Steel casting is a critical process in numerous industries, including automotive, construction, and heavy machinery. However, defects in steel casting can have significant economic impacts, leading to wasted resources, increased costs, and reduced efficiency. This article explores the economic ramifications of steel casting defects and presents strategies to minimize waste and maximize efficiency, with detailed tables and lists for enhanced understanding.
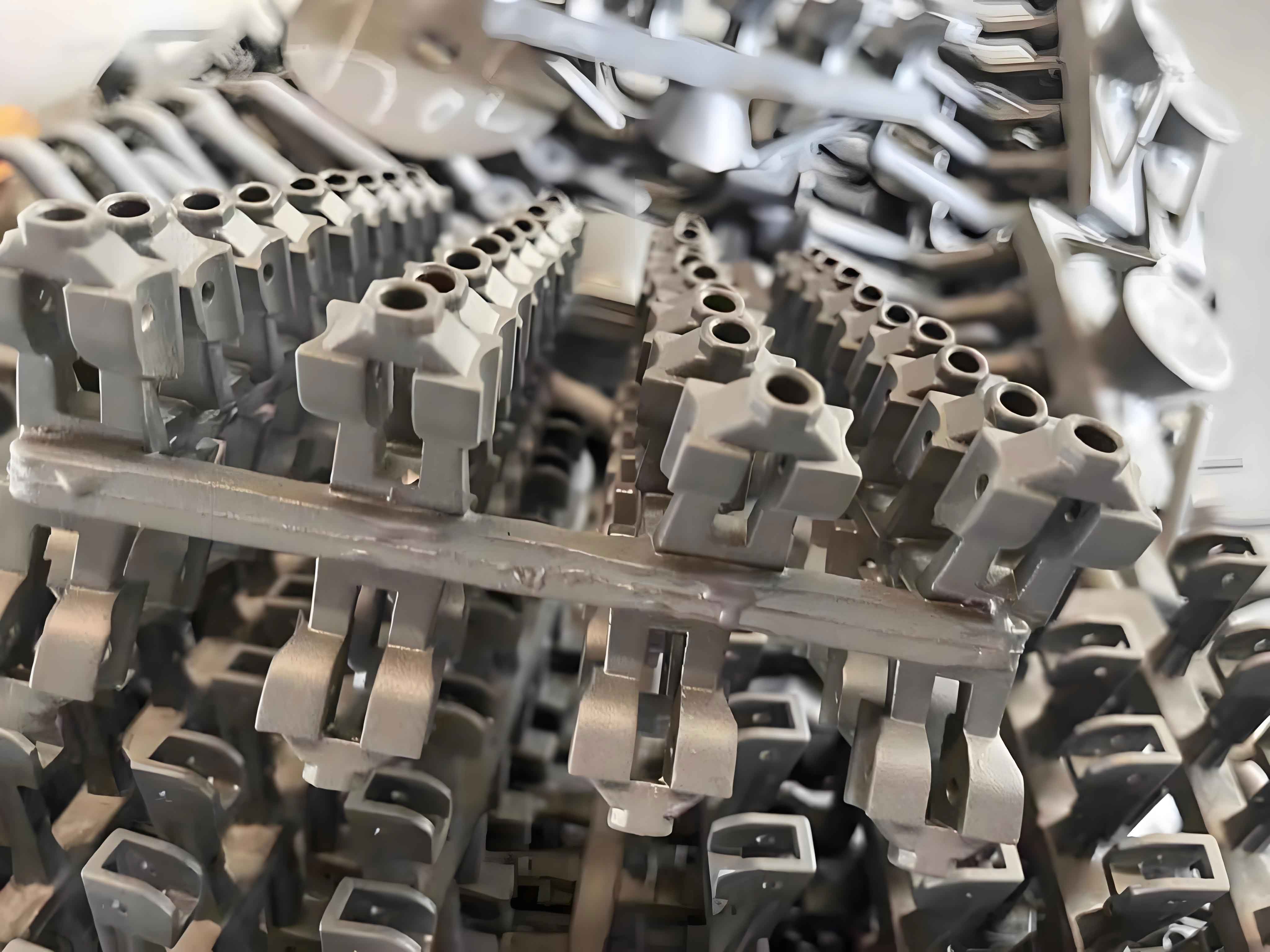
Introduction
Steel casting defects can arise from various sources, including material impurities, process variations, and inadequate quality control. These defects can result in rejected parts, rework, and even equipment failures, leading to substantial economic losses. Understanding the types and causes of defects, along with implementing effective strategies to mitigate them, is crucial for enhancing the economic efficiency of steel casting operations.
Economic Impact of Steel Casting Defects
- Direct Costs:
- Material Waste: Defective steel casting often need to be scrapped, leading to wasted raw materials.
- Rework Costs: Repairing defective parts incurs additional labor and material costs.
- Inspection Costs: Increased inspection and testing to identify defects raise operational expenses.
- Indirect Costs:
- Production Delays: Defects can cause delays in production schedules, impacting delivery timelines.
