In the process of casting, defects can occur due to a myriad of reasons. These defects not only affect the aesthetics of the product but also compromise its functionality, strength, and durability. Understanding the causes, identifying them early, and taking appropriate remedial measures can help ensure the casting process’s quality and efficiency. This article explores the common casting defects, their causes, identification, and preventive measures.
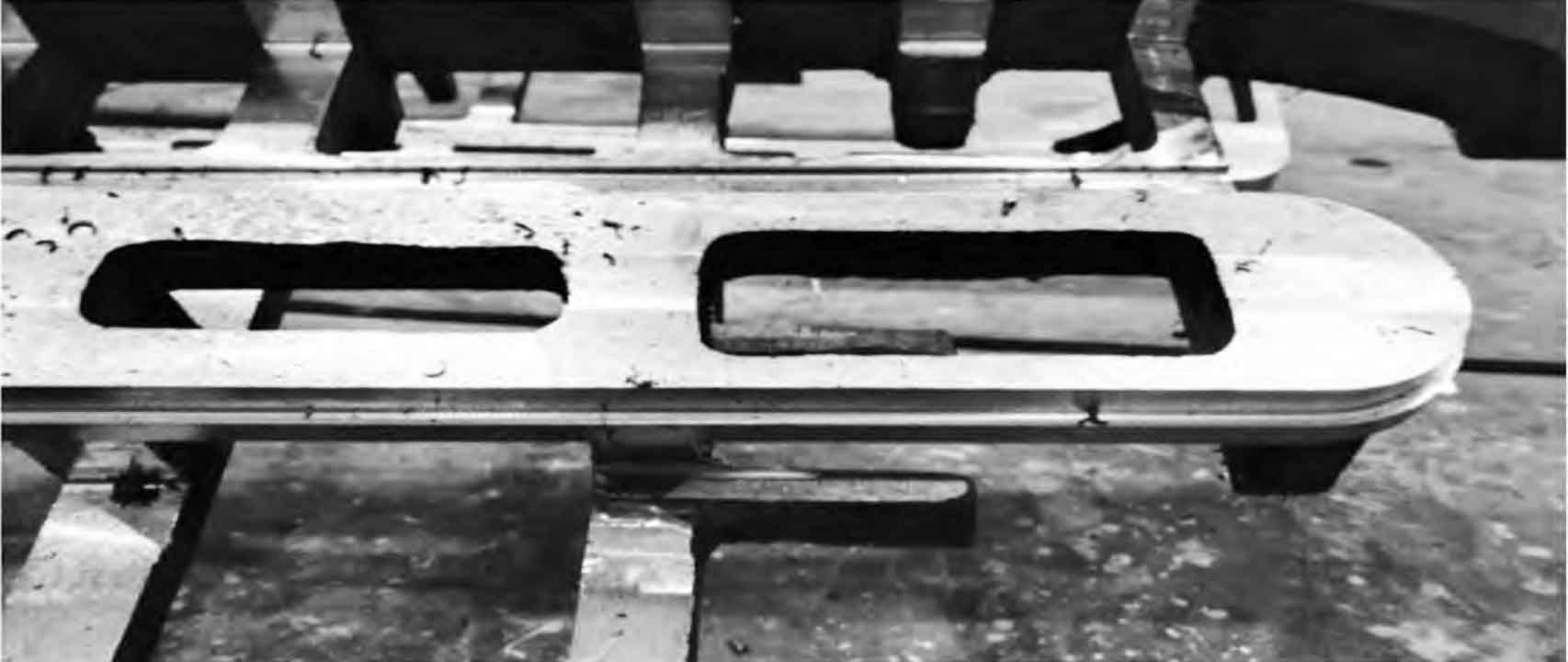
- Porosity: Caused by trapped gases or shrinkage during the cooling process, porosity leads to cavities or bubbles in the final casting. These defects can be identified using methods like ultrasonic testing or radiography. Remedial measures include ensuring proper degassing of molten metal, designing adequate venting in molds, and controlled cooling processes.
- Shrinkage Defects: These defects occur due to the contraction of metal during solidification, causing voids in the casting. Visual inspection and radiographic methods can help identify shrinkage defects. Using risers to supply additional molten metal and maintaining controlled cooling rates can prevent such defects.
- Hot Tears: Hot tears or hot cracks appear as irregular crevices with sharp edges. These are caused by thermal stress during solidification. Visual inspection or dye penetrant inspection can identify these defects. The preventive measure involves careful design of the casting, mold, and gating system to ensure uniform cooling and to minimize thermal stress.
- Cold Shuts: Cold shuts appear when two streams of liquid metal do not fuse properly, leaving a visible seam. Visual inspection can easily identify cold shuts. Maintaining the right pouring temperature and improving mold design to guide the flow of metal can prevent this defect.
- Misruns and Cold Shots: Misruns and cold shots are caused when the molten metal doesn’t fill the mold cavity completely before solidification. Visual inspection or radiography can identify these defects. Maintaining the appropriate pouring temperature and speed and designing an effective gating system can prevent this.
- Inclusions: Inclusions are foreign materials, such as sand or slag, trapped in the casting. Inclusions can be identified using methods like radiographic or ultrasonic inspection. Ensuring the cleanliness of the casting material, molds, and using filters can prevent these defects.
- Mold Material Defects: These defects, including cuts, washes, or scabs, can occur due to issues with mold material or preparation. Visual inspection can help identify these defects, and using appropriate mold materials and ensuring their proper preparation can help prevent such issues.
Casting defects can significantly affect the quality and reliability of the final product. By understanding their causes, accurately identifying them, and implementing appropriate preventive and corrective measures, manufacturers can improve the quality of their cast products and reduce costs associated with rework or scrap. Continuous monitoring and improvements in the casting process can further ensure the delivery of high-quality, defect-free products.