1. Introduction
In recent years, with the increasing concern of consumers about the “energy conservation and environmental protection” and “driving range” performance of new energy vehicles, lightweight has been widely applied in the field of new energy vehicles. Although there has been relatively more research on the lightweight of vehicle bodies at home and abroad, research on chassis lightweight is relatively scarce. With the rapid rise of domestic new energy vehicles, in the short term, the specific capacity of liquid lithium batteries is approaching the limit. Therefore, increasing research on chassis lightweight is of great practical significance. This article focuses on the application and development of cast aluminum alloys in the lightweight of automobile chassis structural parts.
2. Research Objects of New Energy Vehicle Chassis Lightweight
Automobile chassis often use a large number of high-strength steel, cast iron, and cast steel parts. Under the premise of ensuring the safety and reliability of the chassis, how to meet the lightweight requirements of chassis parts through light alloy casting technology has become the key research direction for casting workers and scientific researchers. The main lightweight parts of the new energy vehicle chassis include sub-frames, control arms, steering knuckles, floor plates, battery boxes, wheel arch shock towers, etc. These parts can be formed by processes such as vacuum die casting, low-pressure casting, differential pressure casting, squeeze casting, and gravity casting. The following is a detailed introduction to the casting technologies used for the lightweight of typical chassis parts of new energy vehicles.
2.1 Sub-frame
The sub-frame is divided into front and rear sub-frames, with hollow and solid structures. Generally, the structure is designed according to the vehicle load and NVH requirements, and is mostly formed by low-pressure casting and vacuum die casting processes. In China, low-pressure casting is mainly used, and common aluminum alloy materials include AlSi10MnMg, A356.2, JDA1b, JDA2b, C611, C611M, AlSi9MnMoZr, etc. The chemical composition and mechanical properties are shown in Tables 1 and 2.
Brand | Si | Fe | Cu | Mn | Mg | Sr | Ti | Cr | Zn | RE |
---|---|---|---|---|---|---|---|---|---|---|
AlSi10MnMg | 9.5 – 11.5 | ≤0.15 | ≤0.03 | 0.5 – 0.8 | 0.45 – 0.55 | 0.014 – 0.026 | 0.04 – 0.09 | ≤0.03 | ≤0.05 | – |
A356.2 | 6.5 – 7.5 | ≤0.12 | ≤0.05 | ≤0.02 | 0.25 – 0.45 | – | 0.1 – 0.15 | – | ≤0.05 | – |
JDA1b | 8.0 – 10.5 | <0.15 | 0.1 – 1.5 | 0.5 – 0.8 | 0.1 – 0.5 | 0.02 – 0.03 | 0.1 – 0.2 | – | – | ≤0.25 |
JDA2b | 2.0 – 3.6 | – | – | 0.5 – 0.8 | 6.0 – 8.0 | – | 0.15 – 0.2 | – | – | 0.1 – 0.2 |
C611 | 6.0 – 7.0 | ≤0.12 | ≤0.04 | ≤0.6 | 0.16 – 0.25 | – | ≤0.08 | – | – | – |
C611M | 6.665 | 0.094 | 0.002 | 0.524 | 0.296 | 0.02 | – | – | 0.005 | – |
AlSi9MnMoZr | 9.5 – 10.5 | 0.15 | 0.02 – 0.05 | 0.35 – 0.6 | ≤0.08 | 0.012 – 0.02 | 0.04 – 0.15 | ≤0.05 | ≤0.05 | – |
Brand | Heat Treatment | Tensile Strength (MPa) | Yield Strength (MPa) | Elongation (%) |
---|---|---|---|---|
AlSi10MnMg | T6 | 220 – 240 | 160 – 180 | 6 – 8 |
A356.2 | T6 | ≥280 | ≥220 | ≥6 |
JDA1b | F | 260 – 300 | ≥120 | 12 – 15 |
JDA2b | F | 360 – 420 | 180 – 220 | 10 – 12 |
C611 | F | ≥240 | ≥123 | ≥16.2 |
C611M | F | ≥240 | ≥128 | ≥14 |
AlSi9MnMoZr | F | ≥250 | ≥150 | ≥8 |
Zhang Yunfeng et al. developed the process of a large-size hollow sub-frame by low-pressure casting. The size of the sub-frame is 1128.5mm×606.9mm×271.8mm, the material is A356.0, the mass is about 16.25kg, and the minimum wall thickness is 4.5mm. The inner cavity structure is formed by 3D printed sand cores. After T6 heat treatment, the tensile strength of the body reaches 310 – 328MPa, the yield strength is 230 – 240MPa, and the elongation is 7% – 10%, meeting the product performance requirements. The gating system design is shown in Figure 1.