- Customer Dissatisfaction: Poor quality products can lead to customer complaints, returns, and loss of business.
- Reputation Damage: Consistent defects can tarnish a company’s reputation, affecting future sales and partnerships.
- Opportunity Costs:
- Lost Sales: Time and resources spent on defective products could have been used to produce and sell quality parts.
- Innovation Stagnation: Focus on defect management can divert resources from research and development efforts.
Table: Economic Impact of Steel Casting Defects
Impact Category | Description | Examples |
---|---|---|
Direct Costs | Immediate financial losses due to defects | Material waste, rework costs, inspection costs |
Indirect Costs | Secondary financial impacts affecting operations | Production delays, customer dissatisfaction |
Opportunity Costs | Potential revenue loss and missed opportunities | Lost sales, innovation stagnation |
Common Steel Casting Defects and Their Causes
- Porosity:
- Caused by trapped gases or shrinkage during solidification.
- Inclusions:
- Non-metallic particles trapped within the steel casting, originating from slag or other impurities.
- Cracks:
- Result from excessive thermal stresses or rapid cooling rates.
- Misruns:
- Incomplete filling of the mold, often due to insufficient pouring temperature or poor mold design.
- Hot Tears:
- Occur when the steel casting cools unevenly, leading to internal stresses and fractures.
List: Strategies for Minimizing Steel Casting Defects
- Improved Material Selection:
- Use high-quality raw materials to reduce impurities that cause defects.
- Optimized Pouring Techniques:
- Maintain proper pouring temperatures and techniques to prevent defects like misruns and porosity.
- Enhanced Mold Design:
- Design molds to ensure smooth metal flow and adequate cooling rates.
- Advanced Quality Control:
- Implement rigorous inspection and testing protocols to detect and address defects early.
- Process Control and Monitoring:
- Utilize real-time monitoring and control systems to maintain consistent steel casting conditions.
- Employee Training:
- Train workers on best practices and defect prevention techniques.
Table: Strategies for Minimizing Steel Casting Defects
Strategy | Description | Expected Benefits |
---|---|---|
Improved Material Selection | Use high-quality raw materials | Reduced impurities and inclusions |
Optimized Pouring Techniques | Maintain proper pouring temperatures and techniques | Prevention of misruns and porosity |
Enhanced Mold Design | Design molds for smooth metal flow and adequate cooling | Minimized hot tears and misruns |
Advanced Quality Control | Rigorous inspection and testing protocols | Early defect detection and correction |
Process Control and Monitoring | Real-time monitoring and control of casting conditions | Consistent casting quality |
Employee Training | Training workers on best practices and defect prevention | Reduced human error and improved skills |
Future Prospects for Minimizing Defects and Enhancing Efficiency
- Integration of Smart Manufacturing:
- Implementing Industry 4.0 technologies such as IoT, AI, and machine learning to predict and prevent defects.
- Advanced Simulation Techniques:
- Utilizing computer-aided engineering (CAE) tools to simulate and optimize steel casting processes before actual production.
- Material Innovations:
- Developing new alloys and composite materials with enhanced properties to reduce defect occurrence.
- Sustainability Initiatives:
- Focusing on sustainable practices, such as recycling scrap metal and using eco-friendly materials, to minimize waste and reduce costs.
List: Benefits of Minimizing Steel Casting Defects
- Cost Savings:
- Reducing defects leads to lower material and labor costs, enhancing profitability.
- Increased Productivity:
- Fewer defects mean smoother production processes and higher output rates.
- Enhanced Product Quality:
- High-quality castings meet customer expectations and reduce returns and complaints.
- Improved Competitive Advantage:
- Consistently producing defect-free products enhances market reputation and attracts more business.
- Environmental Benefits:
- Minimizing waste and optimizing resource use contribute to more sustainable manufacturing practices.
Table: Future Prospects for Minimizing Defects and Enhancing Efficiency
Prospect | Description | Potential Benefits |
---|---|---|
Integration of Smart Manufacturing | Use of IoT, AI, and machine learning for defect prediction | Proactive defect prevention and correction |
Advanced Simulation Techniques | Use of CAE tools for process simulation and optimization | Reduced trial and error, optimized processes |
Material Innovations | Development of new alloys and composite materials | Reduced defect occurrence, enhanced properties |
Sustainability Initiatives | Focus on recycling and eco-friendly materials | Cost savings, environmental sustainability |
Conclusion
The economic impact of steel casting defects is significant, affecting both direct and indirect costs as well as opportunity costs. By understanding the common defects and their causes, and implementing effective strategies to minimize them, manufacturers can reduce waste, improve efficiency, and enhance product quality. Future prospects such as the integration of smart manufacturing technologies, advanced simulation techniques, material innovations, and sustainability initiatives hold promise for further minimizing defects and maximizing efficiency in steel casting operations. By adopting these strategies, the steel casting industry can achieve greater economic and environmental benefits, ensuring a more sustainable and profitable future.