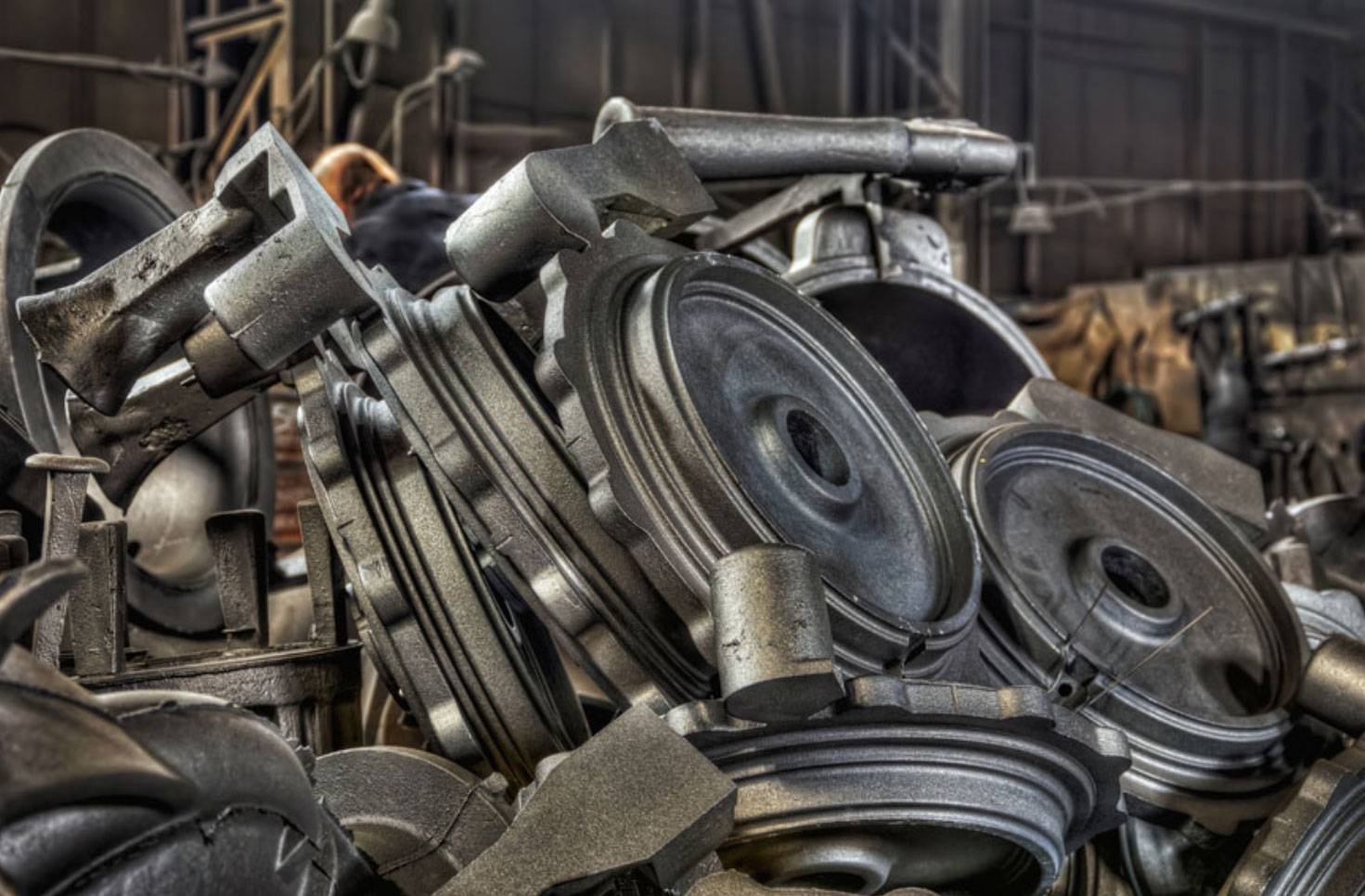
The ductile iron casting process plays a significant role in the automotive industry due to its combination of strength, ductility, and cost-effectiveness. Here’s an insight into its applications and emerging trends in this sector:
Applications in the Automotive Industry
- Engine Components: Ductile iron is used for manufacturing various engine parts such as cylinder heads, engine blocks, and crankshafts. Its strength and fatigue resistance make it ideal for these high-stress components.
- Suspension Systems: Components like control arms, kingpins, and knuckles are often made from ductile iron. Its ability to absorb shock and stress makes it a preferred material for suspension systems.
- Drive Train Components: Ductile iron is used for drive train parts, including gears, differentials, and drive shafts, due to its toughness and wear resistance.
- Braking Systems: Brake calipers, rotors, and drums are commonly made from ductile iron. Its heat dissipation properties and strength are crucial for the safety and efficiency of braking systems.
- Steering Systems: Steering gears and other related components benefit from the ductile iron’s strength and machinability.
Trends in the Automotive Industry
- Lightweighting: With the increasing focus on fuel efficiency and emission reduction, the automotive industry is trending towards lightweight materials. Ductile iron is being optimized in terms of design and alloy composition to reduce weight while maintaining strength.
- High-Performance Alloys: Development of high-performance ductile iron alloys with enhanced mechanical properties for more demanding applications, such as high-speed vehicles and electric cars.
- Improved Casting Techniques: Advancements in casting technology, including computer-aided design and simulations, are enabling the production of more complex and precise components.
- Integration with Additive Manufacturing: Combining traditional casting methods with additive manufacturing (3D printing) to create prototypes and parts with complex geometries.
- Sustainability Focus: Efforts are being made to make the casting process more environmentally friendly, including recycling initiatives and reducing energy consumption.
- Advanced Heat Treatments: Implementing sophisticated heat treatment processes to improve the mechanical properties of ductile iron parts, catering to the high-performance requirements of modern automobiles.
- Quality Control Enhancements: Utilizing advanced non-destructive testing methods to ensure high-quality castings with no internal defects, which is critical for safety-related automotive components.
- Electrification of Vehicles: As the industry shifts towards electric vehicles (EVs), ductile iron is finding new applications in EV components, adapting to the changing dynamics of vehicle design and function.
Conclusion
In the automotive industry, ductile iron continues to be a material of choice due to its excellent mechanical properties, versatility, and cost-effectiveness. Ongoing innovations in material science and casting processes are further enhancing its applications and meeting the evolving demands of the automotive sector. As environmental and efficiency standards become more stringent, the role of ductile iron in automotive manufacturing is likely to adapt and grow.