This article focuses on the nitrogen porosity defects in gray cast iron produced by iron-clad sand casting. Through qualitative and quantitative analysis using EDS spectrometer and in combination with casting production technology, the formation reasons of nitrogen pores are explored. Measures such as replacing coated sand, adjusting new sand amount, and separately managing recycled sands are implemented. Additionally, production process improvements like adding exhaust plugs and modifying temperature and time parameters are carried out. The results show significant defect reduction, with no nitrogen porosity defects in a large number of continuously produced products.
1. Introduction
Iron-clad sand casting is a widely used manufacturing process, especially for producing components like automotive brake drums. The resulting castings often have excellent mechanical properties and microstructure due to the unique cooling characteristics of the process. However, the occurrence of defects, such as nitrogen porosity, can significantly affect the quality and performance of the castings. Understanding the root causes of these defects and implementing effective improvement measures is crucial for the casting industry.
2. Casting Process Overview
- 2.1 Melting and Molding Process
- The melting process utilizes an intermediate frequency induction furnace with a specific charge composition. The raw materials include a certain percentage of return scraps, waste steel, and carbon raisers. The charge is added in a particular sequence to ensure proper melting and carbon content control. The molten iron is then treated with a specific temperature range and holding time, followed by inoculation treatment before pouring.
- The molding process uses recycled coated sand and new sand from Inner Mongolia. The coated sand undergoes a thermal regeneration process with defined properties such as tensile and flexural strengths, burn-off loss, and gas evolution. The new sand addition ratio and the properties of the recycled sand play important roles in the final casting quality.
- 2.2 Pouring System
- The pouring system is designed as a semi-closed type with specific ratios of inner runner, sprue, and runner areas. It has features like a funnel-shaped pouring cup with a ceramic filter to ensure smooth metal flow and slag removal. The number and size of inner runners are determined according to the product structure, and stress grooves are provided for easy removal of the pouring system after casting.
3. Defect Analysis
- 3.1 EDS Spectral AnalysisElementPercentageN49.5C28.58Fe12.71O8.87Si0.34The defect area shows irregular shapes with vertical penetration into the casting. The presence of elements like N, C, Fe, O, and Si indicates a complex defect structure.
- 3.2 Nitrogen Porosity Formation Mechanism
- Nitrogen in the molten iron forms an interstitial solid solution. As the temperature decreases during solidification, the solubility of nitrogen drops. In the iron-clad sand casting process, the rapid cooling rate causes the surface layer of the molten iron to solidify quickly, trapping nitrogen and forming pores.
- 3.3 Reasons for Nitrogen Porosity
- 3.3.1 Raw Materials
- Steel Scrap: Different types of steel scraps have varying nitrogen contents. For example, ordinary carbon steel and high manganese steel contain a certain amount of nitrogen, which can contribute to the overall nitrogen level in the molten iron.Steel TypeNitrogen Content (ppm)Ordinary Carbon Steel40 – 60High Manganese Steel40 – 60Thread Steel90Guide Rail Steel110 – 120
- Carbon Raiser: Different carbon raisers also have different nitrogen contents. Coal-based carbon raisers have a relatively high nitrogen content, while some other types like graphite-based carbon raisers have lower levels.Carbon Raiser TypeNitrogen Content (ppm)Coal-based2000 – 7000Ordinary Calcined Petroleum Coke1000High-temperature Calcined Petroleum Coke300 – 500Graphitizednot more than 300
- 3.3.2 Coated Sand
- The coated sand contains phenolic resin and a curing agent (urotropine). Urotropine decomposes at a certain temperature, releasing ammonia, which can increase the nitrogen content in the casting environment. The resin content and the proportion of urotropine in the coated sand formula can affect the nitrogen porosity formation.
- 3.3.1 Raw Materials
4. Improvement Measures
- 4.1 Coated Sand Quality Improvement
- 4.1.1 Resin and Urotropine Quality Control
- By ensuring high-quality phenolic resin and urotropine, the decomposition behavior and gas release can be better controlled, reducing the potential for nitrogen porosity.
- 4.1.2 New Sand Proportion Adjustment
- Increasing the proportion of new sand from 5% – 20% to 20% – 40% helps reduce the residual nitrogen content in the recycled sand, thereby decreasing the risk of nitrogen porosity.
- 4.1.3 Separate Management of Recycled Sands
- Since the shell line and iron line have different requirements for coated sand, separating their recycled sands can avoid process problems caused by sand mixing.
