0 Introduction
Casting coating is one of the indispensable and important raw and auxiliary materials in the casting process, which has a significant impact on the quality of castings. When the molten metal is poured into the cavity and comes into contact with the sand mold and sand core, various physical and chemical interactions will occur between the sand and the molten metal interface, and the results of these actions will lead to some casting defects on the casting Casting coatings are often used in casting practice to prevent these casting defects from occurring. Casting coating refers to a layer of casting auxiliary material with specific functions that is used to adhere to the casting mold and core to isolate molten metal during the casting process. The main functions of coatings are as follows: to reduce the surface roughness value of castings; Prevent or reduce sand sticking defects in castings; Prevent or reduce casting sand holes and sand inclusion defects, etc. Foundry coatings have different classifications from different angles, according to solvents: water-based foundry coatings, alcohol-based and other organic solvent casting coatings; press Uses: casting coatings for cast steel, casting coatings for cast iron, non-ferrous metals Metal casting coatings, flow coating casting coatings, lost foam casting coatings materials, die-casting casting coatings. According to different operation methods, it is divided into dipping Coating, brushing, flowing, etc.
1 Application process of foundry coatings
1.1 Types of paints
According to different product requirements, sand core structure and process requirements, different coatings are selected, and a total of five types of products from four types of manufacturers are used, including water-based and alcohol-based coatings. There are also a variety of methods in use, such as dip coating, flow coating and brush coating, and different standards are formulated for different coating use methods: (1) Flow coating: select coatings with good leveling performance, specify the angle of flow coating and improve the smoothness of the surface of the sand core. (2) Dipping: Adjust the density and angle of dipping according to different product structures. (3) Brushing: Adjust the density of the brushing paint only for the local weak position of some sand cores. There are strict inspection standards for the suspension, density, solid content, gas generation and other properties of different coatings.
1.2 New Coating Validation Process
Casting coatings have a great impact on the quality of castings, and in order to improve product quality, a new type of coating needs to be verified, but it must go through a series of verification processes. Taking the verification of Class A dipping coating as an example, the process parameters used in the sand core dipping process in the core making section are consistent with those of other manufacturers’ coatings, and the coating density process control range is 1.28~1.36 g/cm3, the surface kiln temperature was set to 200 °C, the time was 60min, and other core making and pouring process parameters remained unchanged. Post-analysis of the production process of castings, casting quality and subsequent processing of scraps. For the Class A dip coating verified this time, a total of 36,736 castings and 58 scraps were produced, with a rejection rate of 0.16%, the main waste defects were sand holes and pores (as shown in Figure 1), the rejection rate was within the normal range, the cleanliness of the inner cavity of the casting was good, and the residue of the paint was not abnormal after dissecting the casting (Figure 2). In the process of multiple productions, there are no abnormal problems in the casting, and the new material can only be put into use after verification.
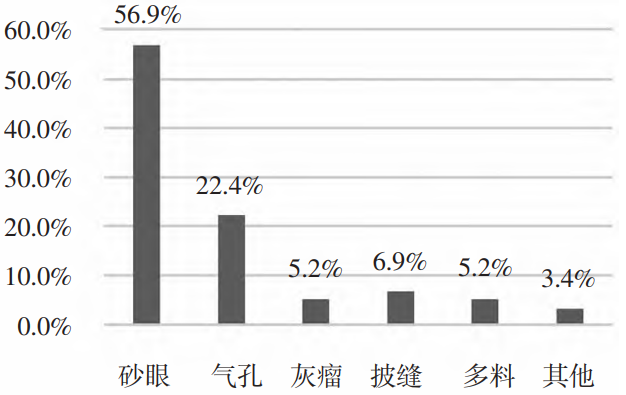
Figure 1 Waste classification chart
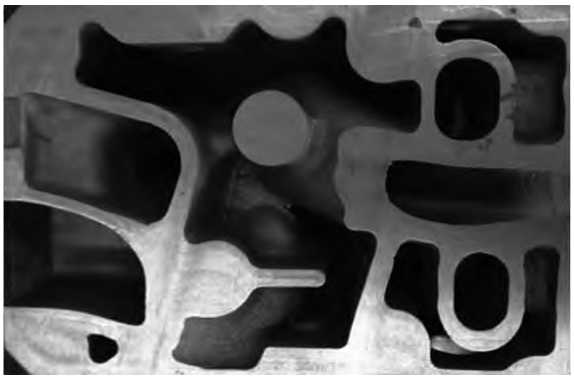
Figure 2 Casting anatomy
2 Problems and control of the use of casting coatings
2.1 Abnormal incoming paint
After the paint is incoming, the viscosity of the paint is large, which makes it difficult to control the density of the site, which affects the use of casting paint and the quality of castings. In December 2020, an anomaly of a dip coating used in the field was analyzed, and the incoming paint was analyzed together with the manufacturer, and Table 1 shows a comparative analysis of three batches of paint that have been used recently. From the above analysis, the following conclusions can be drawn: (1) Paint adhesion
There is no direct correlation between the degree of consistency and the density of the coating. (2) For coatings with too large viscosity, it is not possible to dilute the waste products with water to prevent paint gray tumors, and the consequence of this is that the corresponding density will be reduced.
