Sand casting is a traditional and widely-used method for producing metal components, known for its versatility and cost-effectiveness. However, sand casting manufacturers face numerous challenges that can impact the quality, efficiency, and profitability of their operations. This article explores the various challenges faced by sand casting manufacturers and discusses potential solutions to address these issues.
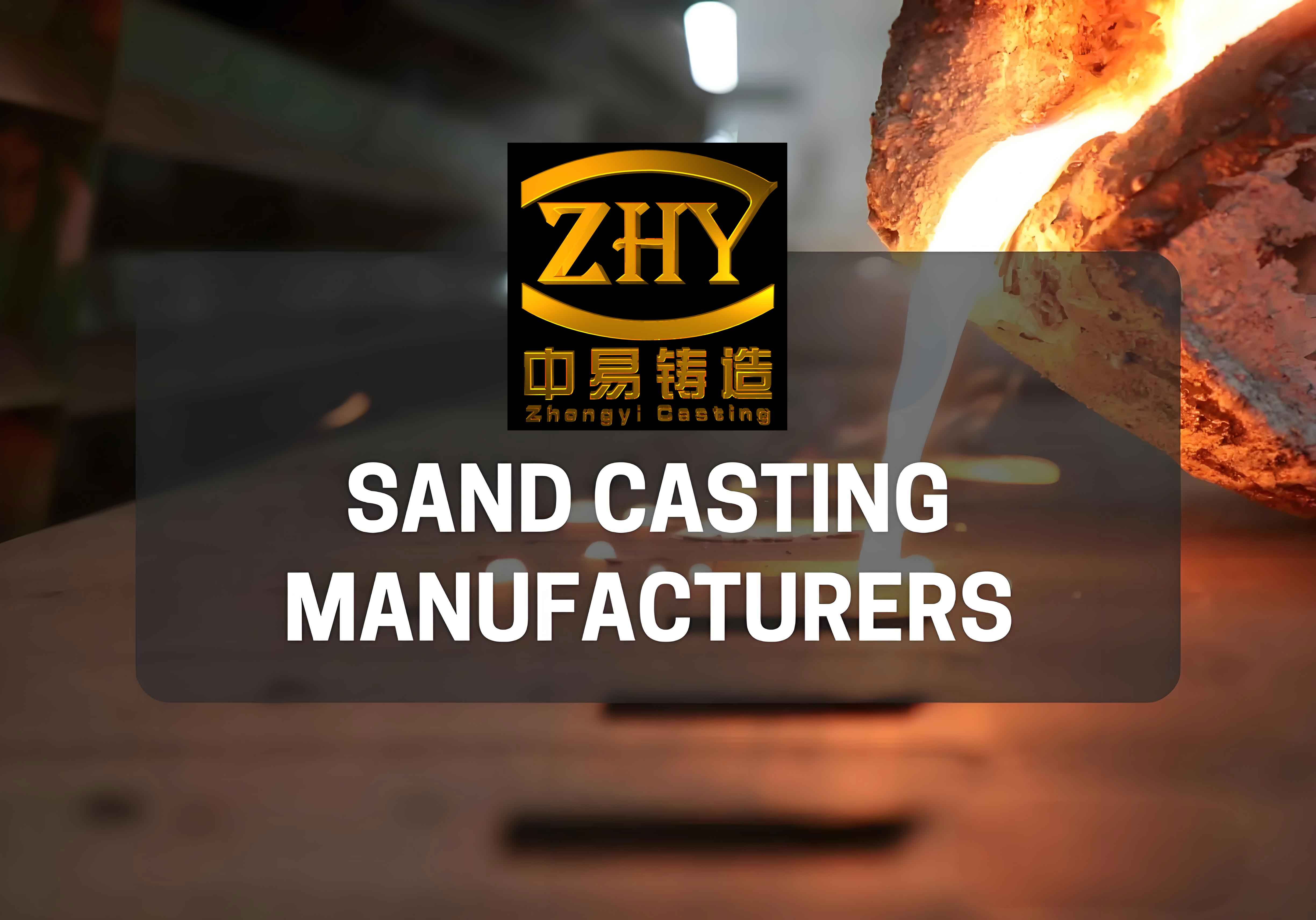
Key Challenges Faced by Sand Casting Manufacturers
1. Quality Control
Ensuring consistent quality is a major challenge for sand casting manufacturers. Variations in the sand casting process can lead to defects, affecting the integrity and performance of the final product.
Common Quality Issues
- Porosity: Small voids or cavities within the casting caused by trapped gases.
- Inclusions: Foreign particles such as sand, slag, or oxides embedded in the casting.
- Shrinkage Defects: Voids caused by the reduction in volume as the metal solidifies.
- Surface Finish: Achieving a smooth and defect-free surface can be difficult.
Solutions for Quality Control
- Improved Materials: Use high-quality sand, binders, and alloys to reduce defects.
- Process Optimization: Implement precise control over pouring temperature, pouring rate, and cooling rate.
- Inspection Techniques: Utilize advanced non-destructive testing methods such as X-ray and ultrasonic testing.