- 4.1.1 Resin and Urotropine Quality Control
- 4.2 Production Process Improvement
- 4.2.1 Exhaust Channel Addition
- Adding exhaust channels in the mold and iron type。
- 4.2.2 Temperature Adjustment
- Increasing the mold temperature to 230 – 250°C and the iron type temperature to 240 – 280°C helps accelerate the gas release of the coated sand, as urotropine decomposes more effectively at these temperatures.
- 4.2.3 Pouring Time Extension
- Extending the time from the start of sanding to pouring from 10 minutes to at least 20 minutes allows more time for the gas to escape, reducing the formation of gas pores in the casting.
- 4.2.1 Exhaust Channel Addition
5. Conclusion
Through a comprehensive approach of adjusting the raw materials (coated sand and its components) and improving the production process (adding exhaust channels, adjusting temperatures, and extending pouring time), significant improvements in casting quality have been achieved. The continuous production of a large number of products without nitrogen porosity defects demonstrates the effectiveness of these measures. This study provides valuable insights and practical solutions for the casting industry to address nitrogen porosity issues and improve the overall quality of castings.
6. Visual Representation of the Casting Process and Defects
6.1 The Casting Process
The casting process involves multiple steps, each crucial for the final product quality. The first step is the melting process in the intermediate frequency induction furnace. As shown in Figure 1, the furnace is loaded with a specific combination of return scraps, waste steel, and carbon raisers. The raw materials are carefully added in a particular sequence to ensure proper melting and carbon content control. The molten iron is then treated with a specific temperature range and holding time to achieve the desired chemical composition and properties.
After the melting process, the molten iron is transferred to the molding process. The molding process uses recycled coated sand and new sand from Inner Mongolia. The coated sand undergoes a thermal regeneration process to regain its properties. As depicted in Figure 2, the coated sand is prepared and mixed with new sand in a specific ratio. The new sand addition ratio and the properties of the recycled sand play important roles in the final casting quality.
The pouring system is another critical component of the casting process. It is designed as a semi-closed type with specific ratios of inner runner, sprue, and runner areas. As shown in Figure 3, the pouring cup is funnel-shaped and contains a ceramic filter to ensure smooth metal flow and slag removal. The number and size of inner runners are determined according to the product structure, and stress grooves are provided for easy removal of the pouring system after casting.
6.2 Defect Analysis Visualization
6.2.1 EDS Spectral Analysis Results
The EDS spectral analysis provides valuable information about the defect area. The presence of elements like N, C, Fe, O, and Si indicates a complex defect structure. The results are presented in a graphical format as shown in Figure 4. The peaks corresponding to different elements clearly show their relative proportions in the defect area.
6.2.2 Nitrogen Porosity Formation Visualization
The nitrogen porosity formation mechanism can be better understood through visual representation. As the temperature decreases during solidification, the solubility of nitrogen drops. In the iron-clad sand casting process, the rapid cooling rate causes the surface layer of the molten iron to solidify quickly, trapping nitrogen and forming pores. This process is illustrated in Figure 5. The figure shows the solidification front and the trapped nitrogen gas forming pores.
7. In-depth Discussion on Raw Materials and Their Impact on Defects
7.1 Steel Scrap Analysis
The type and quality of steel scrap used in the casting process have a significant impact on the final product. Different types of steel scraps have varying nitrogen contents. For example, ordinary carbon steel and high manganese steel contain a certain amount of nitrogen, which can contribute to the overall nitrogen level in the molten iron. The impurities and alloying elements in the steel scrap can also affect the microstructure and properties of the casting. As shown in Table 1, the nitrogen content and other characteristics of different steel scraps are compared.
Steel Type | Nitrogen Content (ppm) | Other Characteristics |
---|---|---|
Ordinary Carbon Steel | 40 – 60 | Contains certain impurities |
High Manganese Steel | 40 – 60 | Higher manganese content |
Thread Steel | 90 | Different microstructure |
Guide Rail Steel | 110 – 120 | Higher strength requirements |
7.2 Carbon Raiser Analysis
Carbon raisers are used to adjust the carbon content in the molten iron. However, different carbon raisers also have different nitrogen contents. Coal-based carbon raisers have a relatively high nitrogen content, while some other types like graphite-based carbon raisers have lower levels. The choice of carbon raiser can affect the nitrogen porosity formation. As presented in Table 2, the nitrogen content and other properties of different carbon raisers are compared.
