Lost foam casting has become a prominent technique in the manufacturing industry, particularly in the production of complex and high-precision components for heavy machinery. Its ability to produce intricate designs with high dimensional accuracy and minimal material waste has made it an invaluable tool for manufacturers. This article presents several case studies of successful lost foam casting projects in heavy machinery manufacturing, highlighting the benefits, challenges, and outcomes of each project.
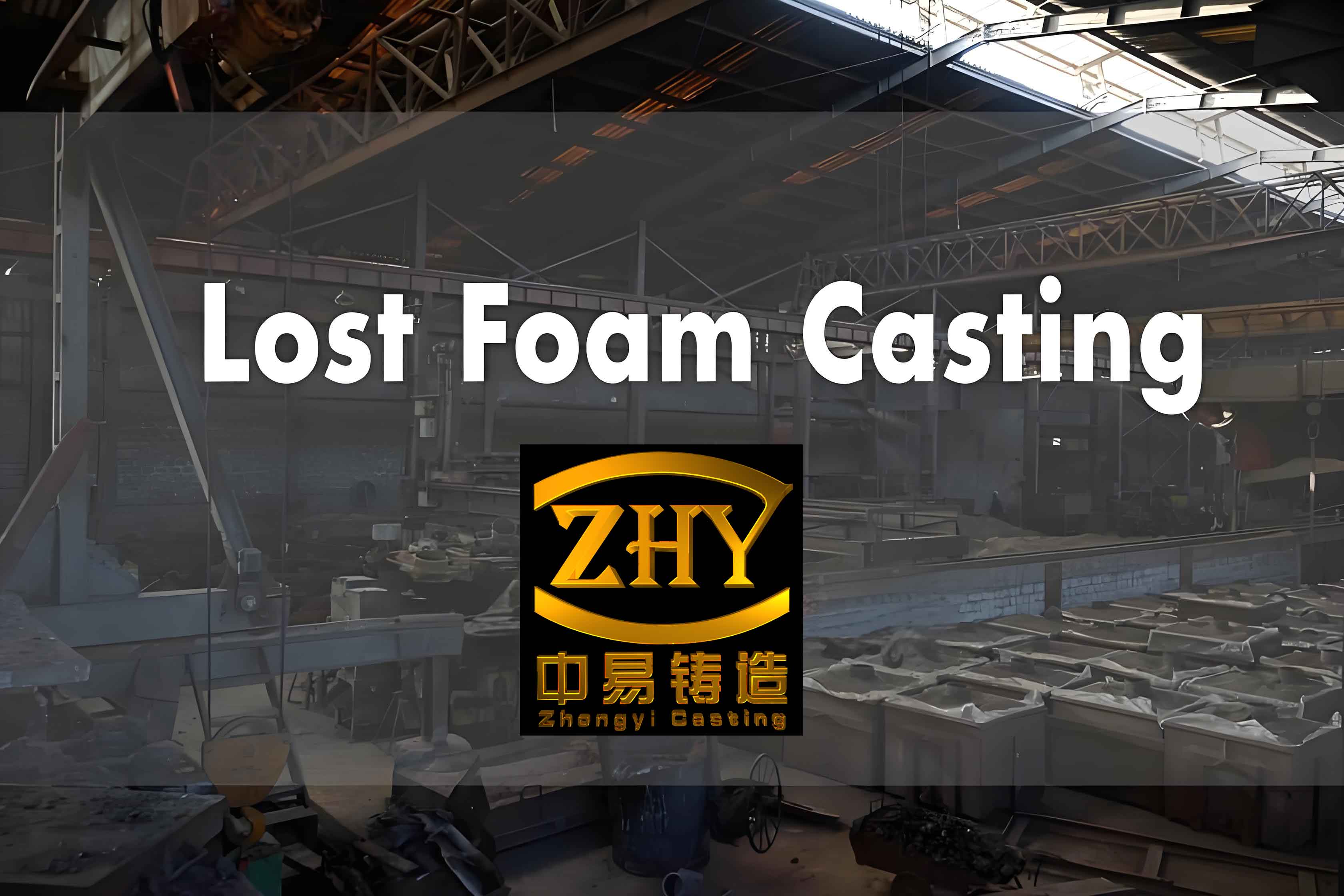
Case Study 1: Engine Blocks for Construction Equipment
Company: ABC Heavy Machinery
Project Overview: ABC Heavy Machinery, a leading manufacturer of construction equipment, sought to improve the quality and performance of their engine blocks. Traditional casting methods resulted in high material waste and required extensive post-processing. The company decided to implement lost foam casting to address these issues.
Implementation:
- Pattern Creation: Expanded polystyrene (EPS) patterns were created to represent the complex geometry of the engine blocks.
- Coating and Mold Preparation: The foam patterns were coated with a refractory material and placed in sand molds.
- Metal Pouring and Cooling: Molten metal was poured into the molds, vaporizing the foam patterns and forming the engine blocks. The molds were allowed to cool and solidify.
