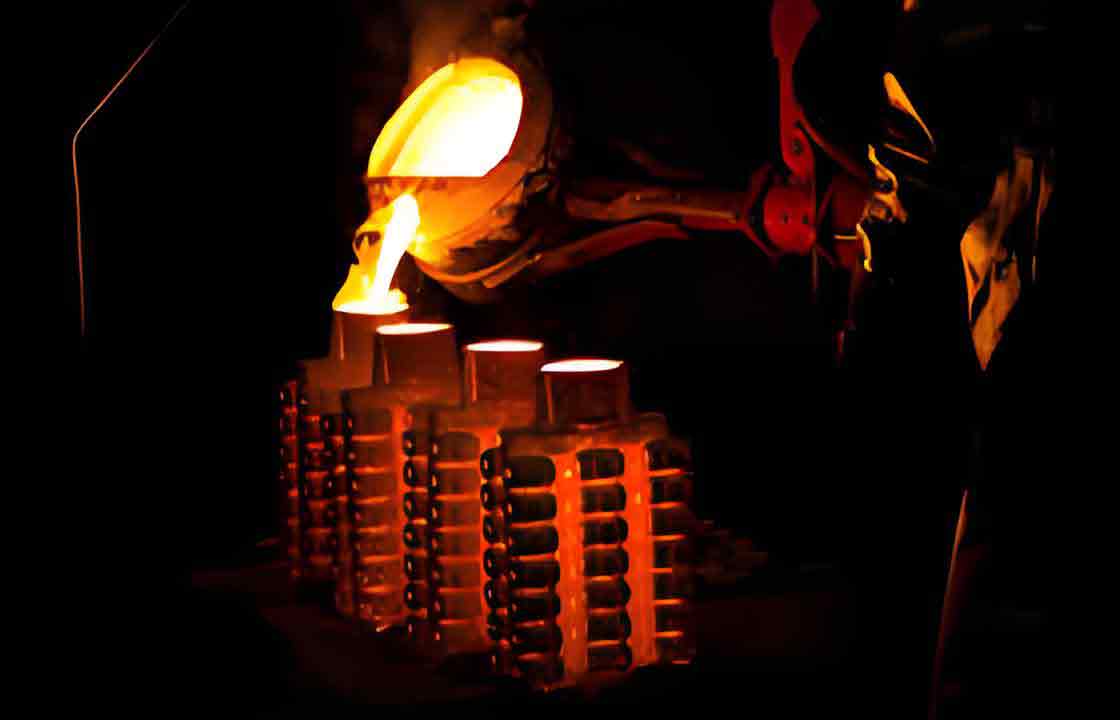
Introduction
Investment casting is a manufacturing process that provides the capability to produce complex and precise components with high dimensional accuracy and superior surface finish. One of the critical factors determining the success of investment casting is the selection of appropriate materials. This article delves into the considerations for material selection in investment casting, exploring the properties, advantages, and applications of various materials used in this process.
Overview of Investment Casting
Process Steps
- Pattern Creation: Wax patterns are created using injection molding or 3D printing.
- Assembly: Wax patterns are assembled onto a central wax gating system.
- Shell Building: The assembly is dipped into a ceramic slurry to build a shell around the wax patterns.
- Wax Removal: The wax is melted and removed, leaving a cavity in the ceramic shell.
- Metal Pouring: Molten metal is poured into the ceramic mold.
- Cooling and Shell Removal: The metal solidifies, and the ceramic shell is broken away to reveal the cast component.
- Finishing: The casting is cleaned, and any additional finishing processes are applied.
Criteria for Material Selection
Mechanical Properties
- Strength: The ability of the material to withstand applied forces without deformation.
- Hardness: Resistance to surface indentation and wear.
- Ductility: The capability of the material to deform under tensile stress.
- Fatigue Resistance: The ability to resist progressive structural damage under cyclic loading.
Thermal Properties
- Melting Point: The temperature at which the material changes from solid to liquid.
- Thermal Expansion: The degree to which the material expands when heated.
- Thermal Conductivity: The ability of the material to conduct heat.
Chemical Properties
- Corrosion Resistance: The ability to withstand degradation due to chemical or electrochemical reactions.
