Advantages of 3D printing technology in sand casting
The emergence of 3D printing technology has certain advantages in additive manufacturing. At present, 3DP technology has a very good application prospect in the field of sand casting. First of all, molding and core making are generally considered to be one of the links with high labor intensity and bad production environment in the casting industry. The sand mold production with 3DP technology replaces the manual operation link. All molding processes are carried out in relatively closed boxes. Due to the particularity of 3D printing sand mold raw materials, there will be no dust in the printing process, The adhesive added for sand mold hardening is also carried out in a relatively closed box, which reduces the emission to the environment and greatly improves the working environment; secondly, the application of 3D printing technology in the field of sand mold casting omits the link of making mold, which not only saves the production cost, but also improves the speed and flexibility of product trial production, The foundry enterprises no longer need to spend a lot of money to build mold storage workshops and professional mold maintenance personnel; thirdly, the application of 3D printing technology in sand casting greatly improves the size accuracy of products, enhances the control ability of sand mold size, and becomes an accurate and controlled link. 3D printing will simplify the complex product sand mold, and reduce the dependence of enterprises on high-tech workers, Enhance product quality and eliminate subsequent product scrap due to dimensional problems. In addition, the precise dimensional control system can control product processing volume in a fine way to ensure that a small amount of processing allowance can be reserved in the design of product processing surface to improve the efficiency of subsequent product processing. Finally, The application of 3D printing technology in the field of sand casting provides sufficient guarantee for the flexibility of product design. Because 3D printing sand mold is not constrained by the size and shape of the product, the parameters can be changed at any time during the production process to modify the part or the whole, so as to improve the efficiency of product development and verification.
Application examples
Case 1
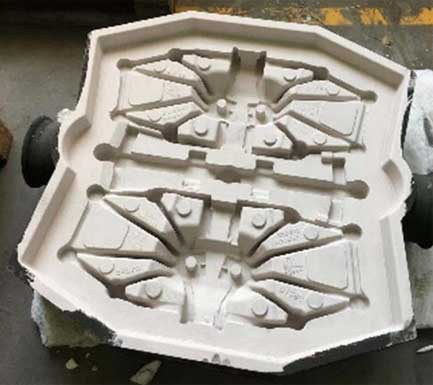
The steering gear parts of an automobile are shown in the figure. The casting structure is complex, there are many processing and assembly holes, and the casting mass is 34 kg. The traditional casting adopts the investment casting method for trial production and production. The investment casting needs to go through wax pressing, wax repairing, tree assembly, slurry staining, wax melting, pouring and post processing, among which the shell making process needs 3-5 times of repeated work to reach the semi-finished state, Long production cycle. In the trial production stage of auto parts, the time cycle determines the finished product cycle of the final product, and in the process of new product development and trial production, product structure, process plan and other links need to be modified many times. When 3D printing is used for production, the whole process is shortened to sand mold design (computer), sand mold printing, pouring metal liquid and post-processing, which greatly shortens the production cycle. Moreover, 3D printing sand mold documents are digital documents directly output by computer, which are easy to modify, flexible to change the process, quick to respond to change speed, so as to achieve the purpose of rapid trial production.
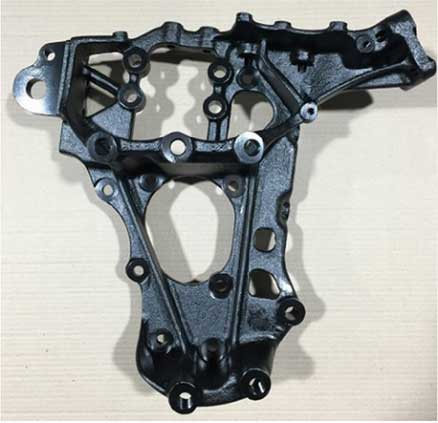
Case 2
As shown in the figure, the parts of an automobile engine have high dimensional accuracy requirements and complex structure. Considering the reasons of energy saving and efficiency improvement of the final assembly of the main engine products, the product has many weight reduction structures. In the traditional manufacturing process, this product is produced by the way of metal model and hot box core. The production cost of metal model is 200000-500000 yuan per set according to the complexity of the product, and the production cycle is about 2 months. Once the model is finalized, it is difficult to modify it. Therefore, in the stage of product trial production and R & D, 3D printing has the advantages of fast reaction speed, high dimensional accuracy and low cost of single piece and small batch, which can well solve all the requirements of the verification stage, until the product is fully verified and reaches the finalized state, then the metal mold can be produced for mass production, so as to save a lot of R & D costs for the enterprise and accelerate the R & D progress, To achieve the purpose of improving the competitiveness of enterprises’ products.
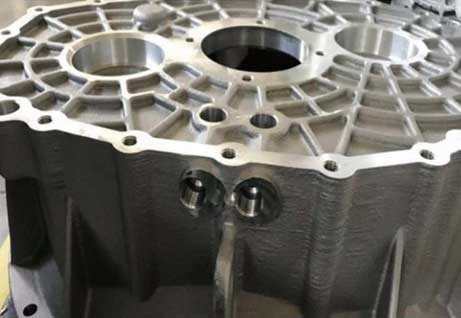
Case 3
As shown in Figure 3, due to the special working conditions of the product, a large number of heat sinks need to be designed around the product. Generally, the number of heat sinks of a motor shell product will reach 40-100, the depth of each heat sink is 100-120 mm, the length is about 100-1800 mm according to the product size, and the thickness of each heat sink is 4-8 mm, The gap between every two fins is 5-6 mm. Due to the particularity of the size parameters of the fins, in the traditional production mode, each fin structure on the product model needs to be made into an independent module as a separate structure, that is to say, if a motor product has 50 fins, 50 independent fin modules need to be made, In the traditional molding process, every module needs to be assembled. After sand filling and solidification, every module needs to be taken out from the sand mold, which is not only time-consuming and laborious, but also causes damage in the operation process, affects the shape of the heat sink, and in serious cases, the whole semi-finished product will be scrapped. 3D printing sand mold is a kind of additive manufacturing technology, which omits the production process of the product model and directly prints the sand mold. 3D printing sand mold does not consider the inclination of the traditional model, and can combine the complex structure for printing. When producing the motor shell with heat sink, it can combine the heat sink in a large area, which can not only ensure the size of each heat sink, It can also ensure the relative size of every two fins, effectively avoid the sand mold damage caused by the traditional casting method, and significantly improve the product quality.
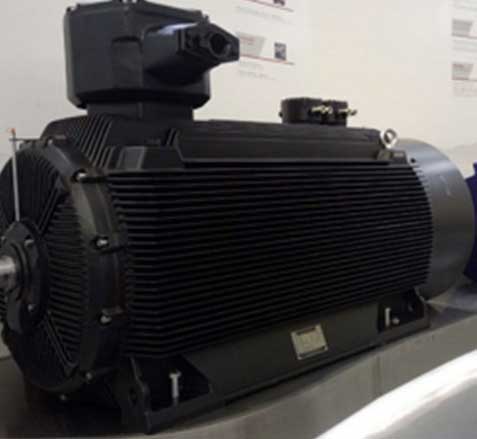