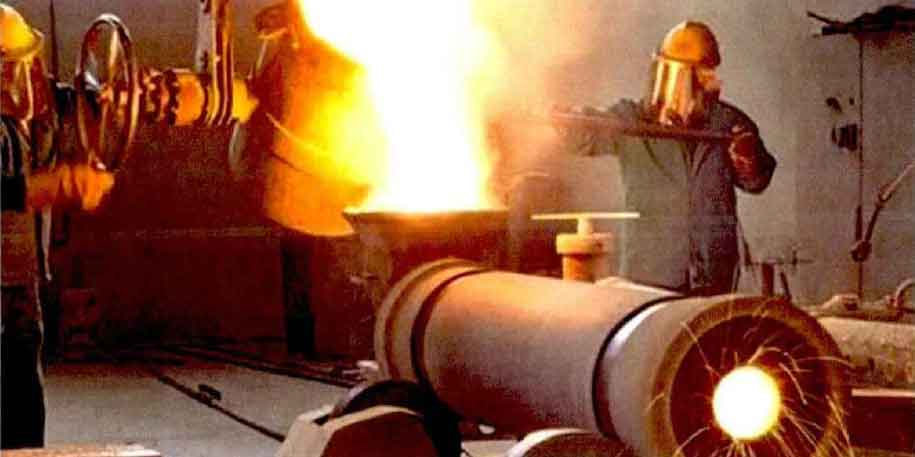
Rolls, seamless tubes and ring parts are the key basic components of high-end equipment such as nuclear power and thermal power, petrochemical industry and large rolling mills. They have the functions of bearing, connecting and driving. They have many varieties, large quantities and wide applications. This kind of component is usually produced by centrifugal casting technology. The liquid metal is poured into the high-speed rotating mold, and the liquid metal is finally formed by clinging to the mold wall under the action of centrifugal force. According to the angle between the axis of mold rotation and the horizontal direction, centrifugal casting can be divided into horizontal centrifugal casting and vertical centrifugal casting. Horizontal centrifugal casting rotates along the central axis of the mold itself without using the core. The inner surface of the casting is a free surface, which is commonly used in the production of long pipe castings; The center of the vertical centrifugal casting mold has a core and rotates around the central axis. It is mainly used for hollow disk parts with small height diameter ratio. Centrifugal casting will not cause metal loss due to gating system and riser, with high flow filling capacity, good casting compactness, few defects such as pores and slag inclusions, and excellent mechanical properties; Thin wall castings can be made by controlling the fluidity of liquid metal through centrifugal acceleration. However, centrifugal casting is prone to specific gravity segregation, which makes it difficult to produce special-shaped castings, and the inner diameter of hollow castings can not be accurately controlled, with rough inner surface and large machining allowance. Zherbtsov and others in Russia have used electromagnetic centrifugal casting technology to manufacture flange rings, and their mechanical properties can be further improved through appropriate heat treatment. Compared with sand casting thin-walled tube, the grain of large-diameter AZ61A magnesium alloy thin-walled tube formed by centrifugal casting is significantly refined, the micro segregation and composition fluctuation are significantly reduced, and the solid solubility and mechanical properties of alloy elements are significantly improved. In addition, wangxiaojia and others prepared AZ91 magnesium alloy castings by sand mold casting, metal mold casting and centrifugal casting respectively. The grain size, mechanical properties and element distribution uniformity of castings prepared by centrifugal casting are significantly better than those of sand mold casting and metal mold casting. Therefore, centrifugal casting technology has gradually replaced the traditional sand casting in the production of major equipment components such as wind power, petrochemical and large ships. It has the obvious advantages of simple process, good mold filling performance and high yield.
