Sand casting parts indeed offer cost-effective solutions for both small and large-scale production. Here are some key factors that contribute to their cost-effectiveness:
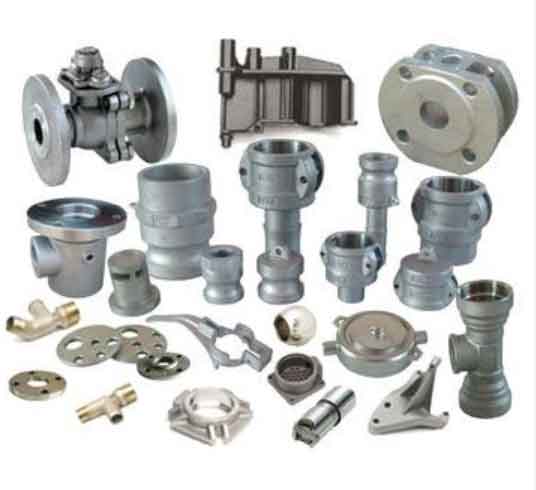
- Low Tooling Costs: Sand casting molds are relatively simple and cost-effective to create compared to other casting methods, such as die casting or investment casting. This results in lower initial tooling costs, making sand casting an attractive option for small-scale production runs and prototypes.
- High Production Efficiency: Once the sand molds are prepared, the casting process itself can be highly efficient, enabling the production of multiple parts in a short time. This efficiency is particularly advantageous for larger production runs, where the per-unit cost can be significantly reduced.
- Material Flexibility: Sand casting allows for a wide variety of materials to be used, including various metals and alloys. This versatility gives manufacturers the flexibility to select the most suitable material based on cost, performance requirements, and application.
- Reusability of Sand Molds: Sand molds used in sand casting can be reused multiple times, reducing material waste and lowering the overall production costs. Additionally, the reclaimed sand can be reconditioned and used again, further contributing to cost savings.
- Design Flexibility: Sand casting offers considerable design flexibility, allowing complex shapes and geometries to be cast without the need for costly and intricate tooling. This enables designers to optimize designs for both functionality and cost-effectiveness.
- Scalability: Sand casting can be easily scaled up or down to meet the production demands. Whether it’s a small batch of specialized components or a large-scale production run, sand casting can efficiently accommodate varying production volumes.
- Rapid Prototyping: Sand casting allows for rapid prototyping, which is crucial for cost-effective product development. Engineers can quickly iterate and test designs, identify potential issues, and make necessary adjustments before committing to full-scale production.
- Minimal Secondary Processing: Depending on the complexity of the part and the desired finish, sand casting often requires minimal secondary processing. The reduced need for additional finishing steps helps to keep costs in check.
- Local Sourcing: Sand casting materials and equipment are readily available in many regions, allowing manufacturers to source materials locally, reducing transportation costs and lead times.
- Economies of Scale: Sand casting benefits from economies of scale, meaning that as production volumes increase, the per-unit cost tends to decrease. This makes it cost-effective for larger production runs.
While sand casting offers cost-effective solutions for many applications, it is essential to consider specific project requirements and design considerations. In some cases, other casting methods might be more suitable for achieving even higher cost-effectiveness or specific performance criteria. Therefore, collaborating with experienced foundries and engineers can help optimize the cost-effectiveness of sand casting parts for a wide range of production scales and applications.