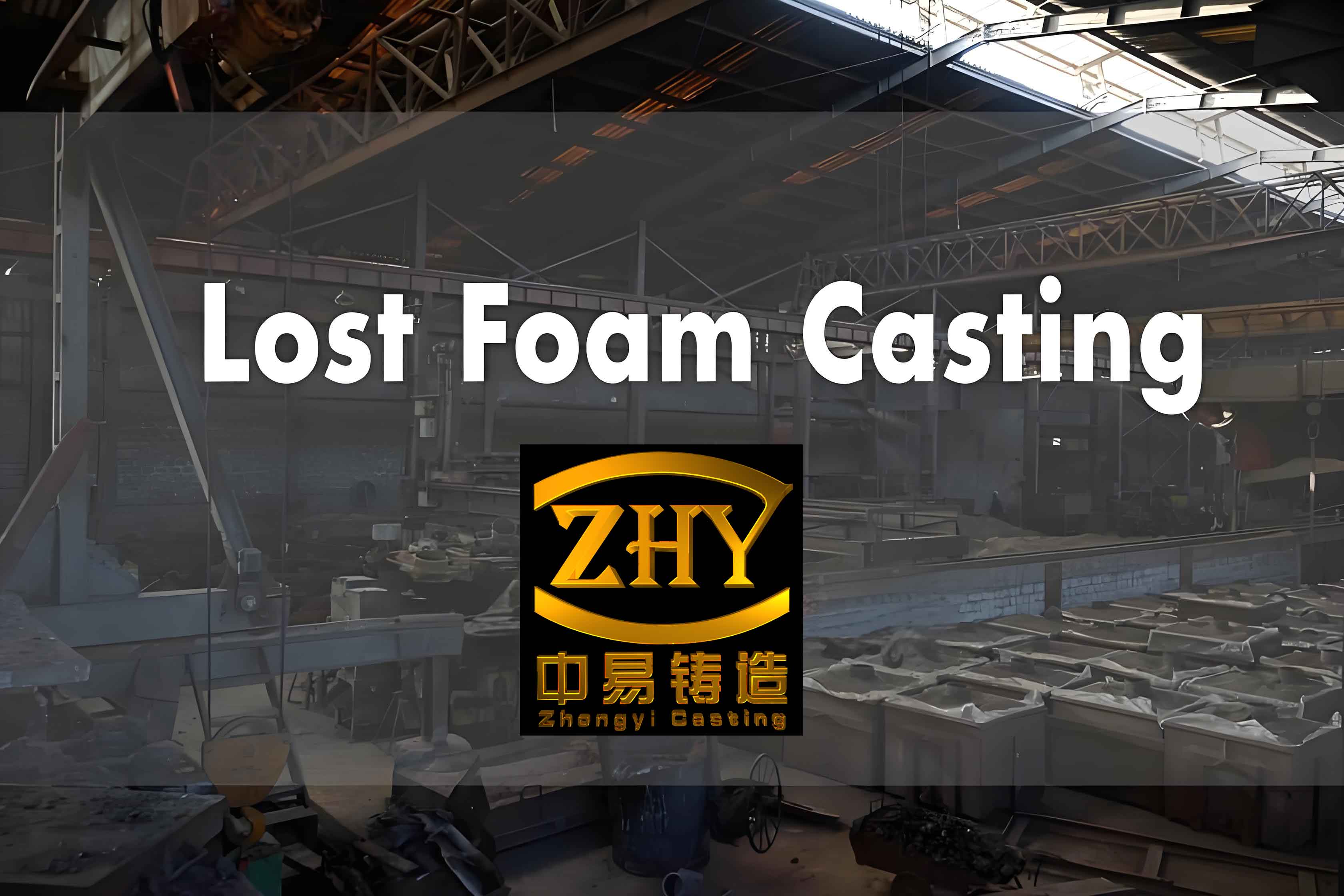
Lost foam casting is a highly versatile and precise casting method that is widely used across various industries, including the oil and gas sector. This method involves creating a foam pattern of the desired part, coating it with a refractory material, and then embedding it in a sand mold. When molten metal is poured into the mold, the foam pattern vaporizes, leaving behind a detailed metal casting. This article explores the applications of lost foam casting in the oil and gas industry, highlighting its benefits, common casting defects, and strategies for optimizing casting quality.
