(1) The main processing procedure of the diesel engine transmission shaft forging is forging isothermal normalizing rough machining ut flaw detection quenching tempering finishing nitriding the forging diagram of the shaft is shown in Fig. 1.
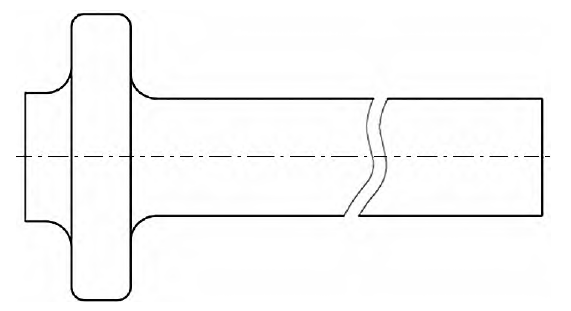
(2) The forging of the shaft is formed by tr upsetting technology. The TR upsetting die diagram is shown in Fig. 2. The equipment is 5MN press, the equipment pressure is 4800 kn, and the forging ratio is 5.1. The forming process of TR upsetting equipment is divided into two stages: operation stage and forming stage; in operation stage, TR upsetting equipment has fast movement speed and small pressure, which can effectively prevent heat loss; in forming stage, TR upsetting equipment has slow motion speed and high pressure, and the maximum extrusion pressure can be 1.25 times of the rated pressure of the press, which helps to fill the flange fillet fully.
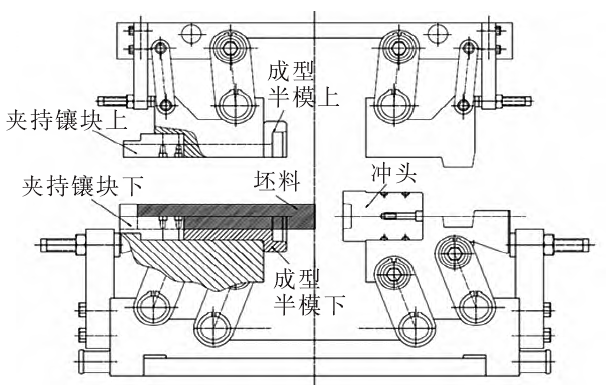
(3) The forging temperature range of 42crmoh steel is 1150 ~ 850 ℃. The shaft is heated by local induction heating. The medium frequency induction furnace parameters are 500kW, 50Hz, the heating diameter is 110mm and the heating length is 400mm. Before each shift of production, the temperature is verified by fixed infrared thermometer and hand-held infrared thermometer, and the heating time is recorded by time relay, Ensure that the heating temperature meets the requirements of forging temperature range. The frequency of temperature sampling was 100%.
(4) According to the skin effect principle, when there is alternating current or alternating electromagnetic field in the conductor, the current distribution inside the conductor is uneven. The current is concentrated on the surface of the conductor. The closer to the surface of the conductor, the greater the current density and the higher the temperature, while the internal current is small and the temperature is low. When the temperature is higher than Curie point, the current penetration depth of ferromagnetic conductor increases sharply, the current density inside the conductor increases, and the temperature increases. Finally, the surface and interior temperature of the conductor tend to be constant. After the infrared temperature measurement test, when the external temperature reaches the forging temperature, the core temperature will be (50 ± 5) ℃ lower than the outer surface temperature.
(5) The stress field analysis can be seen from Fig. 1 that the deformation of the outer circle of the flange plate is the largest during the forging process of the transmission shaft, so the stress is the most concentrated. The stress analysis is shown in Fig. 3: the finite element stress analysis is carried out for the annular zone I in the figure 3, and σ 3 and σ 2 in Fig. 3 are the compressive stress, σ 1 is the tensile stress, and the zone II in Fig. 3 is the zone II σ 1, σ 2 and σ 3 are all compressive stress, so the forging is easy to crack due to tensile stress from zone I (the largest outer circle of flange) during forging.
(6) According to the skin effect principle of induction heating, the surface temperature of the forging is higher. Therefore, if the forging has overheated and overburned structure, the overheated and overburned structure exists in zone I in Fig. 3. According to the stress analysis during upsetting (Fig. 3), due to the tensile stress at the outer circle, if there is overheated and overheated structure, the grain boundary will melt and the intergranular adhesion will decrease. As the deformation of the flange outer circle is the most severe, it will inevitably crack due to tensile stress at the maximum outer circle. After rough turning, no crack was found through ut inspection, which proves that the forging heating temperature is normal. Therefore, it is suspected that the crack is related to the raw material.
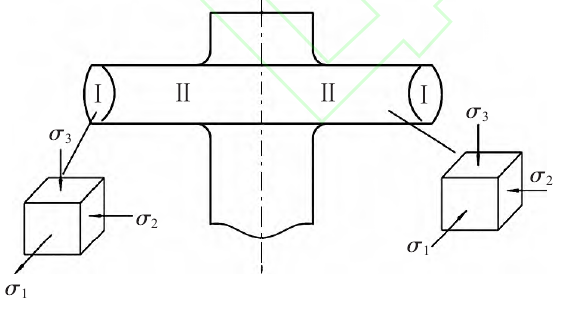