In order to analyze the effect of Cu and Mn content on the mechanical properties of ductile iron casting, tensile tests were carried out on three groups of ductile iron casting samples. The figure is the engineering stress-strain curve of No. 1 ~ 3 ductile iron casting samples, and the table is the mechanical property data obtained from the analysis of tensile curve.
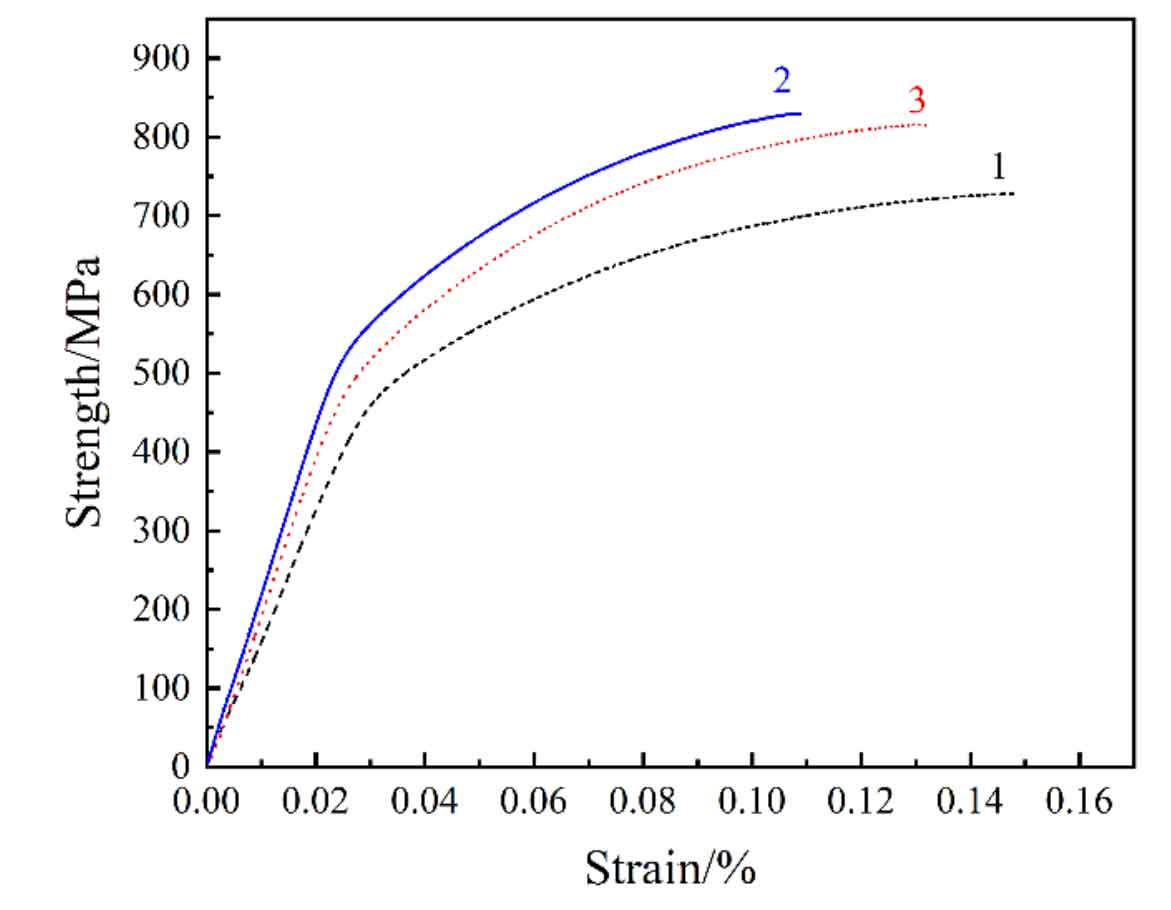
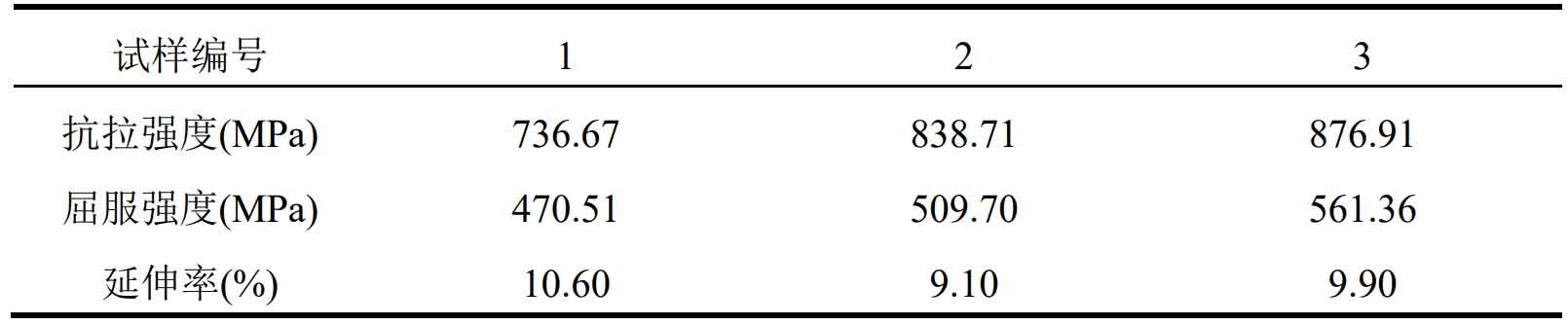
From the tensile curve, it can be seen that as the alloy composition design material of high strength and Toughness ductile iron casting, the comprehensive performance of No. 1 ductile iron casting sample containing 0.28 wt.% Mn and 0.3 wt.% Cu is better, which not only significantly improves the material strength compared with the traditional hub support preparation material QT450-10, but also maintains the plastic toughness of the material. Although No. 2 and No. 3 ductile iron casting samples have higher material strength, the elongation of the material is low, so that the plastic toughness does not meet the requirements of the material.
