In the middle part of the workpiece, take a test bar with a diameter of 6 mm according to the national standard for tensile test. The processing parts of the test bar are shown in Figure 1 (a, B, C, D, e, f). The strength property of rheo squeeze casting is more stable than that of normal squeeze casting, but the elongation fluctuates greatly. The average elongation of the sample is 2992.5%, and the maximum tensile strength of the sample is 2991.5%. SEM scanning and EDS analysis of fracture surface were carried out for the sample with the best elongation and the sample with the worst elongation. See Fig. 5, FIG. 6, FIG. 7 and Fig. 8 for details. It can be seen from the figure that the elongation of different parts fluctuates greatly, which is related to the inclusion of oxide scale and other impurities during rheo squeeze casting.
The main factors affecting the mechanical properties of squeeze casting parts are slurry quality, process parameters, process control, etc., which are reflected in the micro level, mainly reflected in the size of equiaxed grains and the width of columnar crystal zone. The lspsf semi-solid pulping process can improve the crystallization of the alloy at the initial stage of solidification, and obtain finer spherical or near spherical primary solid slurry than ordinary casting. The microstructure of 7075 alloy formed by rheo squeeze casting is finer spherulite or near spherulite. Because the semi-solid slurry itself has a certain apparent viscosity and is not easy to produce eddy current and splash during pouring and squeeze casting, it can make the structure more compact at higher specific pressure and avoid the generation of shrinkage cavity and porosity, so the mechanical properties are greatly improved. However, if there are non-metallic impurities or some intergranular segregation at the grain boundary, the properties of squeeze casting parts will be greatly affected. How to reduce segregation and inclusion is the main problem to improve the mechanical properties of rheo squeeze casting parts on the premise of obtaining refined crystal structure. Due to the intrinsic problems of rheoforming such as entrainment defects and intergranular segregation, the mechanical properties do not have high stability, which is the key problem to be solved urgently in the engineering application of rheoforming.
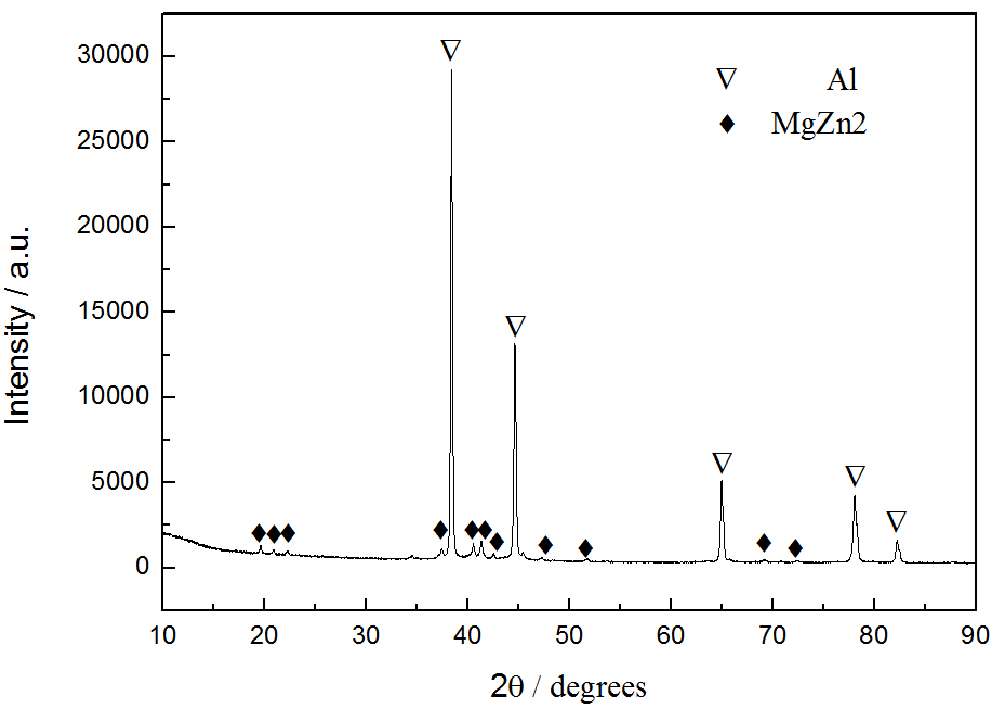
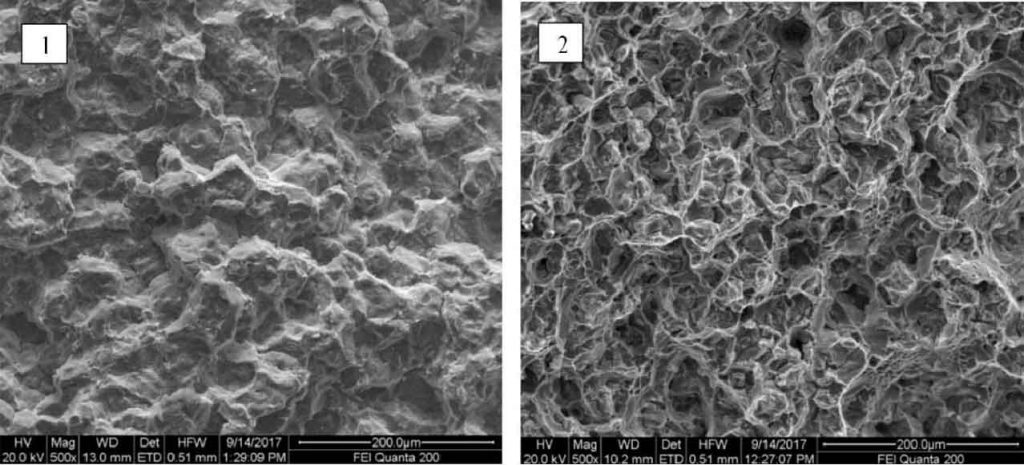
Fig. 3 (a) is a high-power image of the microstructure of 7075 alloy in position 2 (Fig. 1) of liquid squeeze casting without lspsf process. Figure 3 (b) is a high-power image of the microstructure corresponding to the same position 2 (see Figure 1) of the same batch of 7075 alloy formed by lspsf process. It can be seen from the figure that there is intergranular segregation at the intersection of grain boundaries in 7075 alloy parts formed by squeeze casting of alloy melt with two methods. According to the comparison between (a) and (b) in Fig. 3, the intergranular segregation of lspsf process is finer, which is mainly due to the fact that the pouring temperature of semi-solid slurry after rotating tube is lower than that of ordinary liquid squeeze casting, which contains less heat and can complete solidification in a shorter time when crystallizing under pressure.
The XRD pattern of 7075 alloy by rheo squeeze casting (Fig. 4) shows that only mgzn2 compound is found in the matrix, and no other impurity phase is found.
For sample B, inclusions were found near the crack source by SEM scanning, as shown in Figure 7. EDS analysis of the impurity point shows that the impurity elements are mainly C and O, which is mainly caused by a small amount of oxide inclusions mixed into the alloy melt in the process of rheo squeeze casting. The appearance of the inclusions leads to the obvious dissociation fracture characteristics of sample B. Obvious dimples were found in the SEM morphology of sample e, and its plasticity reached 23.33%. EDS analysis from the fracture surface (Fig. 8) showed that the components were all the constituent elements of 7075 alloy, and no impurities or oxidation elements were found.