Quality control in ductile iron casting process is critical to ensure that each cast component meets the required standards and specifications. The process involves several steps, each of which must be carefully monitored and controlled:
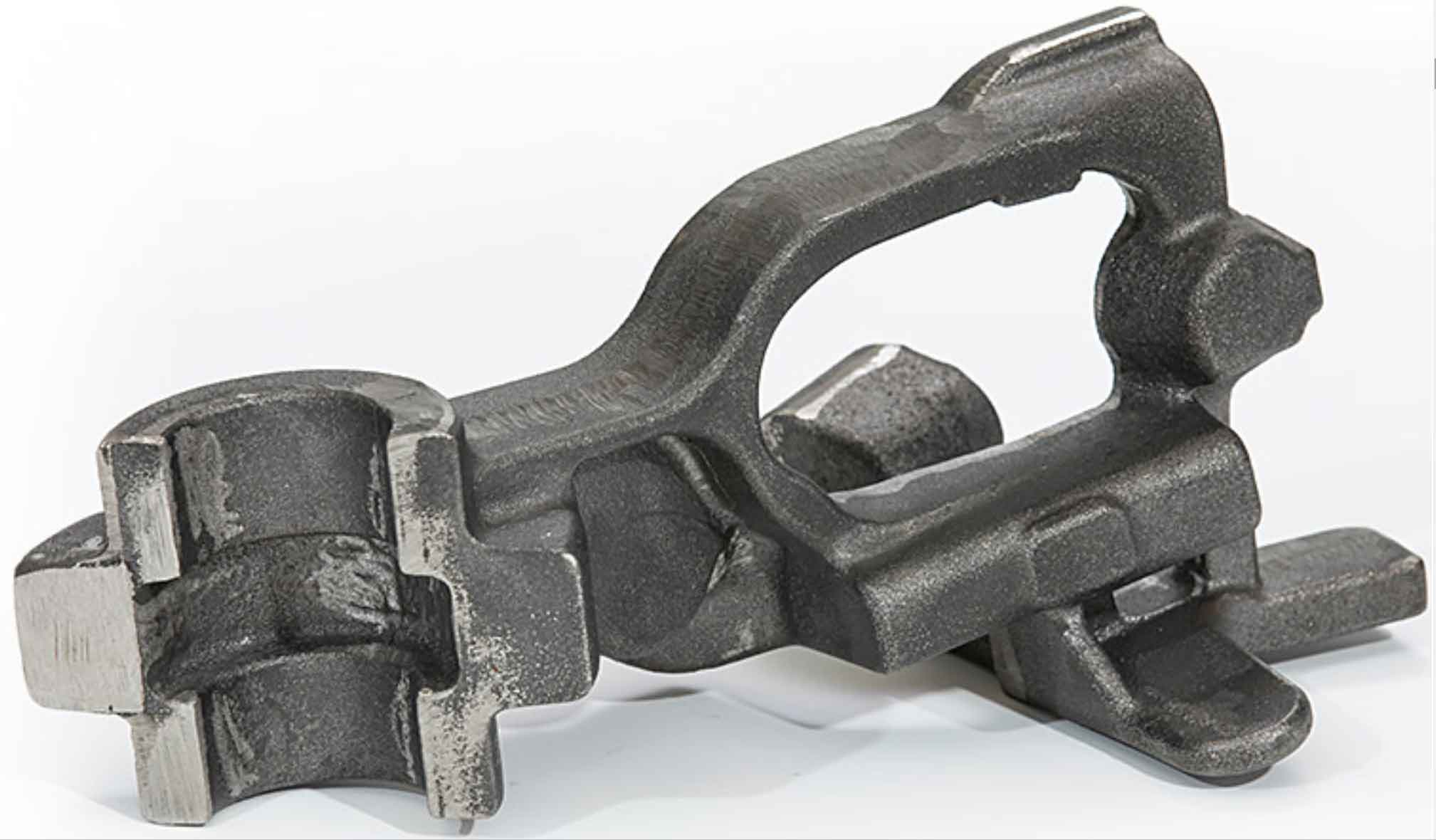
- Raw Material Inspection: The quality control process begins with the inspection of raw materials. The iron and alloying materials should meet specific chemical compositions to ensure the desired properties in the final product. Suppliers’ materials are often accompanied by certificates, but additional testing such as spectrometry can be used for verification.
- Melting and Alloying Control: During melting, the temperature and composition are critical. Controlled melting ensures that the metal reaches the appropriate temperature and composition. Regular checks are made using thermal analysis to maintain the desired carbon and silicon levels, crucial for ductile iron.
- Mold Quality Assurance: The quality of the mold directly affects the quality of the cast part. Inspections for mold dimensions, materials, and the sand’s properties (like moisture content and compactness) are essential to avoid casting defects.
- Pouring Process Monitoring: The pouring temperature and rate must be controlled to prevent common defects such as cold shuts and misruns. Techniques like thermal imaging can be employed to monitor this phase accurately.
- Solidification and Cooling Control: The cooling rate can impact the microstructure and, consequently, the mechanical properties of the cast iron. Controlled cooling processes are used to achieve the desired microstructure, like pearlite or ferrite, depending on the application.
- Post-Casting Inspection and Testing: After ductile iron casting process, each part is inspected for surface defects and dimensional accuracy. Non-destructive testing methods, such as ultrasonic testing, magnetic particle inspection, and radiographic testing, can be used to detect internal defects.
- Mechanical Property Verification: Samples from batches are often tested for mechanical properties like tensile strength, yield strength, elongation, and hardness to ensure they meet the required specifications.
- Heat Treatment (if applicable): If the ductile iron undergoes heat treatment to achieve certain mechanical properties, this process also needs strict quality control. Parameters like temperature, holding time, and cooling rate are crucial.
- Final Quality Check: Before dispatch, a final quality check is done to ensure that all the parts meet the customer’s specifications. This may include checking the surface finish, dimensional accuracy, and ensuring that there are no visible defects.
- Documentation and Traceability: Keeping detailed records of every step in ductile iron casting process is essential for traceability. It aids in identifying and rectifying issues if they arise and in continuous process improvement.
Quality control in ductile iron casting process is not just about testing and inspections; it’s also about continuous process improvement. Regular audits of the process, training of personnel, and investments in technology all play a vital role in maintaining high-quality standards in ductile iron casting process.