affect the solubility and diffusion of nitrogen, thereby increasing the likelihood of defect formation.
4. Improvement Measures
4.1 Coated Sand Quality Improvement
4.1.1 Resin and Hexamethylenetetramine Quality
Improving the quality of phenolic resin and hexamethylenetetramine can reduce the risk of nitrogen porosity. Higher quality resins and curing agents can result in more stable chemical reactions during the coating process, reducing the release of nitrogen – containing gases.
4.1.2 New Sand Proportion Adjustment
The proportion of new sand is adjusted from 5% – 20% to 20% – 40%. This increase in new sand proportion reduces the amount of recycled sand used, thereby reducing the residual nitrogen content in the sand mixture. The use of more new sand can also improve the permeability and mechanical properties of the sand, facilitating better gas discharge during the casting process.
4.1.3 Separate Management of Recycled Sand
Since the performance requirements and particle sizes of the coated sand used in different production lines are different, and the amount of new sand added is also different, mixing the recycled sand from different lines can lead to process problems. Therefore, it is necessary to manage the recycled sand of the shell line and the iron line separately to ensure the consistency and stability of the sand used in each production line.
4.2 Production Process Improvement
4.2.1 Addition of Exhaust Channels
Adding exhaust channels in the mold and on the iron type is beneficial for the gas discharge during the curing process of the coated sand and also improves the filling quality of the coated sand. These exhaust channels provide a path for the gas to escape, reducing the pressure inside the mold and preventing the formation of pores due to trapped gas.
4.2.2 Temperature Adjustment
The decomposition temperature of hexamethylenetetramine in the coated sand is 230°C. In the iron – clad sand casting process, the curing temperature of the coated sand is generally 220 – 240°C. To ensure efficient gas release, the mold temperature is set to 230 – 250°C, and the iron type temperature is set to 240 – 280°C. This temperature adjustment accelerates the gas release from the coated sand, reducing the amount of gas trapped in the casting and minimizing the formation of nitrogen porosity defects.
4.2.3 Extension of Time Interval
The time interval from the start of coating to the start of pouring is extended from 10 minutes to not less than 20 minutes. This extended time allows the gas to be more effectively discharged from the coated sand and the molten iron, reducing the amount of gas that can invade the molten iron and form pores. As a result, the formation of casting porosity defects is reduced.
5. Results and Discussion
After implementing the above improvement measures, a large number of products were continuously produced. Through inspection and monitoring, it was found that no nitrogen porosity defects occurred. This indicates that the measures taken to address the nitrogen porosity defects were effective. The adjustment of the coated sand quality and the improvement of the production process worked in harmony to ensure the quality of the castings.
The increase in the proportion of new sand improved the physical properties of the sand mixture, facilitating better gas discharge. The separate management of recycled sand ensured the stability of the sand used in each production line, preventing process problems caused by inconsistent sand quality. The addition of exhaust channels provided an effective path for gas escape, and the temperature and time adjustments optimized the gas release process during the casting process.
6. Conclusion
In conclusion, the nitrogen porosity defects in gray cast iron produced by iron – clad sand casting can be effectively addressed through a combination of measures. By analyzing the causes of the defects using EDS spectrometer and considering the casting production process, appropriate improvement measures can be implemented. These measures include improving the quality of the coated sand, adjusting the proportion of new sand, separately managing recycled sand, and making improvements in the production process such as adding exhaust channels and adjusting temperature and time parameters. The successful implementation of these measures has been demonstrated by the production of a large number of defect – free products, which is of great significance for ensuring the quality and performance of the castings and the success of the casting operation. Future research could focus on further optimizing these measures and exploring other potential factors that may affect the formation of nitrogen porosity defects to continuously improve the casting quality.
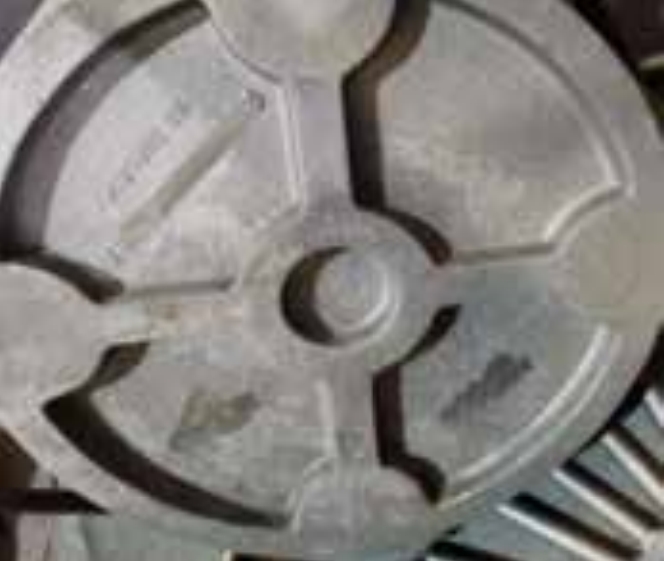