Abstract
The analysis and prevention of defects in flywheel housings produced through lost foam casting, leveraging the principles of the lost foam casting process and the structural characteristics of flywheel housing castings. By controlling the EPS foam bulk density and molding process, adding support ribs, optimizing coating formulation and molding-boxing processes, improving gating systems and pouring operations, and enhancing overall management, we aim to prevent defects such as deformation, slag inclusion, iron-encased sand, and cold shuts. These measures help increase the process yield and product qualification rate of castings.
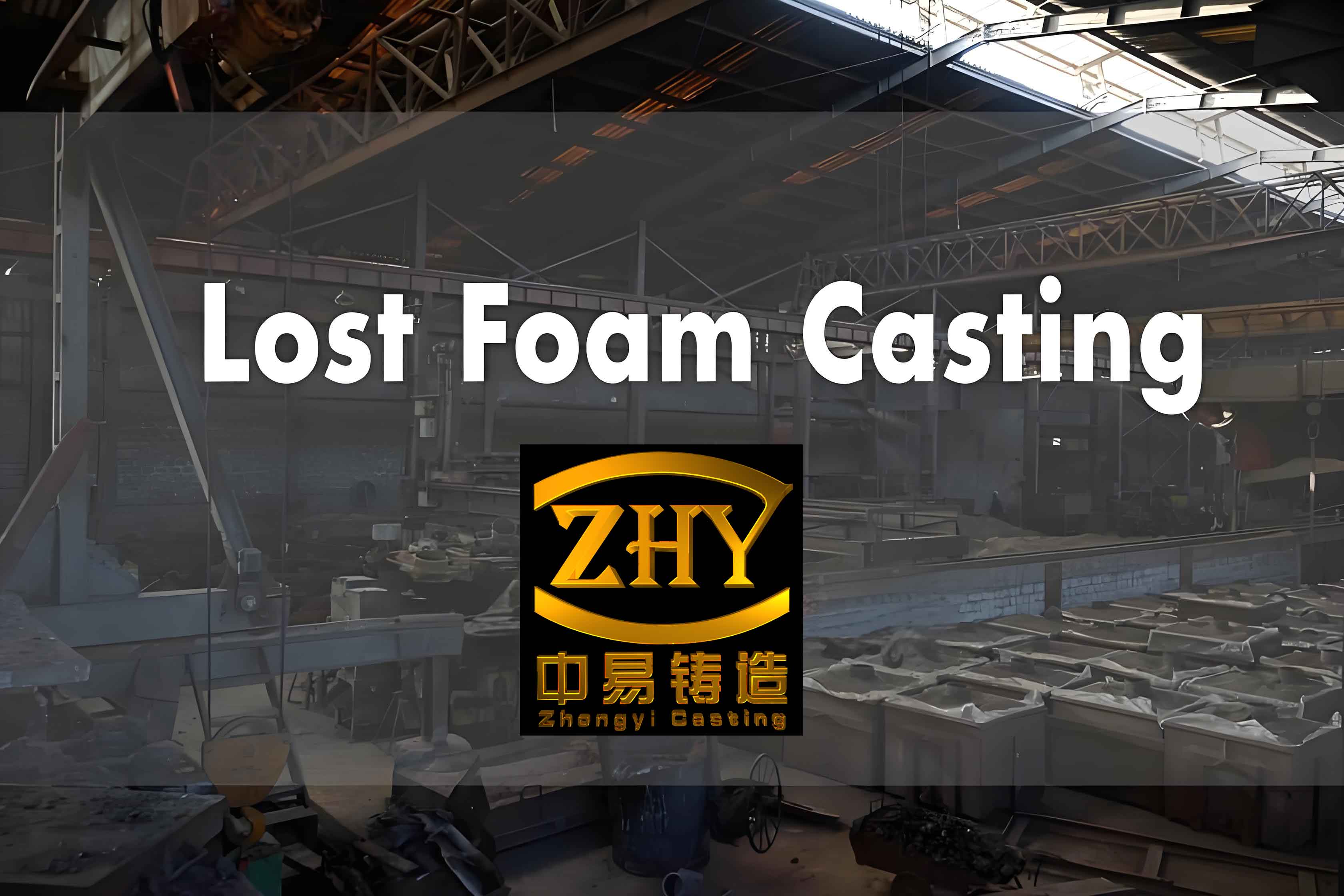
1. Introduction
Over the past half-century, lost foam casting technology has seen significant promotion and rapid development, evolving into a mature stage. Products have transitioned from simple castings to complex shapes, encompassing a wider range of materials and varying in weight from a few dozen grams to several dozen tons. One notable feature of lost foam casting is its collective teamwork, where a qualified casting necessitates multiple processes and seamless cooperation among numerous workers. Therefore, defects in castings gradually accumulate, amplify, and extend throughout the production process, ultimately leading to casting rejection. To fundamentally address casting rejection, a thorough analysis of the causes of deformation, slag inclusion, iron-encased sand, and cold shut defects in flywheel housing castings is crucial. Through process experimentation, gradual improvement, and optimization, we can establish more rational and scientific production processes and standards. By strictly enforcing, controlling, and supervising these processes, we can ensure stable product quality, high process yield, and product qualification rates.
