In recent years, resin sand casting has seen significant advancements and innovations that have further improved the efficiency, precision, and capabilities of the process. Some notable innovations in resin sand casting techniques include:
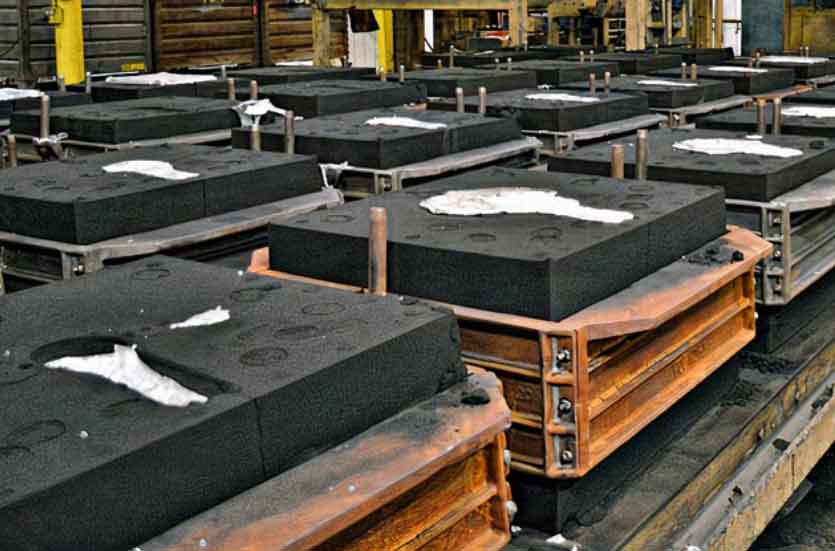
- 3D Printing for Sand Molds: Integration of 3D printing technology with resin sand casting has revolutionized the pattern-making process. Instead of traditional patterns, manufacturers can now create intricate and custom molds directly from digital designs. This approach reduces lead times, enables rapid prototyping, and allows for complex geometries that were previously challenging to achieve.
- Simulation and Modeling Software: Advanced simulation and modeling software have become crucial tools for optimizing resin sand casting processes. These tools allow manufacturers to predict potential defects, optimize gating and risering systems, and simulate the flow of molten metal inside the mold. By identifying potential issues before actual production, manufacturers can improve casting quality and reduce waste.
- Automated Mixing and Sand Preparation: Automation in sand mixing and preparation has streamlined the casting process, ensuring consistent sand properties and reducing human errors. Automated systems precisely control the sand-to-resin ratio, resulting in higher mold strength and improved surface finish.
- Binder Systems and Resin Formulations: Research and development efforts have led to the formulation of advanced resin binders that offer better strength, reduced emissions, and enhanced reclaimability. These binders provide greater mold stability and help minimize environmental impacts.
- Improved Cooling and Solidification Control: Innovations in mold and core design, as well as cooling techniques, have optimized the solidification process during casting. This results in reduced shrinkage and improved dimensional accuracy of the final parts.
- Robotics and Automation in Post-Processing: Automation and robotics are increasingly being used in post-processing operations, such as cleaning, finishing, and inspection of cast parts. This reduces manual labor, improves consistency, and ensures higher quality standards.
- Green Sand Reclamation: The recycling and reclamation of green sand have become more efficient and environmentally friendly. Reclamation systems recover and recondition sand, reducing waste and minimizing the need for fresh sand.
- In-Mold Coatings: The use of specialized coatings inside the mold cavity can improve the surface finish of cast parts and prevent defects like veining and penetration.
- Improved Casting Simulation Software: Casting simulation software has evolved, becoming more accurate and capable of handling complex geometries. This allows manufacturers to optimize the casting process and predict potential defects with greater accuracy.
These innovations in resin sand casting techniques have opened up new possibilities for manufacturers in various industries. The combination of advanced materials, digital technologies, and process optimization has made resin sand casting a versatile, efficient, and environmentally friendly casting method for producing high-quality components. As the industry continues to evolve, further advancements are expected to drive continuous improvements in resin sand casting processes.