- Oxidation Resistance: The resistance to oxidation at high temperatures.
Economic Factors
- Cost: The price of raw materials and their impact on the overall cost of production.
- Availability: The accessibility of materials in the market.
- Machinability: The ease with which the material can be machined or processed.
Commonly Used Materials in Investment Casting
Stainless Steels
- Properties: High strength, excellent corrosion resistance, good ductility.
- Applications: Turbine blades, medical instruments, automotive parts.
Superalloys
- Properties: Superior mechanical properties at high temperatures, excellent oxidation and corrosion resistance.
- Applications: Jet engine components, gas turbines, high-temperature applications.
Aluminum Alloys
- Properties: Lightweight, good thermal and electrical conductivity, excellent corrosion resistance.
- Applications: Aerospace components, automotive parts, electrical enclosures.
Titanium Alloys
- Properties: High strength-to-weight ratio, excellent corrosion resistance, good fatigue resistance.
- Applications: Aerospace components, medical implants, marine applications.
Copper Alloys
- Properties: Good electrical and thermal conductivity, excellent corrosion resistance, antimicrobial properties.
- Applications: Electrical components, plumbing fittings, marine hardware.
Comparative Analysis of Materials
Material | Strength | Corrosion Resistance | Thermal Conductivity | Cost | Common Applications |
---|---|---|---|---|---|
Stainless Steels | High | Excellent | Moderate | Moderate | Turbine blades, medical instruments |
Superalloys | Very High | Excellent | Low | High | Jet engines, gas turbines |
Aluminum Alloys | Moderate | Good | High | Low | Aerospace, automotive |
Titanium Alloys | High | Excellent | Moderate | Very High | Aerospace, medical implants |
Copper Alloys | Moderate | Excellent | High | Moderate | Electrical components, plumbing |
Advantages and Disadvantages of Common Materials
Stainless Steels
Advantages:
- High strength and toughness
- Excellent corrosion resistance
- Versatile and widely available
Disadvantages:
- Higher density compared to aluminum and titanium
- Moderate thermal conductivity
Superalloys
Advantages:
- Exceptional performance at high temperatures
- High strength and fatigue resistance
- Excellent oxidation and corrosion resistance
Disadvantages:
- High cost
- Difficult to machine and process
Aluminum Alloys
Advantages:
- Lightweight
- Good thermal and electrical conductivity
- Cost-effective and readily available
Disadvantages:
- Lower strength compared to stainless steels and superalloys
- Less suitable for high-temperature applications
Titanium Alloys
Advantages:
- High strength-to-weight ratio
- Excellent corrosion resistance
- Biocompatible for medical applications
Disadvantages:
- Very high cost
- Challenging to machine and process
Copper Alloys
Advantages:
- Excellent thermal and electrical conductivity
- Good corrosion resistance
- Antimicrobial properties
Disadvantages:
- Lower strength compared to steel and titanium alloys
- Higher density compared to aluminum
Future Trends in Material Selection
High-Entropy Alloys (HEAs)
- Properties: Combination of high strength, corrosion resistance, and thermal stability.
- Potential Applications: Aerospace, defense, and high-performance engineering applications.
Composite Materials
- Properties: Tailored properties by combining different materials, such as metals, ceramics, and polymers.
- Potential Applications: Aerospace structures, automotive parts, and medical devices.
Advanced Coatings
- Properties: Enhanced surface properties, such as wear resistance, thermal stability, and corrosion resistance.
- Potential Applications: Engine components, cutting tools, and protective gear.
Sustainable Materials
- Properties: Environmentally friendly, recyclable, and reduced carbon footprint.
- Potential Applications: Automotive parts, consumer electronics, and packaging.
Conclusion
Material selection is a crucial aspect of the investment casting process, significantly impacting the performance, reliability, and cost-effectiveness of the final components. By carefully considering the mechanical, thermal, and chemical properties, as well as economic factors, manufacturers can choose the most suitable materials for their specific applications. Ongoing advancements in material science, such as the development of high-entropy alloys, composite materials, and advanced coatings, are set to further enhance the capabilities of investment casting. As the industry continues to evolve, the strategic selection of materials will remain a key driver of innovation and efficiency in investment casting.