It affects the performance of the coating such as high temperature resistance and anti-sticking sand. According to the analysis, the main role of the raw material required in the preparation of the paint – the carrier fluid in the coating is to enable the refractory material to be dispersed in it, and the amount of the carrier liquid determines the coating state of the paint is slurry or paste, which may be caused by improper temperature control during the production of coatings.
2.2 A large number of bubbles in the paint pool
There are many bubbles after the paint is stirred in the paint pool, and bubbles appear in the casting matrix (Figure 3). In this case, the following issues are mainly considered: (1) whether the replacement of the paint is beyond the scope of the process, resulting in the problem of deterioration of the coating, and (2) the reaction of the substance of the paint itself. Our response is the addition of defoamers.
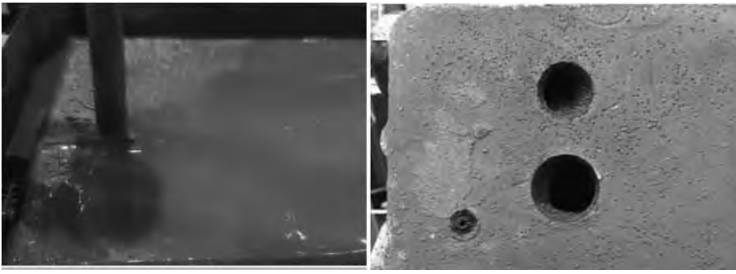
Figure 3 Paint pool and matrix bubbles
2.3 The use strength of the paint is low
The coating is easy to fall off after the sand core is dried, which is defined as insufficient strength and low adhesion, causing the paint to peel off (Figure 4).There are two main functions of binders in coatings: first, the refractory materials and other components in the coating are effectively bonded together to make the coating have certain strength and wear resistance; second, the coating is bonded with the substrate to protect the substrate. After the sand core is dried, the paint will fall easily, mainly because of the abnormal performance of the binder in the coating.
Table 1 analyzes the comparative results
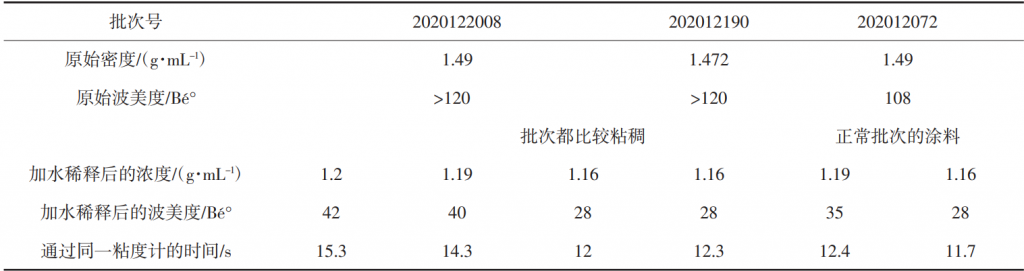
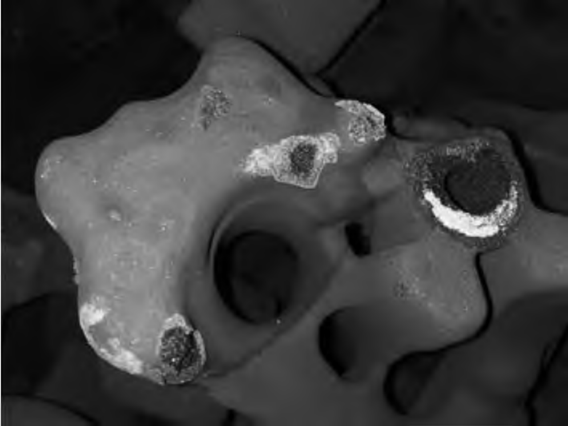
Figure 4 Paint falls
2.4 Paint accumulation
In the process of on-site use, the intake and exhaust ducts are improperly adjusted due to dipping and control coating, resulting in paint accumulation (airway gray tumor) and poor coating (as shown in Figure 5). Comparing the corresponding positions of the cylinder head airway gray tumor and the sand core airway, there is no parting surface and crack, and the analysis is the inlet airway control coating method and coating Improper density adjustment leads to paint accumulation, which eventually leads to a shortage of material in the airway of the sand core multi-material cylinder head. According to the test, the dipping method of the coating was adjusted, and the control coating angle was adjusted from 30° to 45°, and the effect was good (Figure 6). Docking with paint manufacturers, strictly control the paint production process, and ensure the fluidity of coatings.

