Introduction
Casting virtual simulation technology is one of the essential methods for advanced design in modern enterprises. With the development of virtual simulation technology in casting, there is an urgent need for enterprises to master and understand casting CAE technology talents.
In the traditional casting production and process development, it is mainly based on the accumulation of experience and continuous trial and error until qualified products are produced. This practice of relying on experience and repeated trial and error results in long production cycles, high costs, and difficulty in ensuring casting quality. Casting virtual simulation software is one of the organic components of digital manufacturing, aiming to provide students with a comprehensive understanding of the entire process of casting fluidity, stress, heat transfer, solidification, defect analysis, and optimization. By adopting virtual simulation technology for casting, designers only need to use a computer Directly using 3D modeling software such as SolidWorks to establish a 3D model of the casting, and then using casting virtual simulation software to simulate the casting solidification process, it is possible to predict the possible defect areas in the casting before actual casting, thereby optimizing and improving the existing process to ensure casting quality. Virtual simulation technology for casting has become an important direction of technological development in the casting industry, and has been widely used abroad. As the world’s largest casting country, China is also vigorously promoting the application of this technology. The application of virtual simulation technology has shortened the design cycle of casting processes, accelerated the manufacturing speed of castings, and significantly improved the quality of castings. At the same time, it has put forward higher requirements for the quality of casting technicians, requiring them to have a solid professional foundation and strong innovation consciousness, and to be able to master and develop advanced applied talents for new processes and technologies.
The numerical simulation technology of casting filling and solidification process is the core to analyze the casting process of castings, which can complete the entire process of casting filling flow of various casting alloys under various casting methods, calculate the temperature field, liquid
Based on the results of body pressure, gas pressure, flow velocity, gas content, and flow rate of each runner, simulate the gas generation in the sand core, predict the internal air pressure of the sand core, predict the risk area of porosity defects, and calculate the body shrinkage during solidification and cooling processes. By analyzing the simulation results, it is possible to predict the occurrence tendency of various common casting defects such as shrinkage and porosity. This has achieved good results in improving and optimizing processes, reducing scrap rates, increasing process yield, shortening production cycles, reducing manufacturing costs, reducing the dependence of technical personnel on experience, and maintaining stable process design. After introducing MAGMA software for casting virtual simulation technology in professional practice, the mold design methods and means have become more modern, the design results have been visualized, and the technical level of design work has been improved Secondary and teaching quality; Meanwhile, due to students’ exposure to the application of simulation technology in casting production, some negative impressions of the casting industry have also changed.
Sand casting is a casting method that produces castings in sand molds, and over 80% of products in the casting industry are completed by sand casting. The practical operation links of multiple core courses such as “Industrial System Fundamentals”, “Material Processing Experiment”, and “Material Flow Experiment” have been emphasized in casting practice, and the course content has also received unanimous praise from students. In order to improve the casting quality of the produced products and gain a comprehensive understanding of the entire process of casting filling and solidification, digital simulation technology and experimental research have become effective ways to enhance casting technology Means.
For sand casting, according to the characteristics of the mold, the molding method is selected as manual two box integral molding. The pouring position is determined to be vertically placed, with the small end face facing up and the large end face facing down, and the outer circular surface standing sideways. This pouring position is chosen, and the pouring process and casting quality have the following characteristics: the small end face has a tendency to contain slag and porosity, while the large end face and outer circular surface have better quality. For the convenience of parting, there is only one parting surface for the casting, which is determined at the maximum position of the casting section, with all castings in the lower box. The pattern uses aluminum alloy metal pattern, which has high strength, precise size, smooth surface, wear resistance and durability. The size of the sand box is 300mm × 250mm × 90mm, and the sprue cup is funnel-shaped, with a simple structure and low metal consumption; The sprue used is a conical sprue with a slope of 1 °~2 ° and a large top and small bottom. It is easy to mold, fast to fill during pouring, and the metal liquid flows in a positive pressure state in the sprue, thus preventing suction and impurities from entering the mold cavity.
Lost foam casting is a new casting method that forms castings after foam models with similar dimensions and shapes to castings are painted with fire-resistant coating and dried, buried in dry quartz sand for vibration molding, poured under negative pressure, the models are gasified, liquid metal occupies the position of the models, and solidified and cooled. This casting process is also called “gasified mold casting”, “foam polystyrene plastic molding” and “full mold casting”. A significant difference between lost foam casting coating and sand casting is that the coating is applied to the surface of the lost foam casting, rather than to the surface of the mold cavity. The main function of the coating is to prevent sand adhesion on the surface of the casting, improve the surface strength and stiffness of the lost foam casting, and prevent deformation during molding. During use, the coating is required to adhere well to the surface of the gasification mold, without delamination or peeling after drying. The coating used this time is water-based coating, which has a longer drying time and poor suspension and coating properties, so the sand adhesion on the surface of the casting is more severe.
If the results simulated by virtual simulation technology for casting are correct, it does not necessarily mean that the resulting casting is completely problem free, because the casting process is interrelated and complex. Therefore, virtual simulation only plays a predictive role in the occurrence of defects. However, simulation technology is indispensable in casting, and it still has certain advantages for optimizing large and complex castings.
Conclusion
This article elaborates on the application of simulation technology in sand casting and lost foam casting, analyzes the process, and explains the necessity of using simulation in the casting profession. In the process of China’s transformation from a major casting country to a strong casting country, the application of virtual simulation technology in casting is conducive to unleashing the creativity of casting technology designers, shortening the design cycle of casting processes and tooling molds, reducing casting defects, and ensuring casting quality.
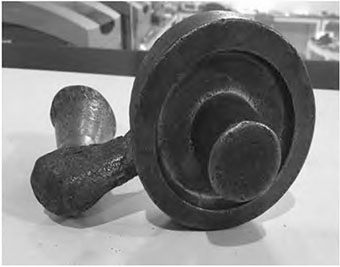
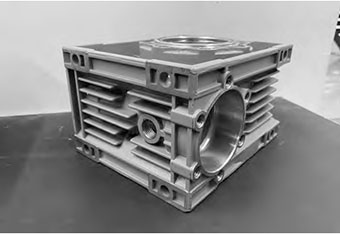