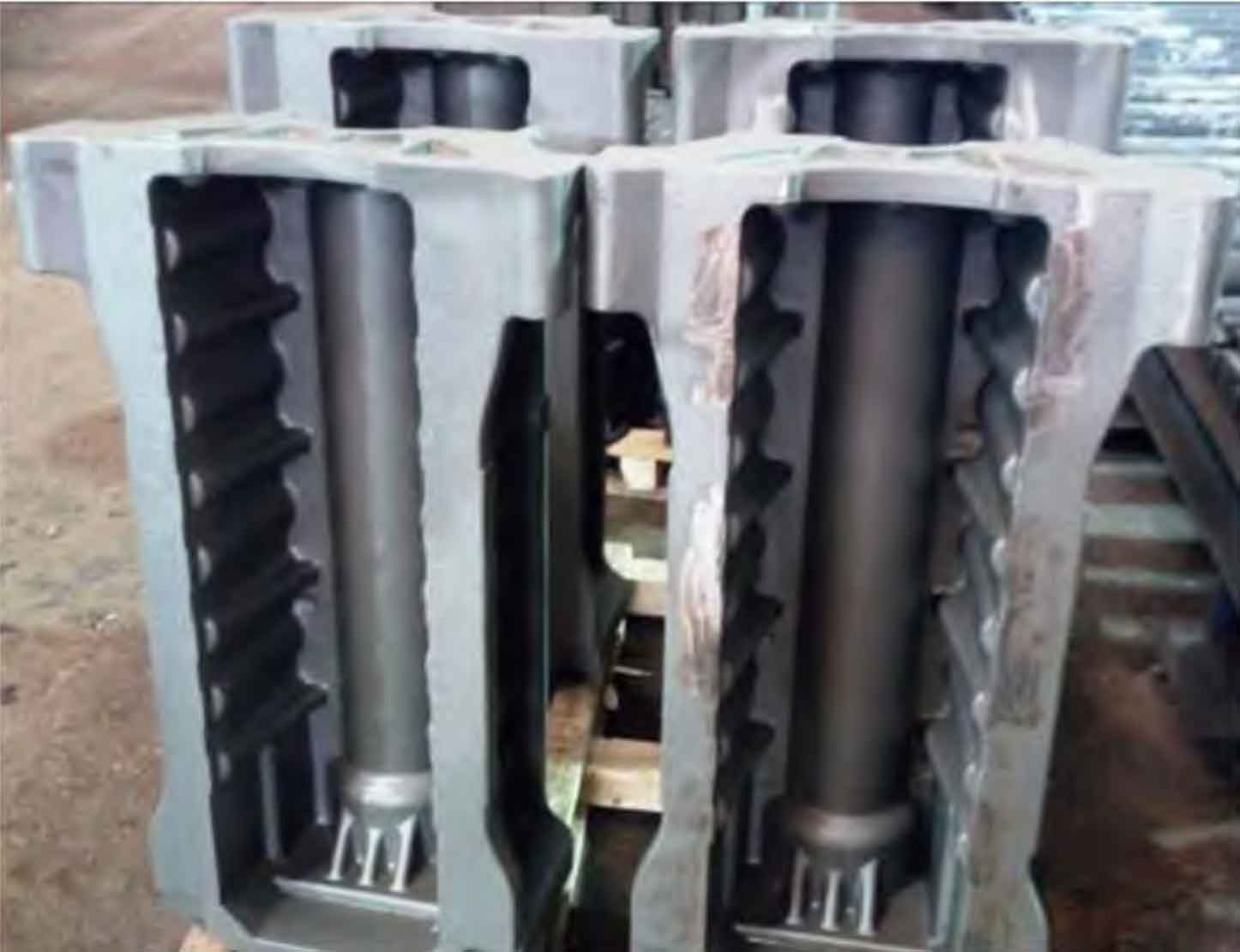
The trial production of A804T0-1009006 nodular cast iron oil pan castings by top-pouring and inclined pouring process was carried out. The appearance and dimension of the castings were good after sanding, and there were no cavity defects on the surface of the inner cavity, as shown in Figure 1. The sawing machine was used to dissect the large hot spot on the top of the ductile iron casting. No shrinkage and porosity defects were found on the dissecting surface, as shown in Figure 2. The surface was sent to the customer for processing. No shrinkage was found on the processing surface, which met the technical requirements.