Introduction to Lost Foam Casting
Lost foam casting is renowned for its ability to produce complex and intricate metal components with high dimensional accuracy and excellent surface finish. The process is particularly advantageous for manufacturing parts that require minimal post-casting machining, making it ideal for the demanding applications in the oil and gas industry.
Key Steps in Lost Foam Casting
- Foam Pattern Creation: A foam model of the desired component is created using suitable foam materials.
- Pattern Assembly: The foam pattern is assembled with gating systems if needed.
- Coating: The foam pattern is coated with a refractory material to form a thin shell.
- Mold Preparation: The coated foam pattern is placed in a sand mold, and sand is packed around it.
- Metal Pouring: Molten metal is poured into the mold, causing the foam pattern to vaporize and be replaced by the metal.
- Mold Breakout: Once the metal has solidified, the sand mold is broken away to reveal the metal casting.
- Finishing: The casting is cleaned, and any excess material is removed to achieve the final product.
Benefits of Lost Foam Casting in the Oil and Gas Industry
The oil and gas industry requires components that can withstand harsh operating conditions, including high pressures, temperatures, and corrosive environments. Lost foam casting offers several benefits that make it an ideal choice for manufacturing such components:
- Complex Geometries: Capable of producing intricate shapes and complex geometries with high precision.
- Dimensional Accuracy: Ensures tight tolerances and high dimensional accuracy, reducing the need for extensive machining.
- Excellent Surface Finish: Provides a smooth surface finish, enhancing the performance and longevity of the components.
- Material Versatility: Suitable for casting a wide range of metals and alloys, including steel, aluminum, and cast iron.
- Cost-Effectiveness: Reduces material waste and machining time, leading to lower production costs.
Benefit | Description |
---|---|
Complex Geometries | Produces intricate shapes and complex geometries with high precision |
Dimensional Accuracy | Ensures tight tolerances, reducing the need for extensive machining |
Excellent Surface Finish | Provides a smooth surface finish, enhancing performance and longevity |
Material Versatility | Suitable for casting a wide range of metals and alloys |
Cost-Effectiveness | Reduces material waste and machining time, lowering production costs |
Common Applications in the Oil and Gas Industry
Lost foam casting is employed in the oil and gas industry to produce a variety of critical components that must meet stringent performance and durability standards. Some common applications include:
Valves and Valve Bodies
Valves and valve bodies are essential components in oil and gas systems, controlling the flow of fluids and gases. Lost foam casting allows for the production of complex valve designs with precise dimensions and smooth surfaces, ensuring reliable performance and sealing capabilities.
- Benefits: High dimensional accuracy, excellent surface finish, and complex geometries.
- Materials: Typically cast from steel or cast iron for durability and corrosion resistance.
Pumps and Pump Housings
Pumps and pump housings are critical for transporting fluids in oil and gas operations. Lost foam casting enables the production of intricate pump components that require minimal machining, ensuring efficient and reliable operation.
- Benefits: Precise dimensions, smooth surface finish, and reduced need for machining.
- Materials: Commonly cast from steel or stainless steel for strength and corrosion resistance.
Compressor Parts
Compressors are used to pressurize gases in various oil and gas processes. Lost foam casting is ideal for producing complex compressor parts with high precision and durability.
- Benefits: High dimensional accuracy, excellent surface finish, and complex geometries.
- Materials: Typically cast from aluminum or steel for lightweight and strength.
Fittings and Connectors
Fittings and connectors are crucial for joining pipes and other components in oil and gas systems. Lost foam casting allows for the production of fittings with precise dimensions and smooth surfaces, ensuring leak-proof connections.
- Benefits: Precise dimensions, smooth surface finish, and complex geometries.
- Materials: Commonly cast from brass, steel, or stainless steel for strength and corrosion resistance.
Manifolds
Manifolds are used to distribute fluids or gases to multiple destinations. Lost foam casting enables the production of complex manifold designs with high precision, ensuring efficient and reliable operation.
- Benefits: High dimensional accuracy, excellent surface finish, and complex geometries.
- Materials: Typically cast from steel or stainless steel for durability and corrosion resistance.