Carbon Raiser Type | Nitrogen Content (ppm) | Other Properties |
---|---|---|
Coal-based | 2000 – 7000 | Higher reactivity |
Ordinary Calcined Petroleum Coke | 1000 | Moderate reactivity |
High-temperature Calcined Petroleum Coke | 300 – 500 | Good thermal stability |
Graphitized | not more than 300 | High graphitization degree |
8. Detailed Explanation of Coated Sand and Its Role in Defect Formation and Prevention
8.1 Coated Sand Composition and Properties
The coated sand contains phenolic resin and a curing agent (urotropine). The resin provides the binding strength and the urotropine acts as a curing agent. The properties of the coated sand, such as tensile and flexural strengths, burn-off loss, and gas evolution, are crucial for the casting process. The coated sand undergoes a thermal regeneration process to regain its properties. As shown in Table 3, the properties of the coated sand are listed.
Property | Value |
---|---|
Tensile Strength (MPa) | ≥2.5 (at room temperature), ≥1.3 (at high temperature) |
Flexural Strength (MPa) | ≥6 (at room temperature), ≥3.8 (at high temperature) |
Burn-off Loss (%) | ≤2.6 |
Gas Evolution (mL) | ≤20 |
8.2 Urotropine Decomposition and Its Impact on Nitrogen Porosity
Urotropine decomposes at a certain temperature, releasing ammonia, which can increase the nitrogen content in the casting environment. The resin content and the proportion of urotropine in the coated sand formula can affect the nitrogen porosity formation. The decomposition process of urotropine is shown in Figure 6. The figure illustrates how urotropine breaks down into ammonia and other products at a specific temperature.
9. Further Elaboration on Improvement Measures and Their Mechanisms
9.1 Coated Sand Quality Improvement Mechanisms
9.1.1 Resin and Urotropine Quality Control Mechanisms
By ensuring high-quality phenolic resin and urotropine, the decomposition behavior and gas release can be better controlled. High-quality resin has a more stable structure and less likely to release unwanted gases. Urotropine with proper purity and quality will decompose in a more predictable manner, reducing the potential for nitrogen porosity. This is achieved through strict quality control measures during the manufacturing process of resin and urotropine.
9.1.2 New Sand Proportion Adjustment Mechanisms
Increasing the proportion of new sand from 5% – 20% to 20% – 40% helps reduce the residual nitrogen content in the recycled sand. New sand has a lower nitrogen content compared to recycled sand. By increasing the new sand proportion, the overall nitrogen content in the sand mixture is decreased, thereby decreasing the risk of nitrogen porosity. This is because the nitrogen in the recycled sand is diluted by the added new sand.
9.1.3 Separate Management of Recycled Sands Mechanisms
Since the shell line and iron line have different requirements for coated sand, separating their recycled sands can avoid process problems caused by sand mixing. The shell line and iron line may have different operating conditions and requirements for sand properties. Mixing their recycled sands can lead to inconsistent sand properties and affect the casting quality. By separating the recycled sands, each line can use sand that meets its specific requirements, ensuring better casting quality.
9.2 Production Process Improvement Mechanisms
9.2.1 Exhaust Channel Addition Mechanisms
Adding exhaust channels in the mold and iron type利于覆膜砂固化时的气体排出,同时利于覆膜砂充型,提高射砂质量. The exhaust channels provide a path for the gas to escape during the curing process of the coated sand. This helps to reduce the pressure build-up inside the mold and allows the coated sand to fill the mold more evenly. The improved gas escape also reduces the formation of gas pores in the casting.
9.2.2 Temperature Adjustment Mechanisms
Increasing the mold temperature to 230 – 250°C and the iron type temperature to 240 – 280°C helps accelerate the gas release of the coated sand, as urotropine decomposes more effectively at these temperatures. The higher temperatures increase the rate of decomposition of urotropine, which leads to more rapid gas release. This helps to reduce the nitrogen content in the casting environment and decreases the risk of nitrogen porosity.
9.2.3 Pouring Time Extension Mechanisms
Extending the time from the start of sanding to pouring from 10 minutes to at least 20 minutes allows more time for the gas to escape. During this extended period, the gas has more time to diffuse out of the sand and the molten iron. This reduces the amount of gas trapped in the casting and decreases the formation of gas pores.
10. Case Studies and Practical Applications of the Improvement Measures
10.1 Case Study 1: A Casting Factory Implementing the Measures
A casting factory was experiencing significant nitrogen porosity defects in their iron-clad sand castings. They decided to implement the improvement measures described in this article. First, they focused on improving the coated sand quality. They sourced high-quality phenolic resin and urotropine and adjusted the new sand proportion to 20% – 40%. They also separated the recycled sands of the shell line and iron line. In the production process, they added exhaust channels in the mold and iron type, adjusted the temperatures as recommended, and extended the pouring time. After implementing these measures, the factory observed a significant reduction in nitrogen porosity defects. The number of defective castings decreased from a high percentage to almost zero in a relatively short period.
