The solidification process of ductile iron castings is generally a process of shrinkage, expansion and re shrinkage. Although the precipitation of graphite can bring volume expansion in the solidification process of ductile iron castings, due to its paste solidification mode (the precipitation of a large number of dendrites separates the liquid metal which has not yet solidified into many independent molten pools, making it impossible for the crystals to supplement each other), and the deformation, displacement and shrinkage defects of the mold wall caused by the expansion force of graphite, especially shrinkage porosity, are the most common in ductile iron castings See the defects.
The volume change and pressure loss during solidification are the direct causes of shrinkage porosity. Shrinkage porosity is divided into macro porosity and micro shrinkage porosity. Macro porosity is a group of small holes scattered in the casting, while the intergranular pores which are invisible to the naked eye are called micro shrinkage porosity. The main factors that affect the shrinkage porosity of castings are chemical composition, inoculation degree, component structure (modulus) and mold strength.
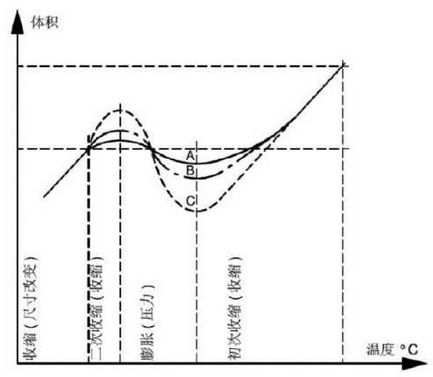
The following figure shows the volume change degree of a (gray cast iron), B (Confucian graphite cast iron) and C (ductile iron castings) in the solidification process with the decrease of temperature. It can be clearly seen that the volume change of nodular cast iron is greater than that of the other two materials in shrinkage and expansion stages. Therefore, how to control and eliminate the shrinkage cavity and porosity of ductile iron castings has always been a problem of concern to the foundry, and also a difficult problem in the production of ductile iron castings in the world.