Shi Jian et al. used the AlSi7Mg0.3 material for low-pressure casting of the Chery rear sub-frame. The aluminum alloy liquid was modified and grain refined, and after heat treatment, the tensile strength of the body was ≥280MPa, the yield strength was ≥220MPa, and the elongation was ≥7%. The outline size of the hollow thin-walled casting is 1135mm×240mm×240mm, the mass is about 7.8kg, the main wall thickness is 4.5mm, there are a large number of reinforcing ribs in the inner cavity, and the local wall thickness is 48mm with uneven wall thickness and a draft angle of 3 – 5°. The gating system design is shown in Figure 2.
In addition to low-pressure casting, Sun Jue et al. used an SCV – 2500 vertical squeeze casting machine to produce the Hongqi sub-frame. The outer dimension of the sub-frame is 940mm×560mm×230mm, the structure is symmetrical on both sides, the structure at both ends is complex, and the structure in the middle section is relatively simple. There are many semi-enclosed inner cavity structures on the front of the casting. The average wall thickness of the casting is about 10mm, and the minimum wall thickness is 6mm. The wall thickness of the mounting holes on both sides is 40mm. The volume of the casting is about 5.6×10⁻³m³, and the mass is about 15kg. The squeeze casting pouring temperature is 700°C, the mold temperature is 250°C, the main injection pressure of the punch is 97MPa, the holding time is 20s, the moving speed of the punch during the filling process is 0.1m/min, and the moving speed of the punch at the end of the filling is 0.2m/min. The pressure of local pressurization is 250MPa, and it is started 3 – 5s after the end of injection. After T6 heat treatment strengthening, the tensile strength of the casting body reaches 280MPa, the yield strength reaches 225MPa, the elongation reaches 8.1%, and the hardness is HBW95. The gating system is shown in Figure 3, and the cross-sectional areas of the gating system are shown in Table 3.
Inner Runner | 1 | 2 | 3 | 4 | 5 |
---|---|---|---|---|---|
Area (mm²) | 412 | 335 | 202 | 202 | 215 |
Inner Runner | 6 | 7 | 8 | 9 | 10 |
Area (mm²) | 201 | 377 | 364 | 270 | 310 |
In addition to the low-pressure casting and squeeze casting processes, the Wuhan factory of Guangdong Hongtu used an IDRA 16000kN die casting machine (punch diameter of 130mm) for vacuum die casting of the rear sub-frame of the Xiaopeng G6. The mass of the part is 2.67kg, the average wall thickness is 3.6mm, the outline size is 678.83mm×114.53mm×233.86mm, and the projected area of the casting is 86421mm². The casting material is AlSi8MnMg, requiring a tensile strength of ≥220MPa, a yield strength of ≥150MPa, and an elongation of ≥5%. The diameter of pores in general positions is ≤1mm, and the diameter of pores in thick-wall positions is ≤2mm. The gas content per 100g of casting at the inlet position is ≤10mL, and the gas content per 100g of casting at the filling end position is ≤15mL. The pull-out force of the M12 thread of the casting is ≥85kN, and the pull-out force of the M10 thread is ≥60kN. When the force on the casting is not less than 6.1kN, the fatigue test can meet 20000 cycles without damage, and there is no damage at 40000 cycles. The impact toughness is greater than 6J/cm², and the hardness HRB is ≥30. The gating system is shown in Figure 4.
Honda Motor exhibited an aluminum alloy front sub-frame at the “2016 People and Vehicle Technology Exhibition” at the Pacifico Yokohama International Convention Center and has put it into use in the mass-produced fuel cell vehicle (FCV) “CLARITY FUEL CELL”. By integrally forming a complex hollow closed cross-section structure, the lightest aluminum alloy sub-frame in the world has been achieved, with a mass 20% lighter than the original and an average wall thickness of about 3mm. The sub-frame is formed by the die casting process, and the key is to use a coated sand core to obtain a hollow closed cross-section. Honda said that it will be applied to larger and more complex aluminum alloy sub-frames in the future. However, the current cost is higher than that of the solid aluminum sub-frame.
At present, hollow sub-frames generally adopt the low-pressure casting or gravity casting process with sand cores, among which low-pressure casting is the mainstream. For example, the rear sub-frames of BYD Yangwang U8, U9, as well as the DENZA series, Hongqi, NIO, SAIC Zhiji (as shown in Figure 5), Dongfeng Voyah, and Tesla Model X.
