As shown in the figure, the solid fraction and shrinkage porosity distribution of the gating system, where the shrinkage porosity threshold is set to 0.01. From the analysis of the solidification process of the investment casting of the turbine guide, the solidification can basically follow the principle of sequential solidification, which is similar to the solidification temperature field of the investment casting of the turbine guide. It can be seen from Fig. (a) and (b) that the thin-walled blade inside the investment casting of the turbine guide takes the lead in solidification, and then gradually advances to the inner and outer rings of the investment casting of the turbine guide. The solidification time at the intersection of the transverse runner and the inner runner is relatively late.
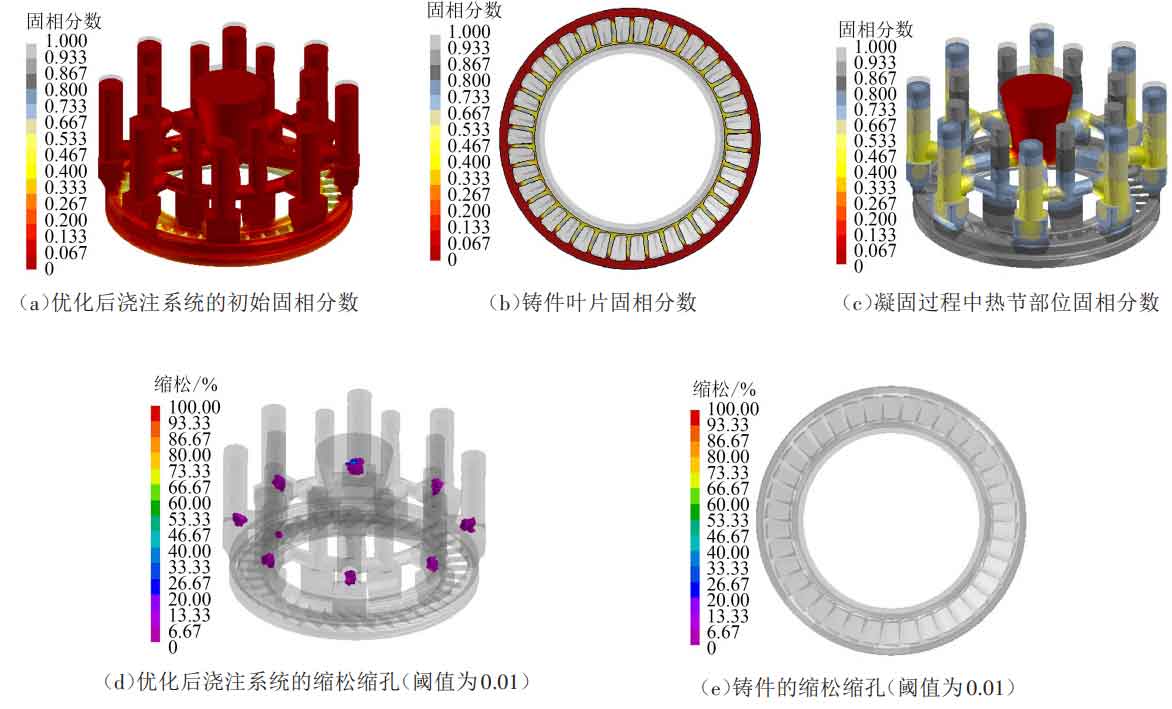
It can be seen from Figure (c) that the wall thickness at the intersection of the transverse runner and the inner runner is prone to produce hot spots, and the solidification time is relatively late, which greatly weakens the feeding capacity of the riser to the middle hot spot position, so it is easy to produce casting defects such as shrinkage porosity and shrinkage cavity, as shown in Figure (d). However, the gating system is sufficient to feed the investment casting of turbine guide, and the casting is solidified according to the principle of sequential solidification, so there is no shrinkage porosity and shrinkage cavity in the investment casting of turbine guide, as shown in Figure (e).
There is no shrinkage hole at the blade of the investment casting of the turbine guide and the inner and outer rings of the casting, but the shrinkage hole mainly occurs at the gating system. From the above simulation results, it can be seen that this casting process can control the melt flow filling process and the production of casting defects.