At present, some industrial 3D printers have been used in casting production services, mainly for rapid prototyping of castings, turning mold, printing mold shell, sand core, etc. For example, domestic Wuhan Binhu electromechanical Co., Ltd. and Beijing Longyuan Co., Ltd. use laser sintering 3D printing to apply to the hot box process. Foreign countries, such as ex one company of Germany, have developed 3DP printer (as shown in the figure) which is specially used for casting sand core printing to realize die-free casting or digital casting. At present, it can print 1800 mm × 1000 mm × 700 mm overall sand mold or core at most. The technical equipment has been introduced by Ningxia sharing group company of China for development and production.

1) Printing sand core process
The method of printing sand core can be summarized as follows: Design sand core structure according to casting process (3D modeling) → import model file (STL format) into printing equipment for processing → prepare printing raw materials, set printing parameters → automatic printing and molding → absorb unused loose sand, take core cleaning → casting production.
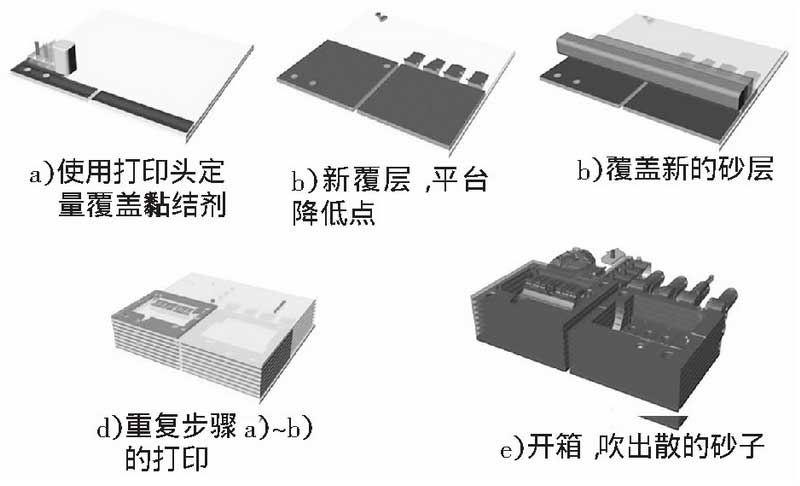
When printing, first lay a layer of sand (mixed curing agent) on the working box, then selectively spray chemical adhesive on the printing head, and alternate layer by layer, and finally self hardening, as shown in the figure.
2) Characteristics of 3D printing sand core
Without mold, complex sand mold / core can be made, especially the core which is difficult to form by mold. To realize the integrated molding of complex sand core and improve the molding accuracy.
The printing sand core has the advantages of large size, high precision, high speed and low cost. At present, most of the other printable sand mould equipments adopt laser sintering. The size of printable products is less than 500 mm × 500 mm × 500 mm, and the molding rate is only a few liters per hour. The printing accuracy of ex one sand core printer reaches 0.3 mm, and the size of the working box is 1800 mm × 1000 mm × 700 mm. It is the largest in the industry at present. It can form 108 l sand per hour. The raw materials are mainly conventional quartz sand, curing agent and bonding agent, and the cost is relatively low.
The printing sand core is solidified at room temperature without shrinkage deformation and can be used directly without subsequent processing.
It can print furan resin, phenolic resin, inorganic resin, etc. it can be used for aluminum, magnesium, iron, steel and other non-ferrous metal casting. It is suitable for sand casting in automobile, aviation, pump, large engine and machinery industries.
Compared with the traditional way of making core, the equipment has the advantages of automatic control, low labor intensity, low noise and dust pollution, and the remaining raw materials can be recycled.
The best cost performance can save about half of the production cost and cycle.
3) Application of 3D printing sand core
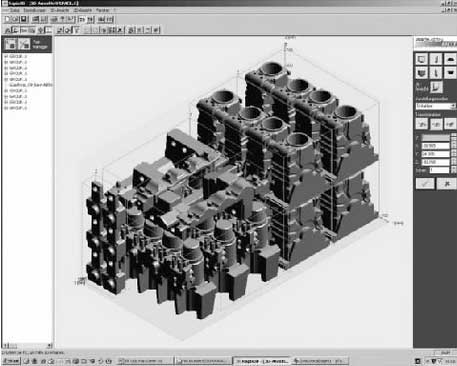
3D printing sand core is the best means of casting product development, the best guarantee of fast delivery, and the best economic way of specific small batch production (as shown in the figure, a box of multiple pieces layout). At present, ex one’s 3D printing sand core has been used in aerospace, automobile, pump and hydraulic, scientific research and development, foundry and related service industries. The application of some typical print cores is shown in the figure
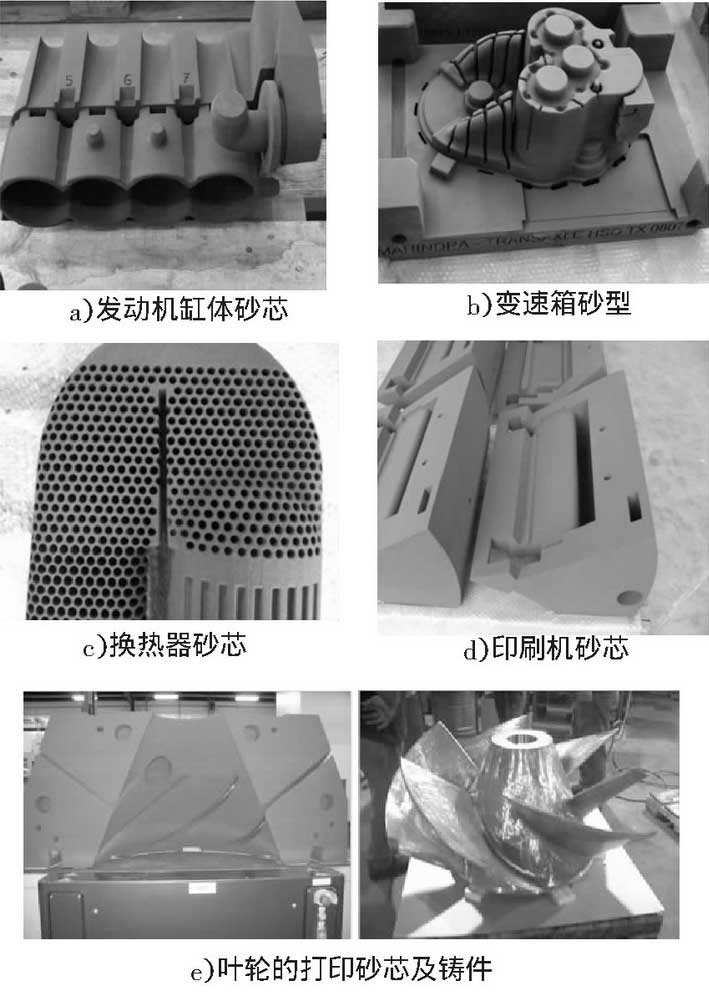