Hubei AVIC Special Vehicle has achieved economies of scale in low-pressure casting aluminum alloy sub-frames. Tesla is researching the production of hollow sub-frames by high-pressure die casting, but it cannot meet the requirements of the hollow structure, mainly involving the strength and collapsibility of the sand core. Foreign countries are trying salt-bonded sand cores, which can be removed by soaking in water after high-pressure die casting. The advantage of high pressure is obvious, but the salt core technology for hollow structures still needs further research and breakthroughs. Japan is at the forefront of this research.
2.2 Control Arm
Aluminum alloy control arms are mainly formed by forging and casting processes. Forged parts have high mechanical properties, but complex structures are difficult to form, and the cost is higher than that of casting. Control arms are mainly produced by gravity, low-pressure, differential pressure, squeeze, and semi-solid casting processes. Xu Shiwen et al. comprehensively considered factors such as investment cost, product performance, and production efficiency and adopted the squeeze casting process, which has performance close to forging and good process stability. The tensile strength of the body is 293.2MPa, the yield strength is 226.48MPa, and the elongation is 9.01%. When there is no local extrusion, obvious shrinkage porosity occurs at the thick mounting holes of the casting, which can be eliminated by local extrusion. In actual production, special attention should be paid to the fact that the penetration depth of the local extrusion pin not only depends on the pressure of the local extrusion cylinder but also on the penetration time and the solidification condition of the casting. The solidification simulation analysis of the gating system and the trial-produced casting are shown in Figures 6 and 7.
For the control arm with a hollow structure, the sand core + low-pressure casting process is adopted, and the mechanical properties are improved by T5 heat treatment. For example, the control arms of FAW Hongqi H9 and Deepal SL03/S7, and the product structure is shown in Figure 8.
2.3 Steering Knuckle
Aluminum alloy hollow steering knuckles are generally formed by low-pressure casting, and solid structures are formed by low-pressure, squeeze, or gravity casting. At present, the mainstream medium and high-end vehicle aluminum alloy hollow steering knuckles are formed by low-pressure casting, such as the Porsche hollow steering knuckle (as shown in Figure 9). Relevant enterprises and universities have carried out research on the production of solid steering knuckles by squeeze casting, but large-scale vehicle application has not been reported. At present, the steering knuckles of economical models are mainly sand-cast ductile iron parts.
2.4 Wheel Arch Shock Tower
It is mainly formed by vacuum high-pressure casting, such as Tesla, Xiaopeng, NIO, and Chery. For example, the contour size of the shock tower casting of the Xiaopeng G6 is 532mm×365mm×299mm, the average wall thickness is 3mm, and the mass is 3.6kg. Compared with the steel plate structure, the product weight is reduced by about 35%. The IDR 3500T die casting machine is used, and the left and right shock towers are designed in a one-mold-two-piece layout. The overall gating system effect is shown in Figure 10(a). The main die casting process parameters are as follows: the length of the pressure chamber is 1250mm, the filling degree is 29.64%, the vacuum degree in the die cavity during die casting is below 90kPa, reaching a high vacuum state, the die casting temperature is 680 – 700°C, and the mold temperature is controlled above 200°C. After T6 treatment (holding at 490°C for 3h, solution treatment + holding at 170°C for 3h, aging treatment), the tensile strength is ≥300MPa, the yield strength is ≥250MPa, and the elongation is ≥8%. The vacuum die casting trial-produced part of the wheel arch shock tower is shown in Figure 10(b).
2.5 Front and Rear Floor Plates
Due to the extremely large contour size of the parts, an ultra-large vacuum die casting machine with a clamping force of more than 7000T is required, and a heat-treatment-free aluminum alloy material is used. Tesla leads the development direction of the industry. The early qualification rate of Tesla was 30%, and after two years of process and gating system debugging, it is currently only 90% – 95%, which shows the great difficulty. Domestic companies such as Guangdong Wencan and Guangdong Hongtu are at the forefront. The domestic Zeekr 009 uses a 7200T die casting machine to produce the world’s largest integrated die-cast rear aluminum floor plate (as shown in Figure 11). The rear aluminum floor plate of the Zeekr 009 is 1.4m long and 1.6m wide, and its volume is larger than that of the Tesla Model Y rear body. This product eliminates nearly 800 welding points for the the Zeekr 009, reduces the number of parts by more than 80, and reduces the weight by 16%. According to the data released by Zeekr, the deformation of the rear part of the integrated die-cast body is reduced by 16%, the bending stiffness is increased by 11%, and the torsional stiffness is increased by 9.5% to reach 36450N·m/deg.
