1. Process parameter setting
C | Si | Mn | P | S |
0.45~0.55 | 0.20~0.40 | 1.50~1.80 | ≤0.030 | ≤0.030 |
According to the national standard jb/t 6402-2006, the chemical composition of the selected wheel model material ZG50Mn2 is shown in Table 1, and its mechanical properties are shown in Table 2.
Yield strength /MPa | Elongation /% | Tensile strength /MPa | Reduction of area /% |
445 | 785 | 18 | 37 |

The chemical composition of cast steel in Table 1 is imported into thermal Calc software and calculated with Scheil module to obtain the phase diagram of zg50mn2, as shown in Figure 1. It can be seen that the solidus temperature is 1397 ℃, and the liquidus temperature is 1484 ℃. Generally, the pouring temperature of steel castings is 40~50 ℃ higher than the liquidus temperature. Considering the complex structure of the casting and the easy obstruction of liquid steel flow, the pouring temperature is 1600 ℃. Import the data into JMatPro software to obtain the thermophysical parameters closely related to casting, such as the density and thermal conductivity of zg50mn2, as shown in Figure 2. The model is imported into the visual mesh module of ProCAST and meshed. The number of two-dimensional meshes is 110566 and the number of three-dimensional meshes is 1843950. Set the sand mold temperature to 20 ℃. Resin sand is selected as sand mold material. According to the calculation formula of effective pouring time of steel castings, the required pouring time is 7.8 s. Set the heat exchange coefficient between the wheel and the sand box to 500 w/ (mm2 · K). The cooling mode of mold and environment is set as air cooling.