With the rapid development of deep space exploration, ocean shipping, wind power generation and other fields, the performance of centrifugal casting components needs to meet the service requirements of high-end equipment under extremely severe environmental conditions. Accordingly, different requirements are put forward for different working surfaces of components, such as the inner layer of composite components should be wear-resistant and corrosion-resistant, and the outer layer should have high strength and high toughness. It is often difficult for a single metal component to meet such performance requirements, because if materials with high strength and good wear resistance are used, the toughness of its outer surface will be reduced and cracks will easily occur; However, if materials with good toughness and low hardness are used, the working face cannot meet the requirements of wear resistance and corrosion resistance. It needs to be replaced frequently and the cost is high. For this reason, two kinds of metal materials with different physical, chemical and mechanical properties are combined to form a bimetallic component by a specific composite process (such as centrifugal casting technology). In this process, the metallurgical combination of atomic diffusion between the two materials is realized, so that the bimetallic component has excellent properties such as wear resistance, strength, toughness and corrosion resistance of the two materials, so as to improve the mechanical properties and service life of the component, It has gradually received the attention of many material researchers. Scholars at home and abroad have carried out a lot of research work on the centrifugal casting process and the control of microstructure and properties of bimetal composite components, and have achieved many useful results. In 1860, American scholars proposed to use hot rolling experiment to manufacture bimetallic composite plates. However, due to the limitations of equipment and test conditions, the hot rolling experiment only stayed at the conception stage. In the 1930s, Germany successfully developed the bimetallic centrifugal casting composite pipe, and then the University of Birmingham in England prepared the bimetallic composite plate by the solid-solid composite method. Chrysler Corporation of the United States adopts solid The graphite / bronze composite plate was prepared by the solid composite method, and the good bonding of the transition layer was achieved. At the end of the 20th century, American scholars put forward the “three-step” method for preparing bimetallic composite plates, namely “surface treatment rolling composite diffusion annealing”, which made a breakthrough in the bimetallic solid-solid composite process. Japanese researchers used the “ladle rolling method” to produce stainless steel / aluminum alloy composite plates for large ships. Domestic research on bimetallic composite components started late, and its preparation technology mainly focused on the explosion method and rolling method. Then, a series of composite rollers and composite pipes were gradually produced by centrifugal casting process. The composite interface is metallurgical bonding of atomic diffusion. Compared with the hot rolling composite method, the interface bonding effect is better. In addition, the pouring process, bonding layer quality The research on composition distribution and heat treatment has also achieved fruitful results.
Based on the research of many scholars at home and abroad, the research status of centrifugal casting technology for bimetallic composite components is summarized, the characteristics and mechanical properties of the inner and outer layers of composite components are analyzed, and the bonding interface morphology and bonding points are emphatically explained; Taking bimetallic composite roll and composite pipe as examples, the forming law of centrifugal casting and the influence of process parameters on the mechanical properties of component interface were analyzed, the mechanism of composite forming and microstructure evolution of centrifugal casting were revealed, and the problems existing in the centrifugal casting of bimetallic components were discussed. Combined with the short process manufacturing technology of ring parts, the development trend and key research contents of bimetal centrifugal casting composite rings are prospected, in order to provide a theoretical basis for the high-performance and lightweight manufacturing of centrifugal casting composite components.
Single metal components are more and more difficult to meet the service performance requirements in extremely harsh environments in terms of performance, while bimetal composite components can have the advantages of two single metal materials to realize their complementary performance. As key connecting, bearing and rotating structural components, bimetal composite components are widely used in aerospace, wind power, petrochemical industry, deep-sea ships and other major equipment fields. However, due to the differences in composition, structure and performance, the composite interface morphology and bonding characteristics determine the key to the manufacture of such components. After years of research and development, the centrifugal casting technology for bimetal composite components such as composite roll and composite seamless pipe has been realized. The bimetallic composite roll is made of horizontal centrifugal casting for the outer layer and gravity filling casting for the inner layer. Both the inner and outer layers of the bimetallic composite pipe are made of typical horizontal centrifugal casting, that is, the inner layer is poured at a certain interval after the outer layer is poured. In this paper, the interface bonding criteria of composite roll and composite pipe are given from the aspects of centrifugal casting process, bonding interface and bonding performance. Combined with the influence of outer pouring temperature, inner and outer pouring interval and mold speed on the interface morphology, it is determined that the main factors affecting the thickness of bonding layer are pouring temperature and solidification method. The performance of composite components mainly depends on the performance of the bonding interface. During the centrifugal casting of composite roll and composite pipe, the morphology and composition distribution uniformity of the bonding interface can be improved by adding electromagnetic control and multi-element alloy modification treatment, as well as step heat treatment after centrifugal casting, so as to improve its bonding performance. It is revealed that the composite forming mechanism of bimetal components in centrifugal casting is mainly metallurgical bonding. Based on the characteristics of disc-shaped ring-shaped parts, the research and development direction of centrifugal casting technology for bimetal composite components is expanded, that is, the bimetal ring-shaped billets with different components in the inner and outer layers are made by the vertical centrifugal casting process, and the geometric dimension accuracy control, microstructure improvement and performance improvement of the ring-shaped billets are realized during the centrifugal casting process, It can solve the problems of interface warpage, bending, large cracking tendency, poor contact quality and low bonding strength caused by traditional single ring fitting after centrifugal casting, improve the basic theory of bimetallic composite component centrifugal casting technology, and provide a theoretical basis for the short process “shape” / “property” integrated manufacturing of stainless steel / low carbon steel, aluminum / steel and aluminum / magnesium bimetallic composite rings.