The Siemens motor shell lost foam casting produced by ZHY Casting using the lost foam process has an overall dimension of 1 240 mm × 800 mm × 700 mm, the mass of lost foam casting is about 780 kg, and the material grade is ASTM48A30C (equivalent to HT200~HT250). The size of the lost foam casting is large, there are many heat ribs, and the thinnest part is 5 mm. The structure of the lost foam casting is shown in Figure 1. Compared with the lost foam casting process of small motor shell, the forming of heat sink is more difficult and there are more problems.
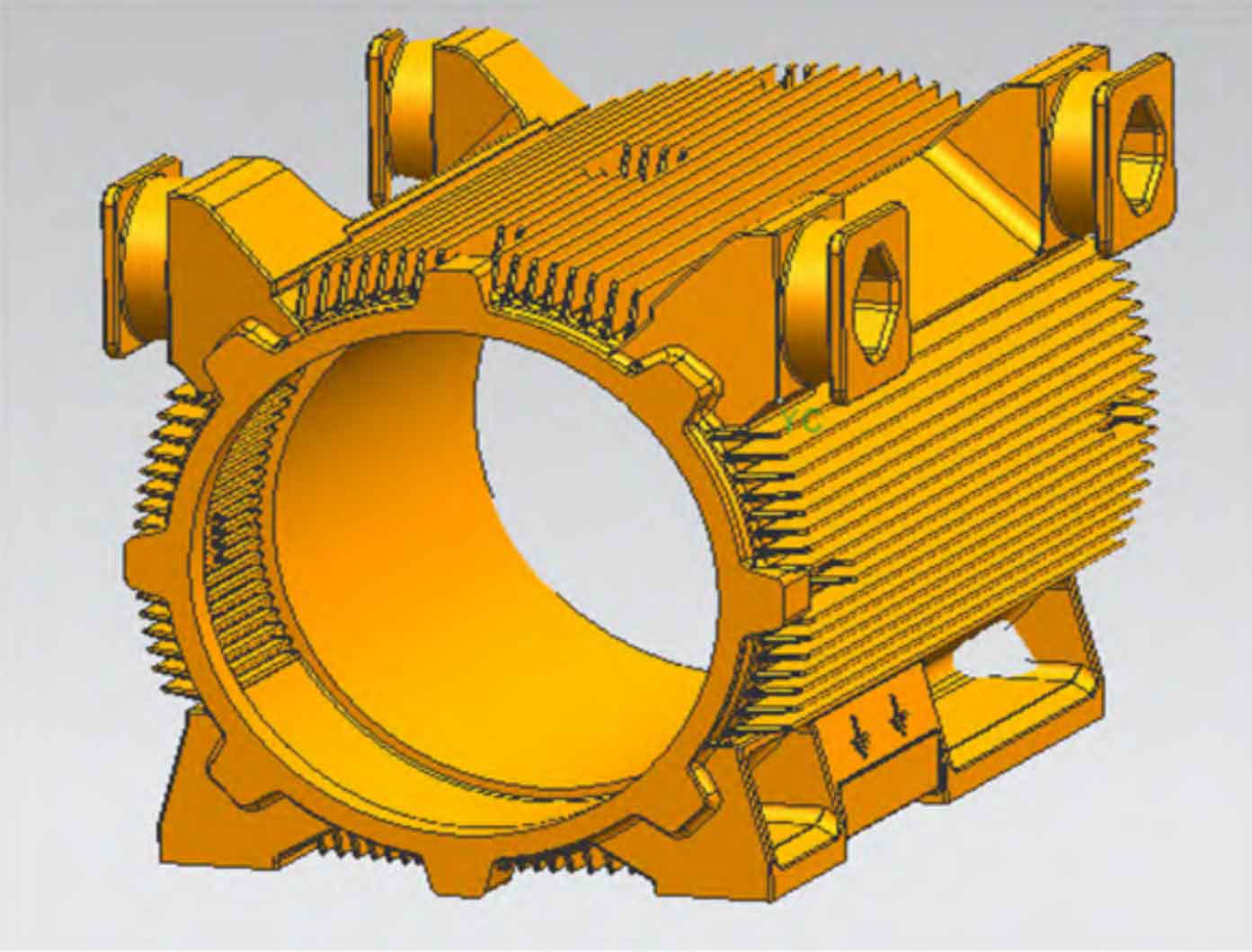
The medium and large motor shell mold with radiating ribs is generally divided into four parts, and the white film is combined after molding. However, the size of the combined white mold is difficult to control and its stability is poor. The mold of our company is integrally formed, and the shape and inner cavity adopt slider structure to ensure the smooth mold release of the whole white film, which fundamentally solves the problems of deformation and dimensional accuracy of the lost foam casting. The parameter selection of shrinkage rate is the key in mold design. The shrinkage rate of large lost foam casting is 1.35% in the length direction and 1.15% in the height direction.
