The global casting products manufacturers are critical component of many key sectors, including automotive, aerospace, construction, and energy. Despite its significance, the industry faces numerous challenges while also being presented with significant opportunities for growth and innovation. This article explores these challenges and opportunities in detail, providing insights into the future landscape of casting products manufacturers.
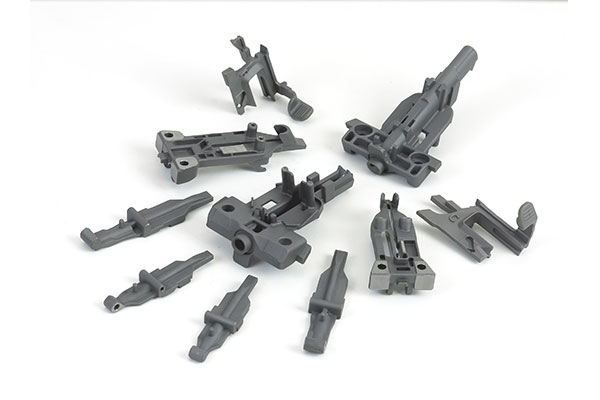
Introduction
Casting products manufacturers involves creating complex metal components by pouring molten metal into molds. This process is essential for producing parts that require precise dimensions and complex geometries. As global demand for high-quality cast components grows, manufacturers must navigate various challenges while capitalizing on emerging opportunities to stay competitive.
Challenges in the Global Casting Products Manufacturers
- Supply Chain Disruptions:
- Raw Material Shortages: The availability of raw materials such as aluminum, steel, and specialty alloys can be unpredictable, affecting production schedules and costs.
- Logistics Issues: Global supply chain disruptions, often caused by geopolitical tensions or natural disasters, can delay the transportation of materials and finished products.
- Rising Costs:
- Energy Costs: The energy-intensive nature of casting processes means that fluctuations in energy prices can significantly impact production costs.
- Labor Costs: Skilled labor is essential for maintaining high standards in casting production, and labor shortages or increasing wages can raise operational costs.
- Environmental Regulations:
- Emissions and Waste Management: Stricter environmental regulations require manufacturers to invest in cleaner technologies and waste management practices, increasing operational costs.
- Sustainability Compliance: Meeting sustainability goals and certifications requires ongoing investment in eco-friendly processes and materials.
- Technological Advancements:
- Integration of New Technologies: The rapid pace of technological advancements requires continuous investment in new equipment and training for the workforce.
- Cybersecurity Risks: As casting products manufacturers adopt more digital and automated processes, the risk of cyber-attacks and data breaches increases.
- Market Competition:
- Global Competition: Manufacturers face intense competition from both established players and new entrants, particularly from regions with lower production costs.
- Product Differentiation: Differentiating products in a crowded market is challenging, requiring innovation and unique selling propositions.
Opportunities in the Global Casting Products Manufacturing Industry
- Technological Innovations:
- Additive Manufacturing: The integration of 3D printing and additive manufacturing technologies allows for more complex designs and faster prototyping, reducing time-to-market.
- Automation and AI: Implementing automation and artificial intelligence in production processes can improve efficiency, reduce errors, and lower labor costs.
- Sustainability Initiatives:
- Recycling and Waste Reduction: Investing in recycling processes and waste reduction strategies can lower material costs and enhance sustainability credentials.
- Energy-Efficient Technologies: Adopting energy-efficient technologies and renewable energy sources can reduce operational costs and environmental impact.
- Expanding Markets:
- Emerging Economies: Expanding into emerging markets with growing industrial sectors offers new revenue streams and growth opportunities.
- New Applications: The development of new applications for cast components in sectors such as renewable energy and electric vehicles can drive demand.
- Collaborative Partnerships:
- Industry Collaborations: Forming partnerships with other companies, research institutions, and technology providers can drive innovation and share costs.
- Customer Engagement: Working closely with customers to develop customized solutions can enhance customer loyalty and create new business opportunities.
- Regulatory Compliance:
- Proactive Compliance Strategies: Investing in technologies and processes that exceed regulatory requirements can provide a competitive advantage and reduce the risk of fines or sanctions.
- Sustainability Certifications: Obtaining sustainability certifications can enhance brand reputation and attract environmentally conscious customers.
Table: Comparison of Challenges and Opportunities
Aspect | Challenges | Opportunities |
---|---|---|
Supply Chain | Raw material shortages, logistics issues | Developing local supply chains, using recycled materials |
Costs | Rising energy and labor costs | Investing in energy-efficient and automated processes |
Environmental | Stricter regulations, sustainability compliance | Innovating with eco-friendly technologies and practices |
Technological | Integration and cybersecurity risks | Leveraging additive manufacturing and AI |
Market | Global competition, product differentiation | Expanding into emerging markets, new applications |
Collaborative | Maintaining competitive edge | Forming partnerships and engaging customers |
Regulatory | Compliance costs | Proactive strategies and certifications |
Case Studies of Leading Manufacturers
- Company A: Embracing Additive Manufacturing:
- Innovation in Design: Company A has invested heavily in 3D printing technologies to produce complex, lightweight components for the aerospace industry. This has not only reduced production times but also opened new markets.
- Sustainability Efforts: The company uses recycled materials in its casting products manufacturers and has implemented a closed-loop recycling system to minimize waste.
- Company B: Automation and AI Integration:
- Efficiency Gains: By integrating AI and robotics into their production lines, Company B has achieved significant reductions in labor costs and error rates. The use of real-time data analytics has improved decision-making and process optimization.
- Energy Management: The company has installed energy-efficient furnaces and utilizes renewable energy sources, significantly cutting down on energy expenses.
- Company C: Expanding into Emerging Markets:
- Market Penetration: Company C has successfully expanded its operations into emerging markets in Asia and Africa, tapping into the growing demand for industrial and automotive components.
- Local Partnerships: By forming strategic partnerships with local firms, the company has navigated regulatory challenges and established a strong market presence.
Future Trends
- Smart Manufacturing:
- IoT and Digital Twins: The use of IoT and digital twins will enhance process monitoring and predictive maintenance, improving efficiency and reducing downtime.
- AI and Machine Learning: These technologies will drive further automation, optimize supply chains, and enhance product quality through predictive analytics.
- Sustainability and Circular Economy:
- Zero Waste Initiatives: Manufacturers will increasingly adopt zero waste initiatives, focusing on recycling and reusing materials to create a circular economy.
- Green Manufacturing: Continued advancements in green manufacturing technologies will reduce the environmental footprint of casting operations.
- Customization and Flexibility:
- Personalized Manufacturing: Advances in manufacturing technologies will enable mass customization, allowing manufacturers to meet specific customer requirements efficiently.
- Flexible Production Systems: Flexible production systems will allow for quick reconfiguration of production lines to accommodate different products and volumes, enhancing responsiveness to market demands.
Conclusion
The global casting products manufacturers at a crossroads, facing significant challenges but also immense opportunities. By embracing technological innovations, adopting sustainable practices, expanding into new markets, and forming strategic partnerships, manufacturers can navigate these challenges and capitalize on emerging opportunities. The future of the industry will be shaped by smart manufacturing, sustainability, and customization, driving continued growth and innovation in casting products manufacturers.