Results:
- Improved Quality: The precision and surface finish of the engine blocks improved significantly, reducing the need for post-processing.
- Material Efficiency: Material waste was reduced by 25%, contributing to cost savings and more sustainable manufacturing practices.
- Cost Savings: Overall production costs decreased by 15% due to reduced material waste and machining requirements.
Key Takeaways:
- Lost foam casting enabled the production of high-quality engine blocks with complex geometries.
- The process resulted in significant material and cost savings for ABC Heavy Machinery.
Case Study 2: Gear Housings for Mining Equipment
Company: DEF Mining Solutions
Project Overview: DEF Mining Solutions specializes in the production of heavy-duty mining equipment. The company faced challenges with the production of gear housings, which required high dimensional accuracy and durability. Lost foam casting was chosen to enhance the manufacturing process.
Implementation:
- Pattern Creation and Assembly: Foam patterns were created and assembled into clusters to cast multiple gear housings simultaneously.
- Coating and Mold Preparation: The patterns were coated with a refractory material and placed in sand molds for support during casting.
- Metal Pouring and Solidification: Molten metal was poured into the molds, vaporizing the foam patterns and forming the gear housings. The molds were cooled and the castings solidified.
Results:
- Enhanced Durability: The gear housings produced using lost foam casting exhibited superior durability and performance.
- High Precision: The dimensional accuracy of the gear housings improved, reducing the need for extensive machining.
- Production Efficiency: The ability to cast multiple components simultaneously increased production efficiency by 20%.
Key Takeaways:
- Lost foam casting improved the quality and durability of gear housings for mining equipment.
- The process enhanced production efficiency and reduced the need for post-processing.
Case Study 3: Hydraulic Pump Components for Agricultural Machinery
Company: GHI Agri-Industries
Project Overview: GHI Agri-Industries, a manufacturer of agricultural machinery, needed to produce high-precision hydraulic pump components. Traditional casting methods resulted in inconsistent quality and high material waste. Lost foam casting was implemented to address these challenges.
Implementation:
- Pattern Creation: EPS foam patterns were designed to replicate the complex shapes of hydraulic pump components.
- Coating and Mold Preparation: The patterns were coated with a refractory material and surrounded by unbonded sand in molds.
- Metal Pouring and Cooling: Molten metal was poured into the molds, vaporizing the foam patterns and forming the pump components. The molds were allowed to cool and solidify.
Results:
- Consistent Quality: The hydraulic pump components exhibited consistent quality and high dimensional accuracy.
- Reduced Material Waste: Material waste was reduced by 30%, contributing to significant cost savings.
- Improved Production Time: The production time for hydraulic pump components decreased by 25% due to the efficiency of the lost foam casting process.
Key Takeaways:
- Lost foam casting ensured the production of high-precision hydraulic pump components with consistent quality.
- The process resulted in reduced material waste and improved production efficiency.
Comparative Analysis of Lost Foam Casting Projects
The following table provides a comparative analysis of the key benefits and outcomes of the lost foam casting projects described above:
Aspect | ABC Heavy Machinery | DEF Mining Solutions | GHI Agri-Industries |
---|---|---|---|
Product | Engine Blocks | Gear Housings | Hydraulic Pump Components |
Improved Quality | High precision and superior surface finish | Superior durability and performance | Consistent quality and high dimensional accuracy |
Material Efficiency | Reduced material waste by 25% | Reduced material waste | Reduced material waste by 30% |
Cost Savings | Decreased production costs by 15% | Enhanced production efficiency | Significant cost savings |
Production Efficiency | Improved due to reduced post-processing | Increased production efficiency by 20% | Improved production time by 25% |
Environmental Impact | More sustainable manufacturing practices | Reduced need for machining | Environmentally friendly process |
Challenges and Solutions in Lost Foam Casting
While lost foam casting offers numerous advantages, it also presents certain challenges that manufacturers must address:
- Pattern Fragility: Foam patterns can be delicate and require careful handling to avoid damage.
- Solution: Implementing rigorous quality control measures and training employees to handle foam patterns with care.
- Process Control: Precise control of temperature and mold conditions is crucial for consistent quality.
- Solution: Investing in advanced equipment and monitoring systems to maintain optimal casting conditions.
- Initial Setup Cost: The initial investment in equipment and technology can be substantial.
- Solution: Conducting a thorough cost-benefit analysis and exploring financing options to manage initial costs.
Conclusion
The successful implementation of lost foam casting in heavy machinery manufacturing demonstrates its potential to enhance product quality, reduce material waste, and improve production efficiency. The case studies of ABC Heavy Machinery, DEF Mining Solutions, and GHI Agri-Industries illustrate the significant benefits and outcomes of adopting lost foam casting. By addressing the associated challenges and leveraging the advantages of this innovative casting method, manufacturers can achieve substantial improvements in their production processes and maintain a competitive edge in the industry.