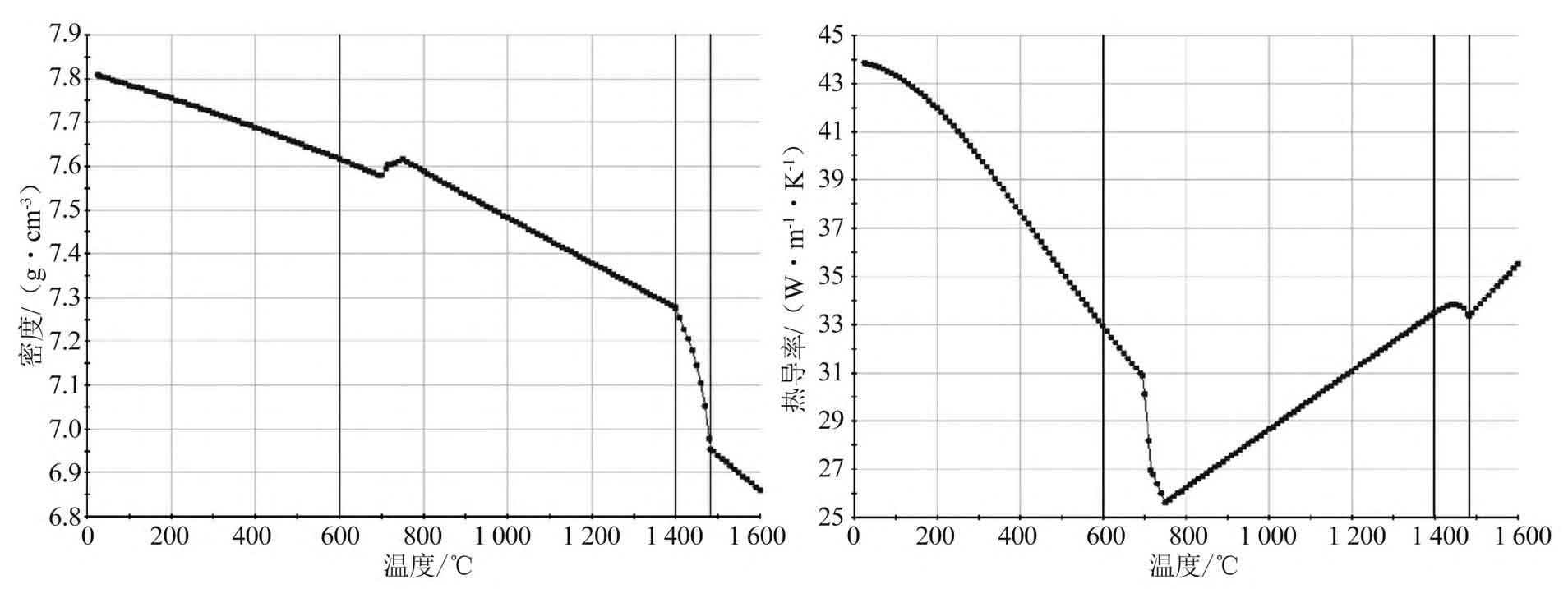
2. Analysis of simulation results
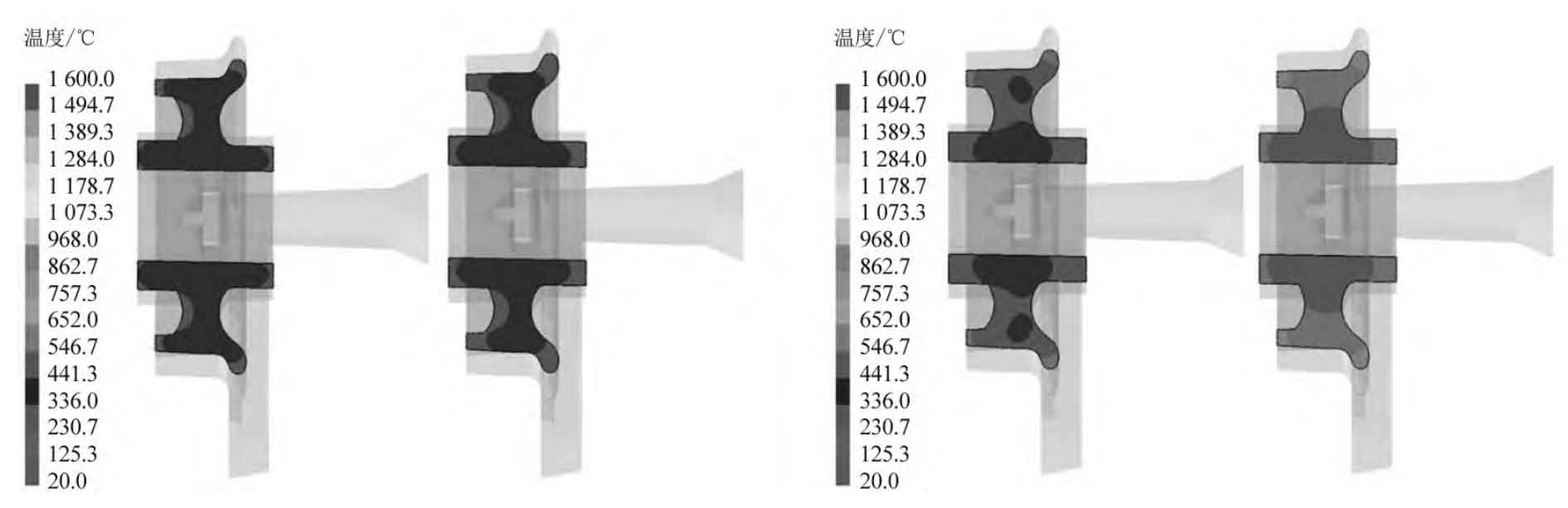
The numerical simulation of the wheel casting was carried out. Because the interior of the wheel was complex and the external observation could not make a judgment, the results were sliced and the temperature field image as shown in Figure 3 was obtained. It can be seen from figure 3A that the temperature around the casting begins to decrease, the internal temperature is in a high state, and there is a large temperature difference with the outside, and the casting is in a liquid shrinkage state as a whole; It can be seen from Figure 3B that the peripheral temperature of the casting continues to decline and gradually expands to the inside, and the temperature difference between the wheel hub and the edge is more obvious; It can be seen from figure 3C that the temperature of the outer ring wall of the casting has reached below the solid phase line and began to solidify, and the interior is still at a high temperature; It can be seen from figure 3D that most of the external positions of the casting have been solidified, the wheel hub has not been fed with liquid metal, the interior of the casting is extremely high, and there is no liquid steel in the central position, resulting in a large number of hot spots in the central part of the casting, resulting in casting defects such as shrinkage porosity and shrinkage cavity.
