Sand slag hole is the most common surface defect of sand mold casting, which is difficult to avoid and usually accounts for the majority of waste products. Therefore, it is necessary to give full play to the sand and slag avoidance functions of the upper horizontal runner (Fig. 1).
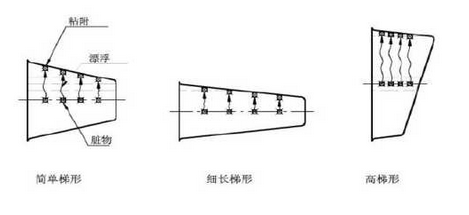
It is an effective way to absorb the impurities in the initial molten metal to connect the vertical runner and the horizontal runner by lapping. The purpose of overlapping the runner of one half sand mold and another half sand mold is to overlap. The purpose is to prolong the time for molten metal to pass through the horizontal gate as far as possible before the molten metal starts to flow vertically, so that the horizontal runner is filled with molten metal as soon as possible, so as to ensure that the impurities have enough time to float up and adhere to the upper surface of the runner, so as to avoid flowing into the sprue.
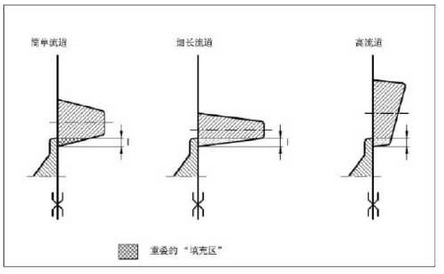
It is also necessary to design the upper horizontal runner extending beyond the sprue lap area (Fig. 2, 3). The effect is to capture the initial low temperature and dirty liquid metal, the cross-sectional area extends to the end, and the reason is that the flow velocity is gradually reduced to avoid the rebound of molten metal after impact, and the formation of eddy current in the lap area.
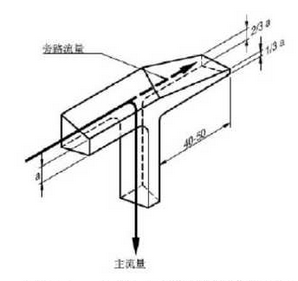
The flow rate of molten metal flowing through the sprue should be equal at each height, which can be described by the following formula,

Q represents the flow rate of the section, a represents the cross-section area, and V is the velocity of metal passing through the section. The permeability of molding sand has a certain influence on the flow rate, which makes the filling process complicated. The following figure shows the state of molten metal flowing through the sprue in three cases. Affected by the acceleration of gravity, the flow rate of the casting increases with the falling of the liquid, so the cross-sectional area of the sprue needs to be reduced to balance the overall flow rate.
As shown in Fig. B, if the cross-sectional area of the sprue is consistent, a low-pressure area will be formed in the sprue, and the molten metal will not contact with the sand mold, resulting in gas invasion and turbulence, especially when the molten metal reaches the bottom of the sprue. The use of conical sprue (Fig. C) can make the upper and lower pressure in the runner consistent, and the molten metal can completely fill the runner and contact with the sand mold to prevent gas invasion and turbulence.
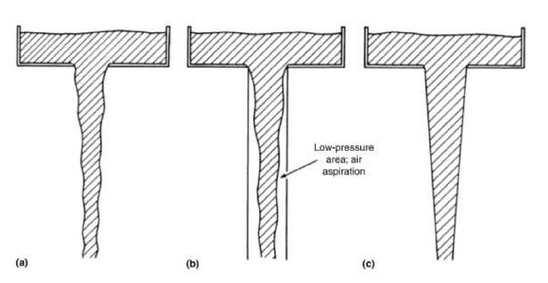