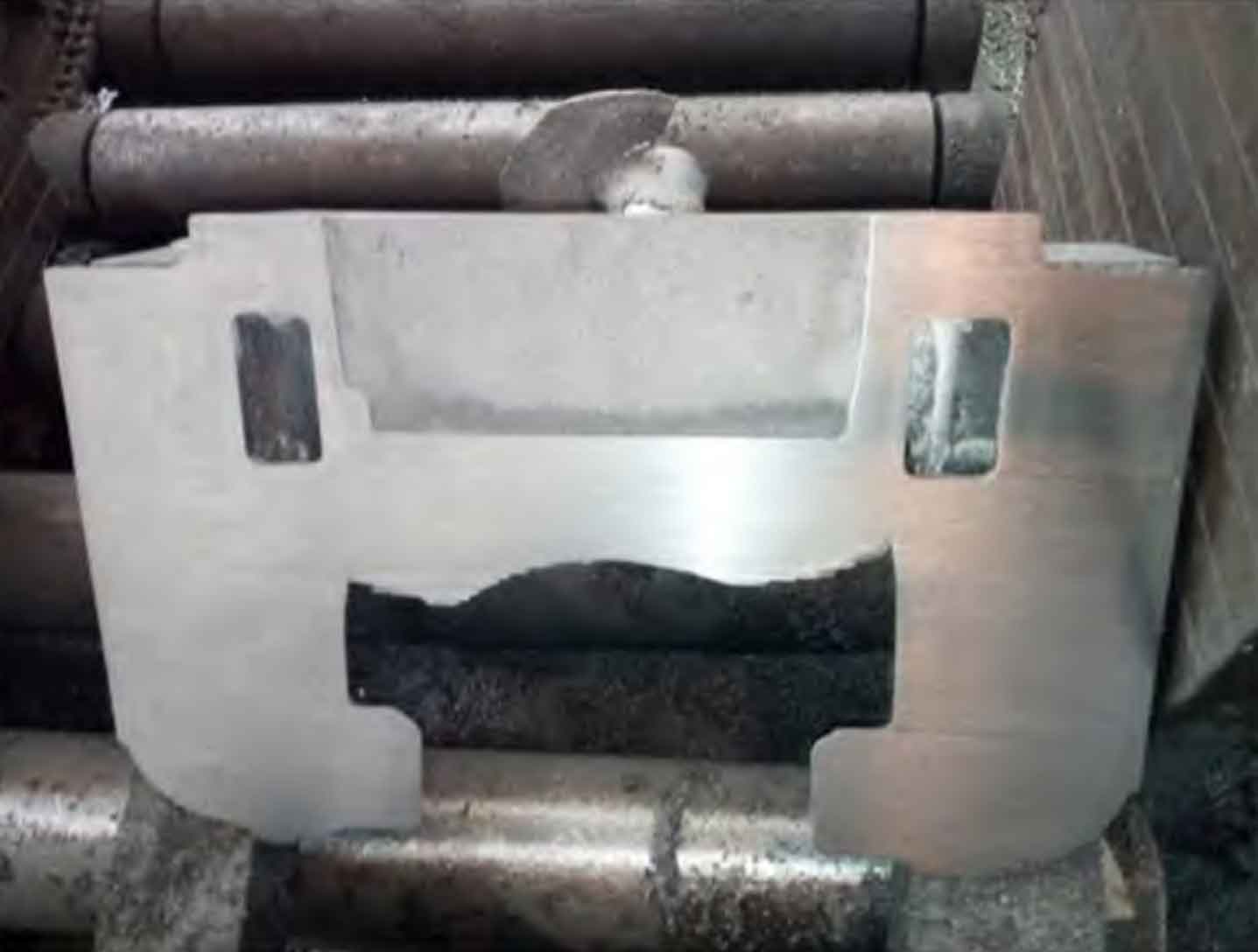
Carry out bulk sampling inspection on the top of the oil pan (as shown in Figure 3). The wall thickness of the sampling part is 45 mm. The results of the bulk metallographic structure inspection are: spheroidization grade 3, graphite size 6, pearlite volume fraction 15%, cementite volume fraction ≤ 1.0%, phosphorus eutectic volume fraction ≤ 0.5%. The mechanical property test results of the body show that the tensile strength is 494 MPa and the elongation is 12%.
