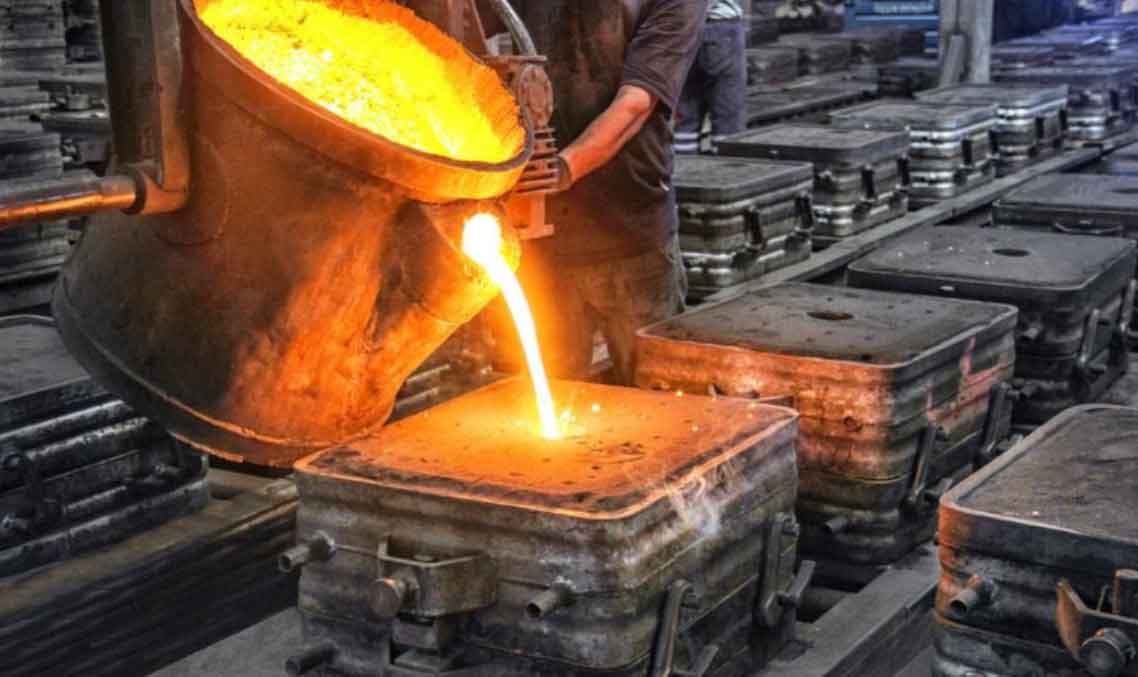
Automation and robotics play a significant role in modern sand casting manufacturing, revolutionizing traditional processes and offering numerous benefits to foundries and their customers. The integration of automation and robotics enhances efficiency, improves casting quality, reduces labor-intensive tasks, and enables foundries to remain competitive in today’s rapidly evolving manufacturing landscape. Here are the key roles of automation and robotics in modern sand casting manufacturing:
1. Pattern Making and Mold Assembly:
- Automated systems can produce patterns with high precision using 3D printing or CNC machining. This reduces lead times and enables rapid prototyping for design validation. Robots can also assist in mold assembly, ensuring accuracy and consistency in the process.
2. Material Handling and Pouring:
- Robots are used to handle heavy molds and pour molten metal into the molds, reducing the physical strain on human workers and ensuring consistent pouring practices.
3. Gating and Risering Design Optimization:
- Casting simulation software, integrated with automation, allows for the optimization of gating and risering designs to improve material flow and minimize defects.
4. Core Production and Placement:
- Automation facilitates the production of cores used in complex casting designs. Robots can accurately place cores in the molds, ensuring proper geometries and alignment.
5. Cleaning and Finishing:
- Automated systems can perform cleaning and finishing operations on castings, improving consistency and reducing post-processing time.
6. Quality Control and Inspection:
- Robots and automated inspection systems can conduct non-destructive testing, dimensional measurements, and defect detection, ensuring high-quality castings and reducing human errors.
7. Data Collection and Analysis:
- Automation allows for real-time data collection and analysis, providing insights into the casting process, identifying patterns, and optimizing process parameters.
8. Enhanced Safety:
- Robots are capable of handling hazardous tasks, such as molten metal pouring or heavy lifting, reducing the risk of workplace accidents and improving worker safety.
9. Increased Productivity and Efficiency:
- Automation and robotics can work continuously, 24/7, without fatigue, resulting in increased production throughput and reduced cycle times.
10. Consistency and Reproducibility:
- Robots perform tasks with high precision and consistency, ensuring that each casting is nearly identical, minimizing variability and defects.
11. Adaptability and Flexibility:
- Modern automation systems are designed to be adaptable and reprogrammable, allowing for easy changes to accommodate different casting requirements.
12. Labor Savings and Cost Efficiency:
- By automating repetitive and labor-intensive tasks, foundries can reduce labor costs, improve resource utilization, and enhance cost efficiency.
Automation and robotics in sand casting manufacturing offer significant advantages, including improved productivity, consistent quality, enhanced safety, and the ability to tackle complex designs and high-volume production. As technology continues to advance, the role of automation and robotics in sand casting is expected to grow, further transforming the industry and unlocking new possibilities for foundries and their customers.