In the high temperature compression test of Al Si based casting materials, the samples have compression deformation under different temperature and different strain rate environment, and its properties can be used to understand the characteristics of solidification shrinkage deformation of casting. During the solidification process of the shell casting of the hydraulic pump, there are shrinkage cavity and porosity in the last solidified part of the casting due to the liquid shrinkage and solidification shrinkage of the alloy. The existence of any kind of shrinkage cavity and porosity in the casting will reduce the effective area of stress and produce the phenomenon of stress concentration, which will significantly reduce the mechanical properties of the casting.
It can be seen from the figure that the location and size of the shrinkage cavity generated after the preliminary calculation by the software. Combined with the microstructure analysis of the compression sample, due to the low temperature during the further solidification process, the solid particles will gather and move together, which will result in many shrinkage cavities. It is verified that the finite element model can get real and reliable simulation results. Considering that the excessive shrinkage porosity of the shell casting of the hydraulic pump may be due to the problem of the pouring temperature setting, we try to use multiple groups of pouring temperature models to observe the shrinkage porosity phenomenon, which are 640 ℃, 660 ℃ and 680 ℃ respectively.
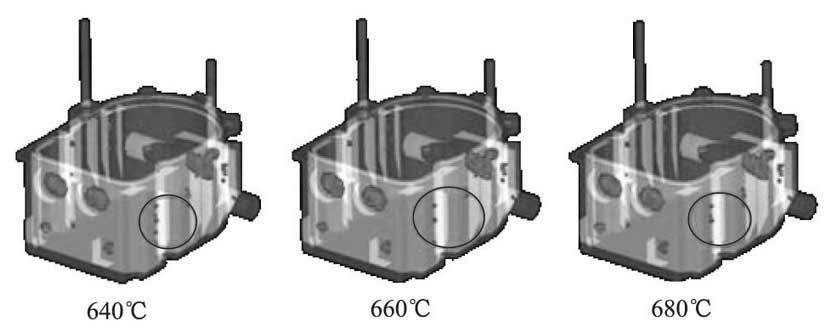
By observing the effect of different pouring temperature on the quality of castings, it is found that there is no significant improvement in shrinkage porosity, only a small part of the area marked in the drawing has some improvement in shrinkage porosity. In the process of casting and solidification of alloy, choosing proper heat treatment process can optimize the quality of casting, and using heat preservation heat treatment can make the surface and internal metallographic structure of casting as consistent as possible.
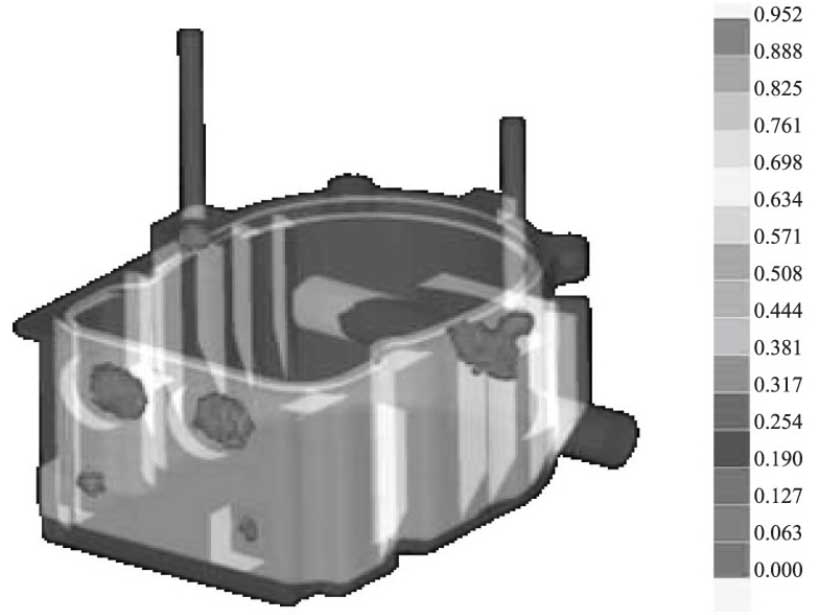
Due to the different ability of solid-phase deformation and aggregation in different temperature range, it is necessary to select appropriate temperature to reduce the adjustment time to ensure the uniform change of structure during the cooling solidification shrinkage process, try not to cause the uneven distribution of large particles in the solid structure of the alloy, and avoid the occurrence of internal cracks. In the process of casting finite element analysis by software, the solution treatment process is calculated by numerical simulation to ensure the mold insulation at 550 ℃ + 6h during solidification, and the shrinkage porosity result is shown in Figure 9. It can be found from the comparison chart that the shrinkage porosity of the workpiece is obviously improved after the heat preservation and treatment process is used.