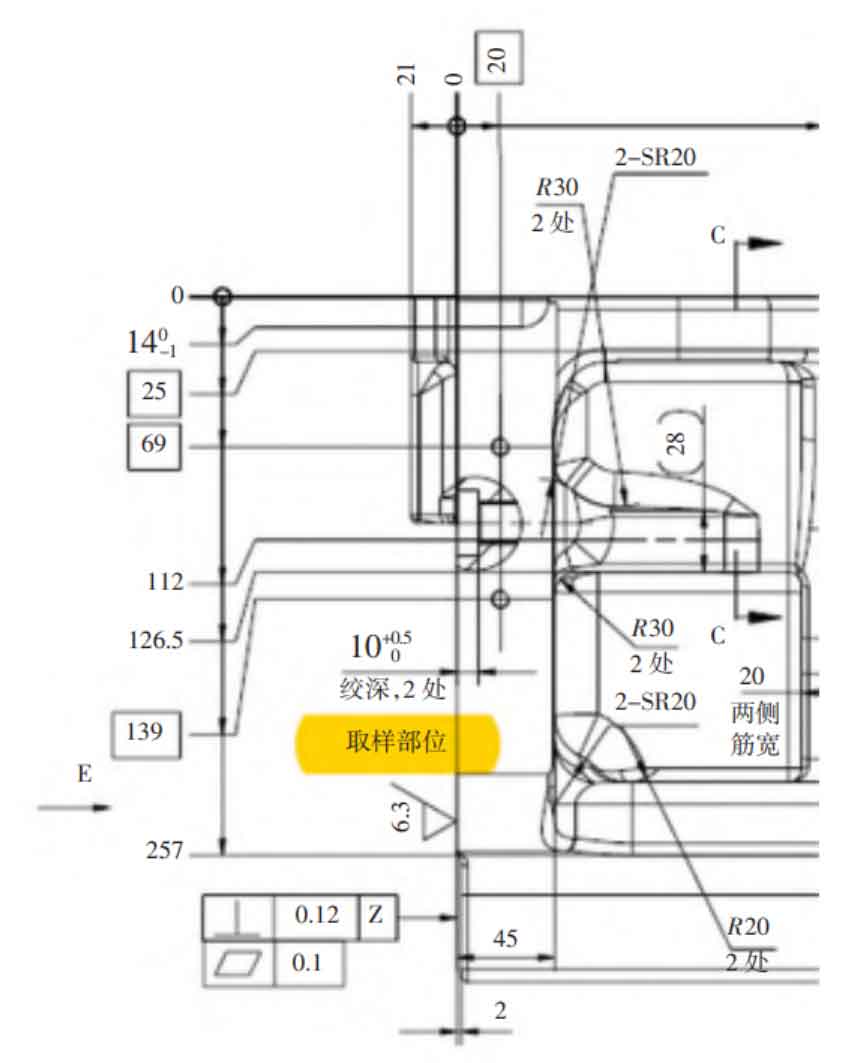
(1) It is feasible to produce large nodular cast iron oil pan by EPC process.
(2) The molten iron adopts the double-line process of covering and feeding wire spheroidization, which ensures the quality of molten iron feeding wire spheroidization, and achieves the material quality requirements of ductile iron castings.
(3) Using the top-pouring inclined pouring process, the smooth, orderly and sequential solidification of the mold filling process was achieved, and the graphite iron castings were compact without shrinkage and porosity, and the use of the graphite iron castings did not leak, meeting the use requirements.