The wear-resistant lining plate is the main vulnerable and consumable part of the ball mill in the beneficiation industry. When the wet mill works, the lining plate will bear the impact and grinding stripping of materials and grinding balls in the corrosive mineral loading environment, resulting in various forms of friction loss of the lining plate, such as shear wear, impact wear, fatigue wear, abrasive wear and chemical corrosion, This makes the ball mill liner become an important cost expenditure of mine ore production industry. At present, mineral concentrators of various materials and minerals are distributed all over the country, and wet ball mill equipment is widely used. Tons of ore processed in the beneficiation industry often consume more than 1kg of metal, with an annual demand of more than 200000 tons of lining plate and 12000 yuan / ton of lining plate casting. It is preliminarily estimated that the wet grinding resistant lining plate for mining is a product with a market scale of several billion.
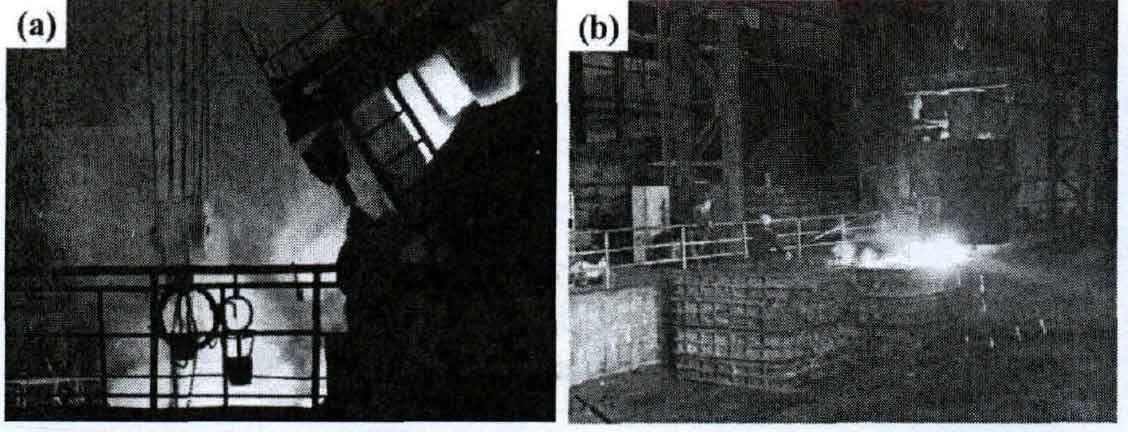
The service life of the lining plate made of traditional high-strength steel and alloy steel is less than 7 months. The service life of the lining plate purchased by a large domestic concentrator with expensive US dollars is only 9 months. The service life of the lining plate is short, causing workers’ labor when replacing the lining plate
High intensity, long shutdown time and troublesome operation procedures. Therefore, a lot of manpower, material resources and funds are invested, which directly affects the production efficiency and economic benefits of the enterprise.
ZHY casting signed a cooperation contract with the Key Laboratory of mold of Huazhong University of science and technology and the National Society of lost foam casting, and took the lead in adopting the bimetallic liquid lost foam composite casting method in China to carry out the research and development of carbon steel high complex cast iron bimetallic wear-resistant lining plate suitable for wet ball mill.
High chromium cast iron is the most excellent wear-resistant material in modern times. Its metallographic structure and properties are especially suitable for the service environment of wet abrasive wear. However, the high chromium cast iron with eutectic structure as the main body is difficult to have the comprehensive performance of strong and strong direction. A new composite lining plate suitable for mine wet ball mill is studied and developed. The better the wear resistance of general materials, the higher the hardness and the worse the adaptability of subsequent machining. The lining plate needs high dimensional accuracy to meet the assembly requirements of the inner wall of the silo of the football mill, and needs high surface quality to reduce the friction coefficient. These are difficult to be guaranteed by traditional sand casting, so the lost foam casting process is selected for production.
Based on the bimetallic liquid lost foam composite casting method, the lining plate of mining ball mill is prepared, which not only has the high strength and high wear resistance of eutectic high chromium cast iron, but also has the high toughness and high ductility of eutectoid steel. Its strong initial combination is characterized by the comprehensive properties that are difficult to be achieved by traditional single materials. Research on solving the contradiction between hardness and toughness can not only reduce the production cost, but also provide theoretical support and practical process guidance for the convenient and reliable mass production of new wear-resistant composites, which has obvious economic benefits and academic significance.