2. Deformation Defects and Control
2.1 Causes
Three specifications of flywheel housings made of HT250 material, with a primary wall thickness of 6mm. Flywheel housing castings are thin-walled shell castings with large internal cavities and discontinuous structures. They are prone to deformation during molding, drying, assembly, coating, and vibrating packing. During trial production, the reject rate for deformation defects was approximately 35%.
2.2 Process Improvements
Casting deformation primarily results from improper operations and inadequate control during molding, drying, assembly, coating, and vibrating packing. These include factors such as foam model removal control, drying arrangement, coating application techniques, and inconsistent forces applied to the foam model during vibrating packing. To address these issues, several measures were implemented:
- Strict quality control of the pre-foamed density and particle size of the foam pattern, using high-strength, low-density beads for molding.
- Improved coating formulation to enhance the foam pattern’s resistance to deformation and adhesion.
- Increased foam pattern strength.
- Added support ribs to the foam pattern’s upper opening, using the counterforce generated by the support ribs to balance the forces applied by the coating and sand during immersion coating and vibrating packing, thereby preventing deformation.
3. Slag Inclusion Defects and Control
3.1 Causes
Initially, the reject rate for slag inclusion defects in flywheel housing castings was as high as 45%. These defects arise from two main sources: firstly, during pouring, the model produces solid and liquid phases that, if not promptly removed, remain inside the casting, forming unique slag inclusion defects. The higher the model density, the more solid and liquid phases are produced. Secondly, molten iron infiltrates the coating on the model during pouring, which, upon solidification, forms slag inclusion defects. Both types of slag inclusion defects appear as black, blocky distributions on both the casting’s external and internal surfaces.
3.2 Control Measures
To address slag inclusion defects, various measures were implemented:
- Low-Density, High-Strength Foam Patterns: To reduce the production of solid and liquid phases, foam patterns with a low density of 24-26g/L were selected. However, excessive reduction in density could compromise the model’s surface quality and increase the risk of coating infiltration. After small-batch testing, it was found that foam patterns with a pre-foamed density of 24-26g/L performed best, reducing the reject rate for slag inclusion defects to less than 5%.
Table 1: Comparison of Foam Pattern Densities and Slag Inclusion Defects
Pre-foamed Density (g/L) | Slag Inclusion Reject Rate (%) |
---|---|
24-26 | <5 |
26-28 | – |
28-30 | – |
- Reasonable Gating System and Pouring Operations: After preliminary calculations, the cross-sectional areas of the gating system components were determined and subsequently improved and optimized through process experimentation. Hollow cylindrical risers were adopted, with molds designed for direct molding using a molding machine. By controlling the pre-foamed density, surface roughness was also controlled. The cylindrical shape minimized the tendency for slag inclusion and reduced temperature loss during pouring.
4. Iron-Encased Sand Defect Analysis and Control
Sand trapping in casting dead zones is a common challenge in both wet sand casting and lost foam casting. In lost foam casting, sand is difficult to fill into dead zones during molding, reducing sand compaction and providing inadequate support for the coating. High-temperature, high-density, and high-flow molten iron can easily breach the coating, causing defects such as iron infiltration.
To address this, the vibration frequency was adjusted using a three-dimensional vibrating table, with a vibration acceleration range of 1-2g. Vibration time and frequency were optimized through experimentation. Compaction time was set to 20s, with a vibration frequency of 45-50Hz and an amplitude of 1-1.5mm. The sanding method involved adding base sand, compacting it, placing the foam pattern, and then filling the sand in two stages. This ensured tight compaction in dead zones, resolving the issue of iron infiltration and controlling iron-encased sand defects.
5. Cold Shut Defect Analysis and Control
Cold shuts are another major defect in thin-walled flywheel housing castings, primarily affecting reject rates. Thin-walled shell castings have slower molten iron flow rates compared to thick castings, resulting in longer flow times and faster temperature drops. Areas where molten iron arrives last may not fully fuse due to excessive heat loss, forming cold shuts.
To address this, the molten iron tapping temperature was increased to 1620°C, with a pouring temperature not below 1500°C. Additionally, pouring operations were optimized for rapid pouring, effectively addressing cold shut defects.
6. Conclusion
Extensive production tests have demonstrated that:
- Support ribs can prevent foam pattern deformation.
- Foam models with a pre-foamed density of 24-26g/L and hollow cylindrical risers effectively address slag inclusion defects.
- Adjusting vibration parameters and manual sand filling solve iron-encased sand defects.
- Increasing tapping and pouring temperatures, along with proper pouring operations, effectively control cold shut defects.
Through these measures, we have significantly improved the quality, process yield, and product qualification rate of flywheel housing castings produced by lost foam casting.