Combined with the microstructure analysis of three groups of ductile iron casting samples in the previous section, it can be found that:
The tensile strength of No. 1 ductile iron casting sample is 736.67 MPa, the yield strength is 470.51 MPa and the elongation is 10.6%. According to the microstructure analysis results in the previous section, pearlite accounts for about 41.3%, ferrite accounts for about 58.6%, and the pearlite lamellar spacing is 495 nm. With a good matrix structure ratio, the strength of ductile iron casting samples is also higher than that of traditional materials on the premise of maintaining the elongation higher than 10%. In addition, higher spheroidization rate and uniform graphite size are also conducive to reduce stress concentration, and finally make No. 1 ductile iron sample obtain excellent comprehensive properties.
The tensile strength is 838.71 MPa, the yield strength is 509.70 MPa and the elongation is 9.1%. Compared with No. 1 ductile iron casting sample, No. 2 ductile iron casting sample has higher strength but lower elongation. This is because with the increase of Mn content, the ferrite content in the matrix of ductile iron casting sample decreases, and the pearlite content increases to 71.4%. At the same time, the pearlite lamellar spacing is refined to 444 nm, resulting in the increase of material strength and the decrease of elongation.
The Mn content of No. 3 ductile iron casting sample remained unchanged at 0.28 wt.%, the Cu content increased to 0.45 wt.%, the tensile strength was 876.91 MPa, the yield strength was 561.36 MPa, and the elongation was 9.9%. Compared with No. 1 ductile iron casting sample, the pearlite structure of No. 3 ductile iron casting sample increased significantly to 88.8%, about 2.15 times that of No. 1 ductile iron casting sample; The pearlite lamellar spacing is further refined to 306 nm, which further improves the strength of the material. Although the ferrite content in the matrix of No. 3 ductile iron casting sample is the least, its plastic toughness is slightly better than that of No. 2 ductile iron casting sample. This may be because when Mn and Cu act together, the equilibrium distribution coefficient of Mn is 0.64, which belongs to positive segregation, and the equilibrium distribution coefficient of Cu is 1.43, which belongs to negative segregation [75], so the addition of Cu element can weaken Mn segregation, Thus, the effect of Mn segregation on the plastic toughness of the material is reduced to a certain extent.
According to the above analysis and discussion, it is found that by adjusting the content of Cu and Mn in the chemical composition of the material, the effect of changing the proportion of ferrite and pearlite in the matrix structure of the material can be achieved, and finally the high-strength ductile iron casting with comprehensive properties meeting the requirements can be obtained.
The mechanical properties of nodular cast iron can vary significantly depending on its grade. These grades differ in their mechanical strength and elongation capabilities. The microstructure of nodular cast iron, including the density and distribution of graphite nodules, plays a critical role in determining these properties. The graphite nodules act as crack arresters, improving the material’s ductility and toughness. This structural characteristic allows nodular cast iron to possess a combination of strength and ductility that is not typically found in other types of cast iron, making it an excellent material for components that undergo stress, such as hub supports.
Furthermore, the process of manufacturing nodular cast iron involves controlling the shape and distribution of graphite within the iron matrix. Techniques like data mining and machine learning have been applied to better understand and predict the relationship between the material’s microstructure and its mechanical properties. By analyzing experimental data, researchers can identify patterns and correlations that might not be evident through traditional investigative methods. For instance, the variation in solidification rates due to dimensional effects can significantly influence the microstructure and, consequently, the mechanical properties of nodular cast iron. This advanced approach aids in optimizing the material’s characteristics for specific applications, ensuring that components like hub supports meet the required performance standards.