As the core component of the engine, the cylinder liner has put forward higher requirements for various performances of the cylinder liner with the development of the engine technology in the direction of high speed, high power, high detonation pressure, low emissions, and high performance. In the working process of the engine, the inner wall of the cylinder liner, as the friction working surface of the reciprocating movement of the piston, needs to have high strength, high temperature resistance, friction resistance and other characteristics, so the reliability and life of the cylinder liner are crucial to the life of the engine. Ductile iron is widely used in main engine plants for its excellent mechanical properties and cavitation resistance. However, when our company produced the ductile iron cylinder liner through the horizontal centrifugal casting process of water-cooled metal mold, it was found that the white structure appeared at the wall thickness of the casting, which is called anti white casting.
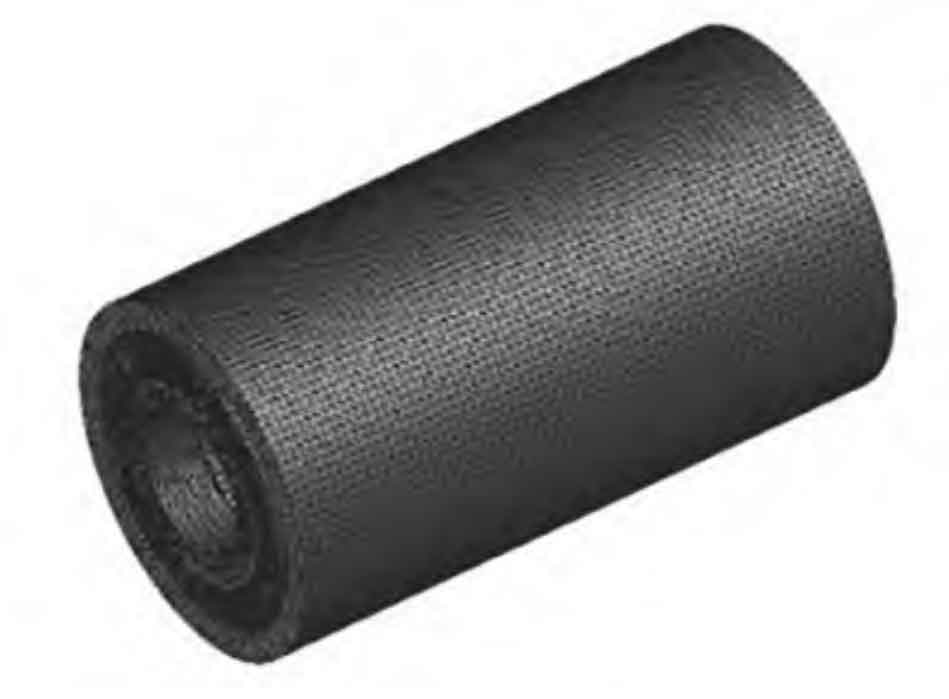
The anti white defect is a kind of defect hidden in the ductile iron casting. It will reduce the mechanical properties of the casting, increase the difficulty of machining the casting, reduce the tool life, and directly affect the quality and economic benefits of the casting. The formation of reverse chill is mainly related to the chemical composition segregation of ductile iron, the inoculation effect of molten iron and the cooling conditions of castings.
(1) The temperature field and solid-liquid phase distribution of the original casting process were analyzed by using the casting simulation software, and the position of the final solidification area of the casting was determined. The simulation results were consistent with the defect positions in the practical production, which proved the correctness of the simulation results and provided data support for the optimization and improvement of the centrifugal casting process.
(2) Combined with the simulation results, the cooling water flow and insulation coating thickness at the casting wall thickness position were adjusted to shorten the solidification time of the final solidification position, eliminate the influence of inoculation recession, reduce the depth of the final solidification area from the casting inner wall, eliminate the casting anti white mouth defects, improve the casting quality and machining performance, and verify the correctness of the optimization scheme through actual production.
(3) Through the simulation of centrifugal casting process, the solidification law of centrifugal casting is understood, which provides a theoretical basis for reducing the machining allowance of castings and improving the utilization rate of materials.
(4) The method introduced in this paper can provide guidance for the design and development of similar products, effectively reduce the process development cycle, reduce the cost of process improvement, and improve economic benefits.
With the development of computer numerical simulation technology, a new way to explore the filling process and solidification law of centrifugal casting has been provided for the process designers of centrifugal casting. Although the current casting simulation software for horizontal centrifugal casting process simulation is not yet mature, and there is still a certain gap with the actual production process, it has the advantages of short development cycle, low research cost, convenient adjustment of process parameters, etc., and plays an increasingly important role in guiding the actual production and process improvement process.
The solidification process of cylinder liner casting was simulated numerically. By studying the solidification law, temperature field, solid-liquid phase distribution and other problems of the cylinder liner casting after filling, the location of the anti white mouth defect of the cylinder liner casting was determined, providing data support for process optimization and improvement.