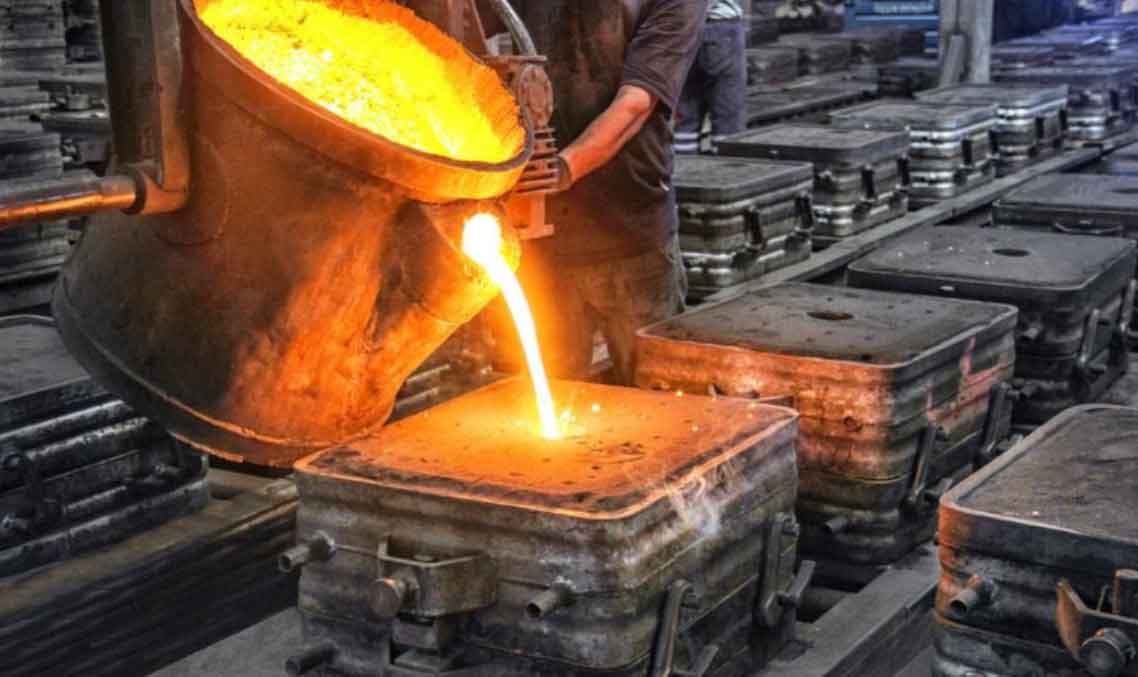
The pricing in sand casting manufacturing is influenced by various factors that contribute to the overall cost of producing castings. Understanding these cost factors helps both manufacturers and customers determine the pricing of sand casting components. Here are the key factors affecting pricing in sand casting manufacturing:
1. Material Selection:
- The choice of casting material significantly impacts the cost. Different metals and alloys vary in price, and some may require special handling or processing, affecting the overall cost.
2. Component Design Complexity:
- The complexity of the casting design affects the cost. More intricate and complex designs may require additional pattern-making and molding efforts, leading to higher costs.
3. Pattern and Tooling Costs:
- The creation of patterns and tooling for sand casting incurs initial costs. Complex designs or large-scale production runs may require more expensive tooling, contributing to the overall pricing.
4. Production Volume:
- The volume of castings ordered influences the pricing. Higher production volumes often result in reduced per-unit costs due to economies of scale.
5. Raw Material Costs:
- The cost of sand, additives, and metal alloys directly impacts the overall pricing of sand castings.
6. Labor Costs:
- The labor required for mold preparation, core making, casting, finishing, and quality control contributes to the overall cost. Labor costs may vary depending on the geographic location of the foundry.
7. Process Complexity:
- Certain sand casting processes may involve additional steps, such as core making, heat treatment, or post-casting finishing, which can affect the overall pricing.
8. Inspection and Quality Control:
- Rigorous inspection and quality control measures are essential to ensure casting integrity. These efforts may add to the overall cost of production.
9. Scrap and Rework Rates:
- Higher scrap and rework rates lead to increased material wastage and additional labor, impacting the overall cost.
10. Post-Casting Finishing:
- Additional finishing processes, such as machining, surface treatments, or painting, may incur extra costs.
11. Market Demand and Competition:
- Market demand and competition can influence pricing. In competitive markets with many foundries, prices may be more competitive.
12. Supplier Reputation and Expertise:
- Established and reputable foundries with proven expertise may command higher prices due to their track record of quality and reliability.
13. Energy Costs:
- Energy costs, including electricity and fuel, contribute to the overall cost of production.
14. Environmental Compliance Costs:
- If a foundry implements eco-friendly practices or meets specific environmental regulations, it may incur additional compliance costs that could be reflected in the pricing.
It’s important to note that these factors are interconnected, and a comprehensive analysis of the entire production process is necessary to determine the final pricing of sand casting components. Manufacturers and customers can collaborate to optimize the design and production process to strike a balance between cost-efficiency and the quality of the final castings.