Component | Benefits | Materials |
---|---|---|
Valves and Valve Bodies | High dimensional accuracy, excellent surface finish, complex geometries | Steel, cast iron |
Pumps and Pump Housings | Precise dimensions, smooth surface finish, reduced machining | Steel, stainless steel |
Compressor Parts | High dimensional accuracy, excellent surface finish, complex geometries | Aluminum, steel |
Fittings and Connectors | Precise dimensions, smooth surface finish, complex geometries | Brass, steel, stainless steel |
Manifolds | High dimensional accuracy, excellent surface finish, complex geometries | Steel, stainless steel |
Common Casting Defects and Mitigation Strategies
Despite its advantages, lost foam casting can be susceptible to various casting defects that can compromise the quality and performance of the final product. Common casting defects and strategies to mitigate them include:
Gas Porosity
Gas porosity occurs when gases are trapped within the molten metal during the casting process, leading to small voids or cavities in the final casting.
- Causes: Moisture in the mold, reactions between the metal and mold materials, impurities in the metal.
- Mitigation Strategies: Use high-quality sand, ensure proper drying of the mold, optimize gating and venting systems, control pouring temperature.
Shrinkage Porosity
Shrinkage porosity occurs due to the natural contraction of metal as it cools and solidifies, leading to voids if the mold does not provide sufficient feed metal.
- Causes: Inadequate risers or feeders, improper cooling rates.
- Mitigation Strategies: Use adequate risers, optimize cooling rates, use chills to control solidification.
Surface Defects
Surface defects, such as roughness or inclusions, can compromise the surface finish and performance of the casting.
- Causes: Poor quality foam pattern, improper coating application, impurities in the sand.
- Mitigation Strategies: Use high-quality foam patterns, apply coatings uniformly, use clean and high-quality sand.
Casting Defect | Causes | Mitigation Strategies |
---|---|---|
Gas Porosity | Moisture in mold, reactions, impurities | High-quality sand, proper drying, optimize gating and venting, control pouring temperature |
Shrinkage Porosity | Inadequate risers/feeders, improper cooling rates | Use adequate risers, optimize cooling rates, use chills |
Surface Defects | Poor quality foam pattern, improper coating, impurities in sand | High-quality foam patterns, uniform coatings, clean sand |
Advanced Techniques and Technologies
To further enhance the quality and performance of lost foam cast components in the oil and gas industry, several advanced techniques and technologies can be employed:
Simulation and Modeling
Simulation and modeling tools can predict and optimize the casting process, helping identify and mitigate potential casting defects before production.
- Benefits: Predicts porosity, shrinkage, and other defects; optimizes gating and venting systems; improves overall casting quality.
Vacuum-Assisted Casting
Vacuum-assisted casting involves applying a vacuum to the mold cavity to remove gases and reduce porosity.
- Benefits: Removes trapped gases, reduces gas porosity, improves casting quality.
Inert Gas Purging
Purging the molten metal with inert gases such as argon or nitrogen can remove dissolved gases and reduce gas porosity.
- Benefits: Displaces dissolved gases, reduces gas porosity, results in cleaner metal.
Advanced Technique | Benefits | Applications |
---|---|---|
Simulation and Modeling | Predicts and optimizes casting process, reduces defects | General casting process optimization |
Vacuum-Assisted Casting | Removes trapped gases, reduces gas porosity | High-precision and high-quality castings |
Inert Gas Purging | Displaces dissolved gases, reduces gas porosity | Components requiring high purity and quality |
Conclusion
Lost foam casting offers significant advantages for the oil and gas industry, enabling the production of complex, high-quality metal components with excellent dimensional accuracy and surface finish. By understanding and mitigating common casting defects, and leveraging advanced techniques and technologies, manufacturers can further enhance the quality and performance of lost foam cast components. These advancements ensure that lost foam casting remains a valuable and effective method for producing reliable, high-performance parts that meet the stringent demands of the oil and gas industry.
Benefit | Description |
---|---|
Complex Geometries | Produces intricate shapes and complex geometries with high precision |
Dimensional Accuracy | Ensures tight tolerances, reducing the need for extensive machining |
Excellent Surface Finish | Provides a smooth surface finish, enhancing performance and longevity |
Material Versatility | Suitable for casting a wide range of metals and alloys |
Cost-Effectiveness | Reduces material waste and machining time, lowering production costs |
By focusing on these key benefits and addressing potential casting defects, the oil and gas industry can continue to rely on lost foam casting as a vital manufacturing process for critical components.