3. Conclusion
Aluminum alloy casting technology will play a significant role in the lightweight of new energy vehicle chassis, especially in the vacuum die casting and low-pressure casting of oversized parts. The high-pressure casting of hollow structures has not been maturely applied due to the need to overcome the balance between the strength and collapsibility of sand core materials. The use of 3D printed sand cores has poor collapsibility and is not suitable for mass production. Therefore, it is necessary to develop core materials that balance strength and collapsibility. The chassis hollow structural parts are mainly formed by low-pressure casting, combined with T5, T6, or T7 heat treatment, which can meet the mechanical property requirements of the body. The A356 squeeze casting parts have the potential to replace some sand-cast ductile iron parts and forged aluminum parts due to their small machining allowance. The vacuum squeeze casting technology for oversized parts is a future research direction. Currently, the main factors affecting the substitution of cast aluminum parts for ductile iron and steel are technical reserves, vehicle cost performance, and economies of scale.
In the future, with the continuous development of technology and the increasing demand for lightweight in the automotive industry, the application and innovation of cast aluminum alloys in the lightweight of automobile chassis structural parts will continue to progress. It is expected that more advanced casting processes and materials will emerge, further promoting the development of the automotive lightweight industry.
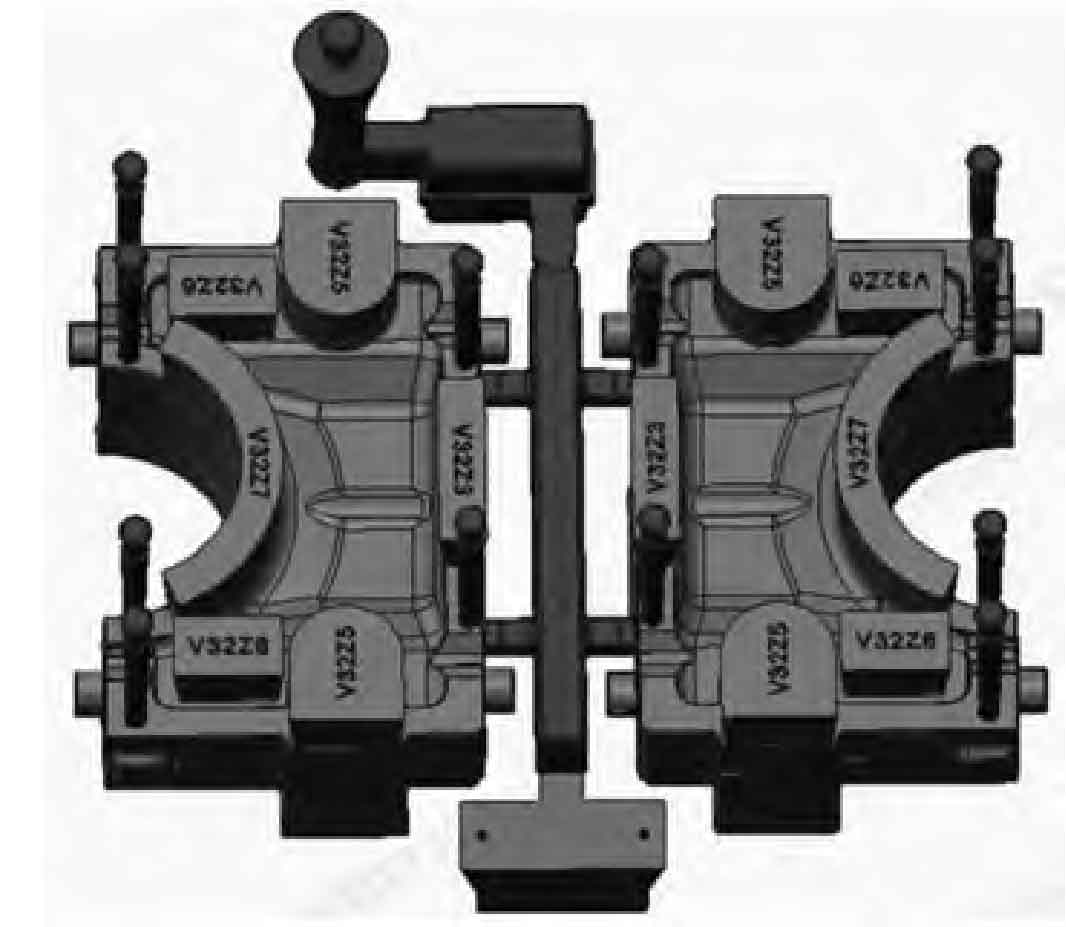