Figure 1 shows the mechanical properties of gray cast iron materials with different carbon equivalents. It can be seen that the mechanical properties of gray cast iron gradually increase with the decrease of carbon equivalent. When the carbon equivalent is 3.8%, the sharp tip of flake graphite will have a splitting effect on the gray cast iron because the graphite is coarse flake, so the mechanical properties of the material will be reduced. When the carbon equivalent decreases from 3.8% to 3.2%, the Brinell hardness of gray cast iron increases from 210hb to 245hb, increasing by 16.7%; The tensile strength increased from 303.99mpa to 385.9mpa, an increase of 27.0%. Moreover, the mechanical properties of 3.2% carbon equivalent grey cast iron are better than ht350 (Brinell hardness 220 ~ 290hb, minimum tensile strength 350Mpa) and reach the mechanical properties of high-strength grey cast iron. The influence of different carbon equivalent on the hardness and tensile strength of gray cast iron can be seen from the comparison formula. In order to further analyze the influence mechanism of carbon equivalent on the mechanical properties of gray cast iron, it is necessary to further analyze the tensile fracture.
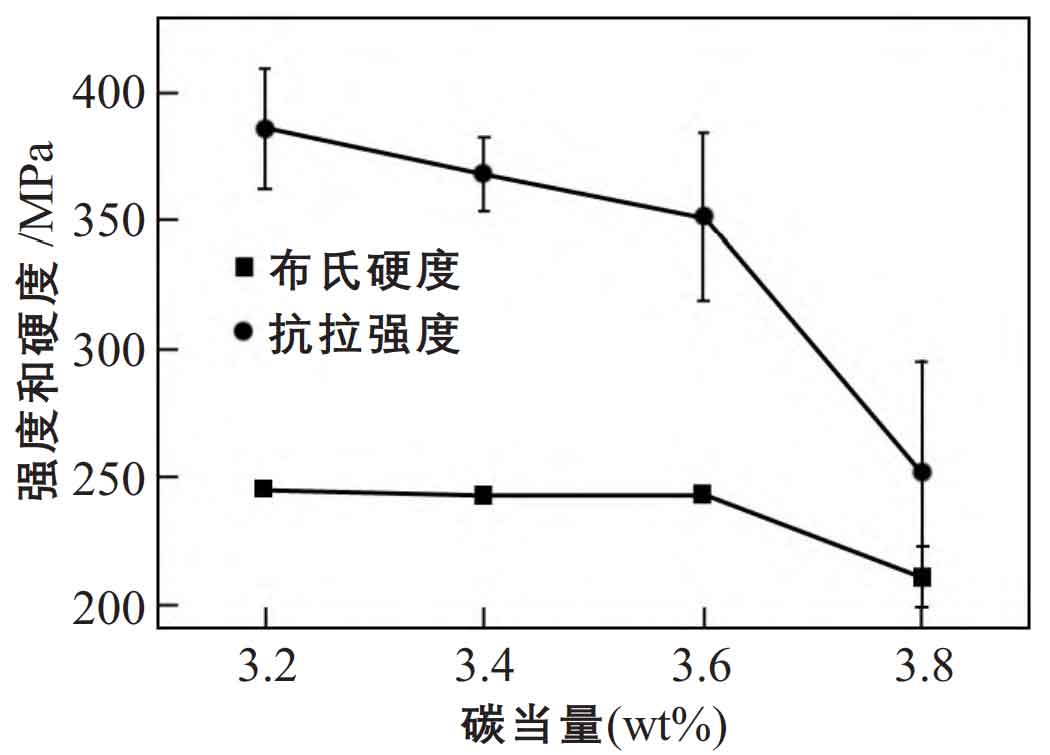
Effect of carbon equivalent on Brinell hardness:

Effect of carbon equivalent on tensile strength:

Where: HBW is Brinell hardness; RM is the tensile strength; X is the carbon equivalent.

The fracture morphology of gray cast iron is mainly affected by the shape, size and distribution of graphite. The fracture form of grey cast iron is brittle fracture, which is cleavage fracture caused by graphite cleavage or interface separation between graphite and matrix. The flower shape is the three-dimensional morphology of flake graphite in a eutectic group. Figure 2 shows the fracture morphology of gray cast iron with different carbon equivalent. The “cavity” in the figure appears after the fracture of graphite, and the fracture also extends outward from the graphite. It can be seen from Fig. 2 (a) to (d) that when the carbon equivalent is 3.2%, the graphite is fine and bent due to the small carbon content. Therefore, there are fewer “holes”. When it breaks, it needs to absorb more energy, which can be obtained from the fact that there are more fluvial cracks; With the gradual increase of carbon equivalent, the graphite morphology gradually becomes flat and coarse, and there are more and larger “cavities”, which leads to the decline of material properties. Therefore, in order to improve the properties of gray cast iron, the graphite morphology should be controlled. The graphite morphology is fine, curved and evenly distributed.