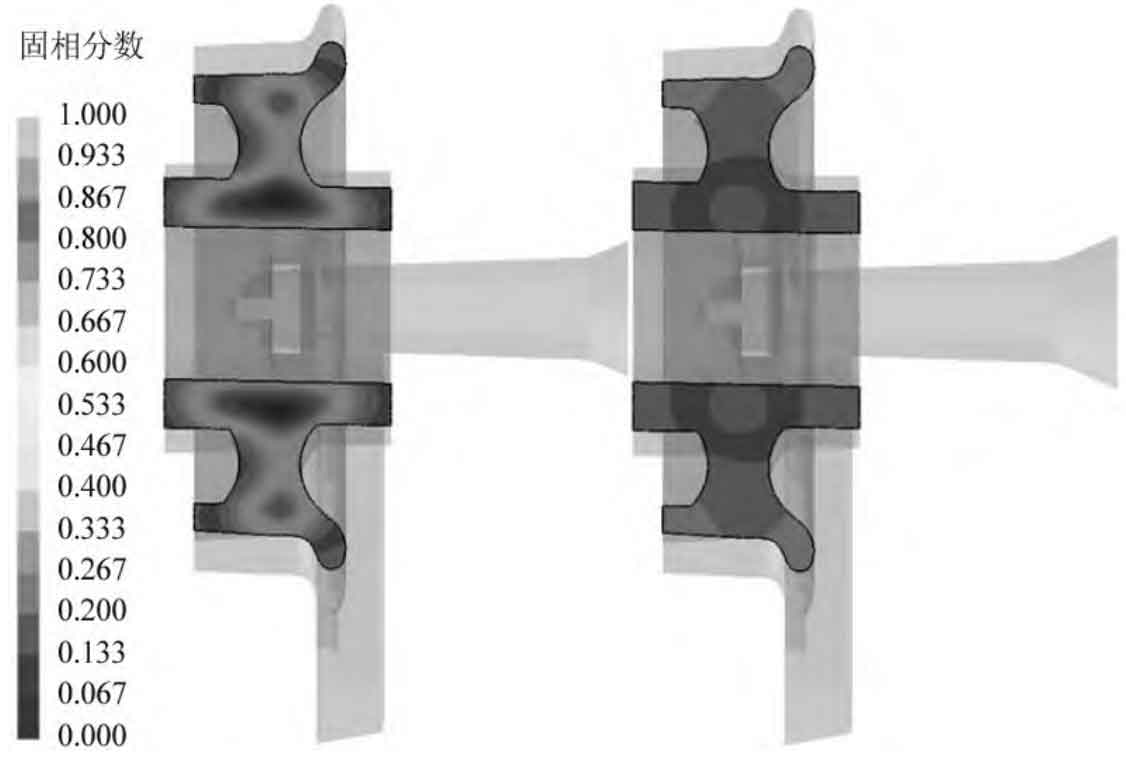
As shown in Figure 4, the isolated liquid phase diagram of the casting when the solidification fraction is 60% and 90% respectively. It can be clearly seen in Figure 4A that the location of the hot spot of the casting; The gray area in Figure 4b is the location where the isolated liquid phase area is generated. Figure 5 shows the location of shrinkage porosity and shrinkage cavity of wheel casting. It can be seen that a large number of shrinkage porosity and shrinkage cavity are generated in the center of the wheel, with a total volume of 146.96 cm3, of which the shrinkage cavity volume is 100.55 cm3, accounting for 40.62% of the total volume. The casting is seriously unqualified, so the overall casting needs to be optimized.
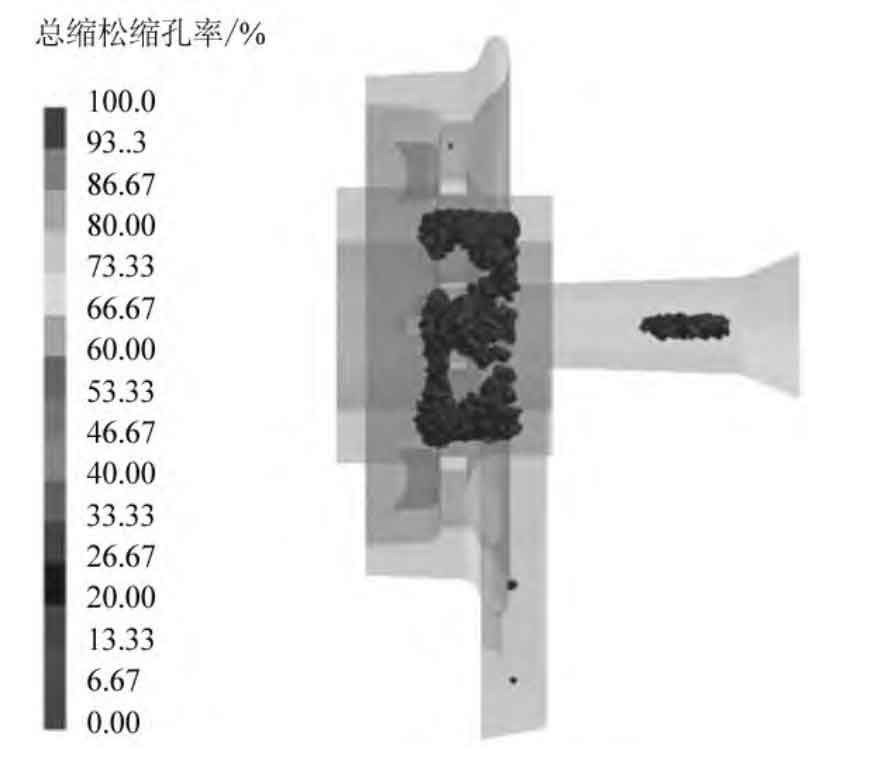