The thickness of chill is designed according to the chill of gray iron casting, as shown in the formula
Where s is the thickness of the casting or the diameter of the hot spot at the chilled part of the chill, where s = 520mm.
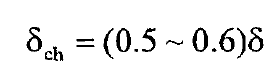
Then the thickness of chill is δ ch = (0.5-0.6) 520 = (260-312) mm, and the thickness of chill is 300 mm. The distance between chill layers is 30mm, and the chill is evenly distributed on the inner and outer walls of the test block.
Commonly used metal mold materials are gray cast iron, ductile iron, cast steel (including carbon steel, structural steel, tool steel, etc.), copper, etc. Gray cast iron is the most commonly used metal mold material with low price and good processing performance, but poor high-temperature mechanical properties, which is easy to produce cracks; ductile iron has good heat resistance and corrosion resistance, with small crack tendency and deformation tendency; cast steel has good mechanical properties, but high cost and processing cost, which is easy to weld with castings; copper has fast heat transfer speed and high thermal conductivity However, it is easy to produce white cast iron and the cost is high.
Considering the factors of cost, processability and casting performance, ductile iron is selected as the material of metal mold; from the point of view of process and manufacturing, the same material as ductile iron nuclear spent fuel container is selected as the material of metal mold, that is, qt400-18.