Figure 5 Poor coating
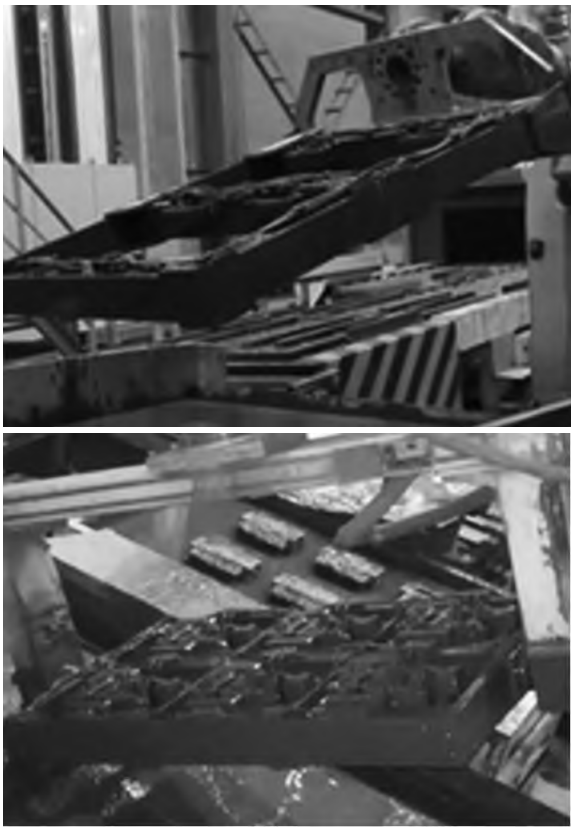
Figure 6 Dip angle
3 The use of local special coatings
If there is a water leakage defect in the casting, which is anatomically analyzed as local shrinkage porosity, and according to the software analysis, there is indeed a problem of slow cooling of the defective part (as shown in Figure 7), we will test a chilling coating according to the structure of the sand core of the casting.
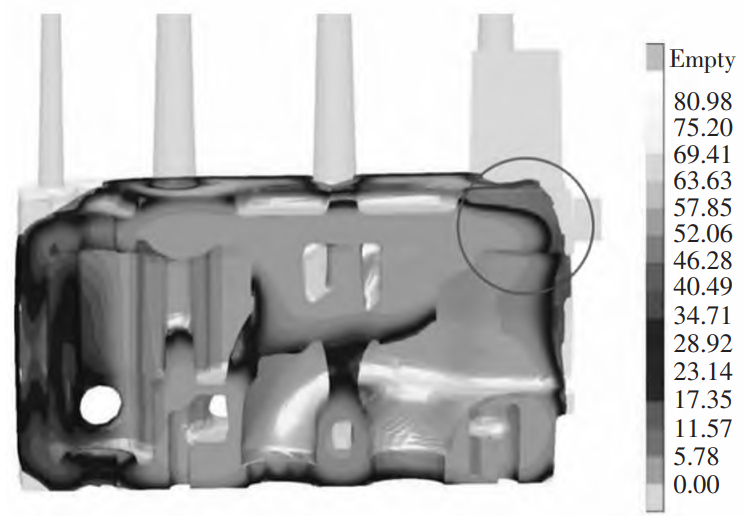
Figure 7 Filling simulation of the gating system
The quenching coating contains a strong carbonization element, which can increase the subcooling degree of the molten metal and make the casting cool quickly. On the one hand, the use of paint can make the molten iron in this part supercool and solidify quickly, avoid the gas in the sand core and molten iron from finally gathering here to form pores, and on the other hand, make the wall thickness and structure dense to prevent pressure leakage. After the test, the position of the brush paint was knocked out, and the chilling structure could be observed macroscopically, with a thickness of about 1.5 mm, and the structure of the brush coating position was different from that of normal gray cast iron by metallographic structure analysis, and the boundary of the white layer was obvious, and obvious supercooled D, E type graphite layers appeared, that is, the quenching effect was good.
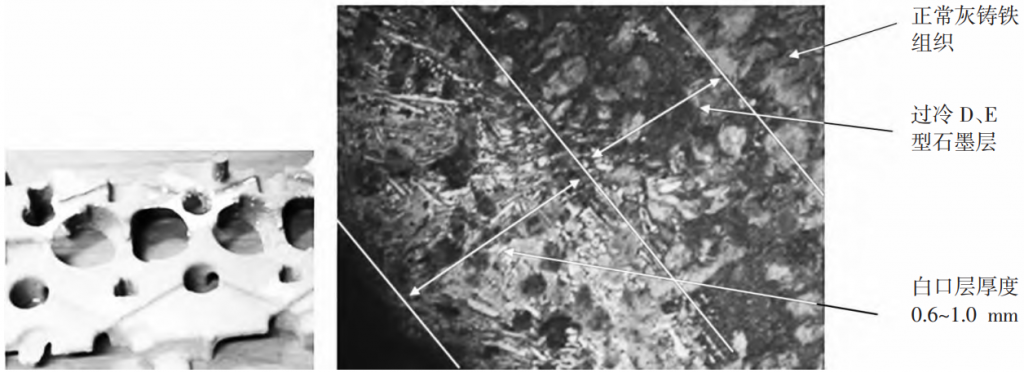
Fig. 8 Crystalline phase analysis of the coating position and microstructure
4 Conclusion
The influence of the coating on the casting is very important and the situation is complex, through the study of the current situation of the use of the coating and the problems in the use process, the reasons for the abnormal use of the coating are analyzed, and the direction is provided for the control of the subsequent coating incoming materials, the treatment of abnormal conditions and the verification of new coatings.