10.2 Case Study 2: Another Casting Facility’s Experience
Another casting facility had similar issues with nitrogen porosity in their castings. They adopted a similar approach but also made some additional adjustments based on their specific production conditions. They found that by closely monitoring the quality of the raw materials and making slight modifications to the improvement measures, they could achieve even better results. For example, they optimized the temperature adjustment based on the actual heat transfer characteristics of their equipment. This led to a further reduction in nitrogen porosity defects and an improvement in the overall quality of their castings.
11. Future Perspectives and Research Directions
11.1 Potential for Further Optimization of the Improvement Measures
Although the current improvement measures have shown significant effectiveness, there is still room for further optimization. For example, the quality control of raw materials could be further enhanced. This could involve more precise analysis and selection of steel scraps and carbon raisers to ensure even lower nitrogen contents. The coated sand formulation could also be further refined to better control the gas release and improve the casting quality.
11.2 Exploration of New Technologies and Materials for Casting
In the future, new technologies and materials may offer alternative solutions to the nitrogen porosity problem. For example, the development of new resins with lower nitrogen content and better curing properties could be explored. New casting techniques that provide better control over the solidification process and gas escape could also be investigated. These new technologies and materials could potentially revolutionize the casting industry and provide more efficient and effective ways to produce high-quality castings without nitrogen porosity defects.
12. Conclusion
In conclusion, the nitrogen porosity defects in iron-clad sand castings are a significant concern for the casting industry. Through a comprehensive understanding of the casting process, defect analysis, and implementation of improvement measures, significant progress has been made in reducing these defects. The visual representation of the casting process and defects, in-depth discussion on raw materials, detailed explanation of coated sand, further elaboration on improvement measures, case studies, and future perspectives all contribute to a more complete understanding of the issue and its solutions. By continuously exploring and applying new knowledge and techniques, the casting industry can further improve the quality of its products and meet the increasing demands for high-quality castings.
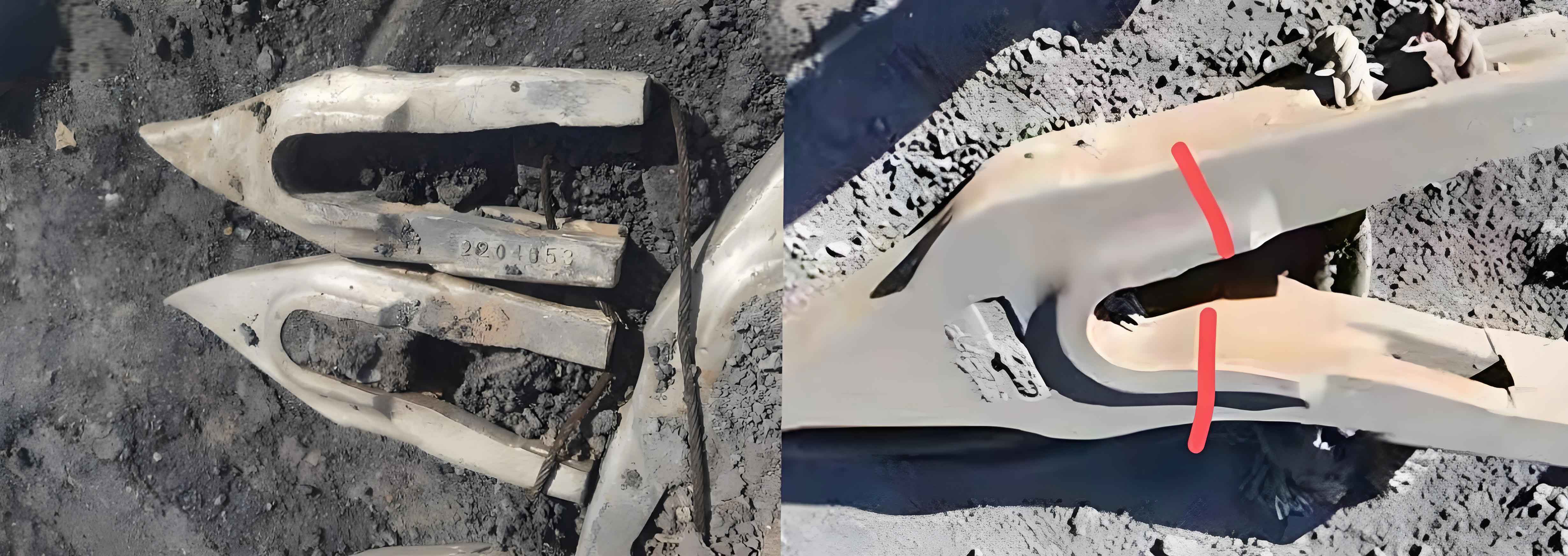