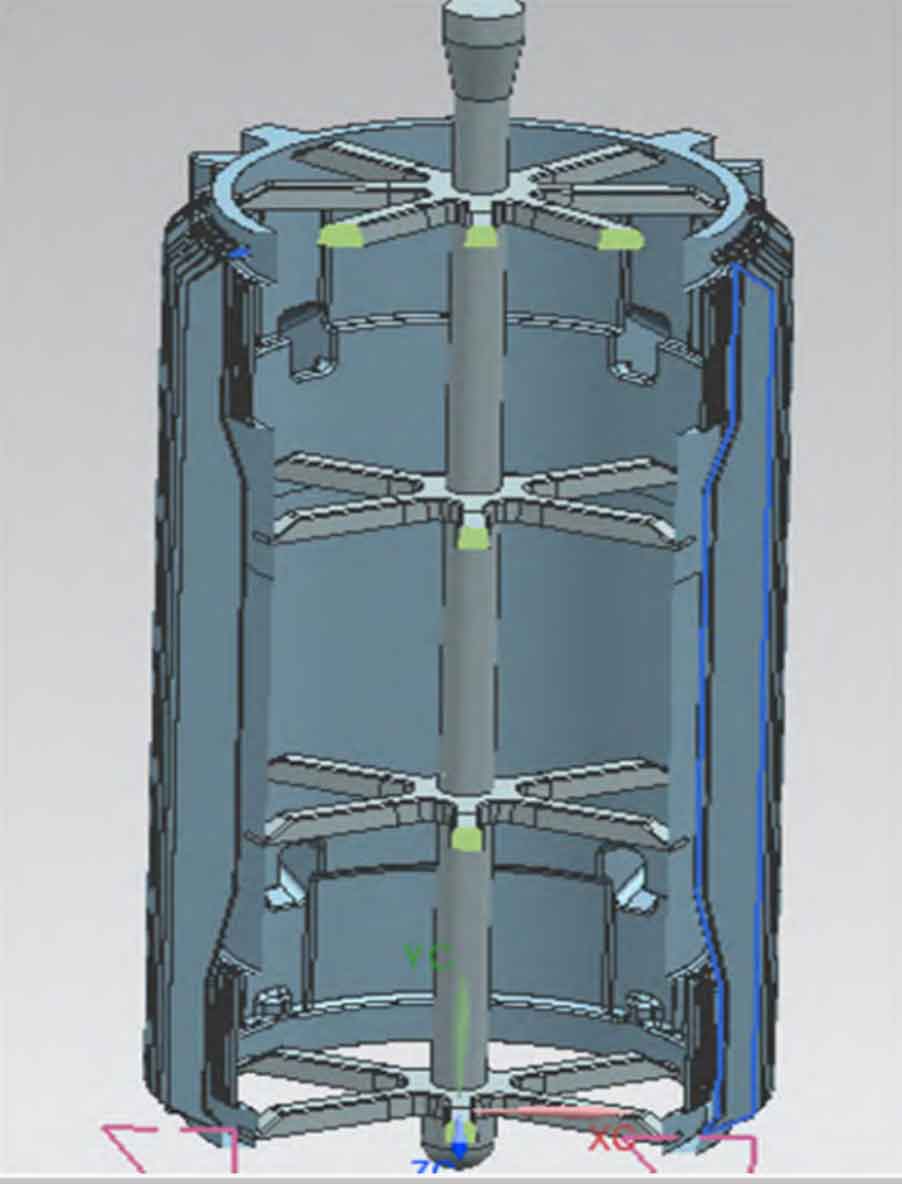
The form of the gating system of the lost foam casting is different from the traditional process. The size, size, shape and direction of the inner runner of the lost foam casting directly affect the vaporization of the pattern. If the size of the inner runner is calculated according to the traditional sand casting process, the molten iron capacity is small and the surrounding heat dissipation area is large, which will sharply reduce the temperature of the molten iron entering the mold cavity and affect the vaporization speed of the pattern. According to the calculation of traditional sand casting process, the total sprue sectional area is generally increased by 10%~25%, and adjusted appropriately after the test. Due to the high height of the lost foam casting, the design of the position of the inner runner of the lost foam casting is very important, as shown in Figure 2. The inner runner with multi-point molten iron injection is adopted. The gating system and parameters are designed as follows: the section size of the sprue is φ 48 mm, there are 4 layers of transverse sprue and inner sprue, and the height and diameter directions are uniformly arranged. There are 8 layers on the top layer, 6 layers on the other 3 layers, and a total of 26 layers. Because the vertical sprue is hollow, molten iron directly enters the lowest layer of the sprue. As the liquid iron level rises, it rises to the height of the second layer, and the second layer begins to enter molten iron. Therefore, according to the single-layer calculation, the pouring system proportion is Σ F straight: Σ F horizontal: Σ F inside=1.25:2.5:1.