Table 1: Common Quality Issues and Solutions
Quality Issue | Description | Solutions |
---|---|---|
Porosity | Small voids caused by trapped gases | Use degassing techniques and improve mold venting |
Inclusions | Foreign particles embedded in the casting | Ensure clean materials and proper mold handling |
Shrinkage Defects | Voids due to volume reduction during solidification | Design effective risers and ensure adequate feeding |
Surface Finish | Rough or defective surface | Use finer sand, additives, and coatings |
2. Production Efficiency
Achieving high production efficiency is crucial for sand casting manufacturers to remain competitive. However, various factors can hinder efficiency.
Efficiency Challenges
- Cycle Time: Long cycle times can reduce overall production rates.
- Energy Consumption: High energy usage in melting and maintaining optimal temperatures.
- Waste Management: Managing and recycling sand and other waste materials.
Solutions for Production Efficiency
- Automation: Implement automation in mold making, pouring, and handling to reduce cycle times.
- Energy Optimization: Use energy-efficient furnaces and maintain precise temperature control.
- Waste Reduction: Develop effective sand reclamation and recycling processes.
List 1: Strategies for Improving Production Efficiency
- Implement automation in key processes.
- Use energy-efficient equipment.
- Develop sand reclamation and recycling methods.
3. Environmental Compliance
Sand casting manufacturers must comply with environmental regulations, which can be stringent and complex.
Environmental Challenges
- Emissions: Managing emissions from furnaces and other processes.
- Waste Management: Proper disposal and recycling of sand and other waste materials.
- Resource Consumption: Efficient use of raw materials and energy.
Solutions for Environmental Compliance
- Emission Control: Install advanced emission control systems to capture and reduce pollutants.
- Sustainable Practices: Implement sustainable practices such as using recycled materials and reducing waste.
- Regulatory Compliance: Stay informed about and comply with local, national, and international environmental regulations.
Table 2: Environmental Challenges and Solutions
Environmental Challenge | Description | Solutions |
---|---|---|
Emissions | Pollutants released during melting and casting | Install emission control systems |
Waste Management | Disposal and recycling of sand and other materials | Develop effective waste management practices |
Resource Consumption | Efficient use of raw materials and energy | Implement sustainable practices and recycling |
4. Skilled Labor Shortage
The shortage of skilled labor is a significant challenge for sand casting manufacturers. Experienced personnel are crucial for maintaining quality and efficiency.
Labor Challenges
- Training and Retention: Difficulty in training new employees and retaining experienced workers.
- Knowledge Transfer: Ensuring that critical knowledge and skills are transferred to new employees.
- Workforce Aging: An aging workforce leading to potential knowledge gaps as experienced workers retire.
Solutions for Skilled Labor Shortage
- Training Programs: Develop comprehensive training programs to upskill new employees.
- Incentives: Offer competitive salaries, benefits, and career advancement opportunities to retain skilled workers.
- Knowledge Management: Implement knowledge management systems to capture and transfer critical skills and knowledge.
List 2: Addressing Skilled Labor Shortage
- Develop robust training programs.
- Provide competitive compensation and career growth opportunities.
- Implement knowledge management systems.
5. Technological Advancements
Keeping up with technological advancements is essential for sand casting manufacturers to remain competitive. However, integrating new technologies can be challenging.
Technological Challenges
- Integration: Difficulty in integrating new technologies with existing processes.
- Cost: High initial investment costs for advanced equipment and software.
- Adaptation: Training employees to adapt to and effectively use new technologies.
Solutions for Technological Advancements
- Incremental Implementation: Introduce new technologies gradually to minimize disruption.
- Investment Planning: Plan investments strategically to balance cost and benefits.
- Employee Training: Provide comprehensive training to ensure employees can effectively use new technologies.
Table 3: Technological Challenges and Solutions
Technological Challenge | Description | Solutions |
---|---|---|
Integration | Difficulty in integrating new technologies | Gradual implementation and phased integration |
Cost | High initial investment costs | Strategic investment planning |
Adaptation | Training employees to use new technologies | Comprehensive training programs |
Case Study: Overcoming Challenges in a Sand Casting Manufacturer
A sand casting manufacturer faced multiple challenges, including quality control, production efficiency, and environmental compliance. The following table outlines the steps taken to address these challenges and the results achieved.
Table 4: Case Study – Addressing Challenges
Challenge | Action Taken | Result |
---|---|---|
Quality Control | Implemented advanced inspection techniques | Reduced defects and improved product quality |
Production Efficiency | Introduced automation in mold making and pouring | Increased production rates and efficiency |
Environmental Compliance | Installed emission control systems and developed recycling processes | Achieved regulatory compliance and sustainability |
Conclusion
Sand casting manufacturers face numerous challenges that can impact their operations and product quality. By focusing on improving quality control, enhancing production efficiency, ensuring environmental compliance, addressing skilled labor shortages, and integrating technological advancements, sand casting manufacturers can overcome these challenges and remain competitive in the market. Continuous improvement, strategic investments, and a commitment to quality and sustainability are essential for the long-term success of sand casting manufacturers. Through these efforts, manufacturers can produce high-quality, precise, and durable castings that meet the demands of various industries.