Sustainable practices are becoming increasingly crucial in the steel casting industry, driven by environmental concerns and regulatory pressures. Steel casting manufacturers are adopting a variety of sustainable practices to minimize their environmental impact, improve energy efficiency, and create more sustainable production cycles. Here are some key sustainable practices that steel casting manufacturers might implement:
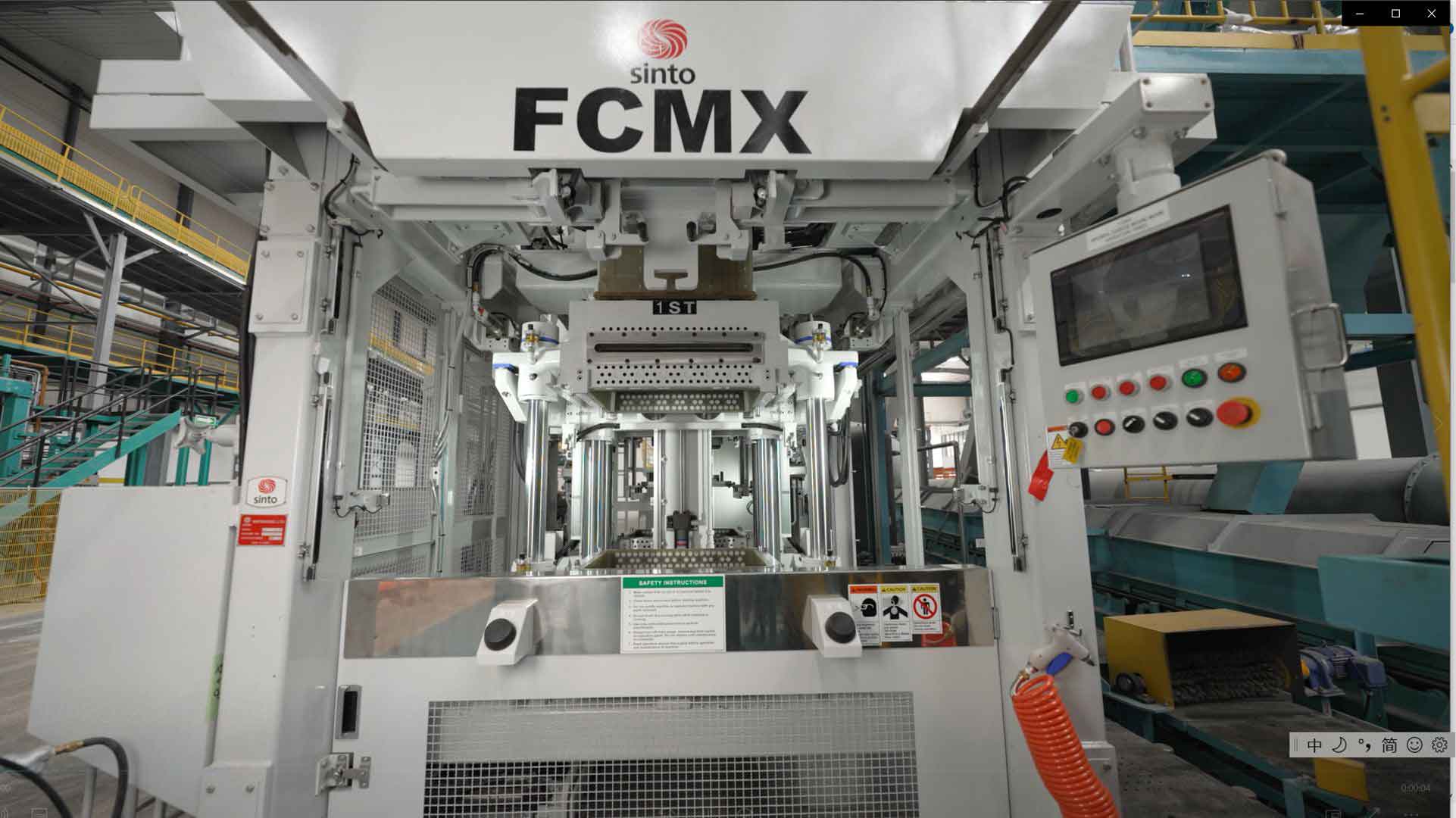
1. Energy Efficiency Improvements
- Advanced Furnaces: Using energy-efficient furnaces that require less fuel to melt and maintain metal at required temperatures.
- Heat Recovery Systems: Implementing heat recovery systems to utilize the heat generated during the casting process for other plant operations, reducing overall energy consumption.
2. Use of Renewable Energy
- Solar and Wind Power: Installing solar panels and wind turbines to power operations can significantly reduce reliance on non-renewable energy sources.
- Green Energy Purchases: Purchasing energy from renewable sources through green energy credits or direct purchase agreements.
3. Waste Reduction and Recycling
- Metal Recycling: Recycling scrap metal and defective products to reduce waste and decrease the demand for raw materials.
- Sand Reclamation: Using systems to reclaim and recycle sand from the molding process, reducing the need for new sand and minimizing landfill waste.
4. Water Conservation
- Closed-Loop Water Systems: Implementing closed-loop systems for cooling and other processes to reduce water usage.
- Water Treatment Facilities: Installing on-site water treatment facilities to clean and reuse wastewater.
5. Emission Controls
- Air Filtration Systems: Employing advanced filtration systems to capture and treat emissions from furnaces and other sources.
- Carbon Capture and Storage (CCS): Exploring CCS technologies to capture CO2 emissions from the production process and store them underground.
6. Eco-Friendly Material Use
- Biodegradable Binders: Using biodegradable or less toxic binders in the sand casting process to reduce environmental toxicity.
- Alternative Raw Materials: Researching and utilizing alternative raw materials that are more sustainable but maintain the integrity and quality of the castings.
7. Sustainable Product Design
- Life Cycle Assessment (LCA): Conducting LCAs to understand the environmental impacts of products throughout their lifecycle and improving design for reduced environmental impact.
- Design for Recycling: Designing products that are easier to disassemble and recycle at the end of their life cycle.
8. Community and Regulatory Engagement
- Compliance with Environmental Standards: Ensuring all operations comply with local, national, and international environmental regulations.
- Community Outreach: Engaging with local communities to support environmental initiatives and improve the societal impact of the business.
9. Employee Training and Involvement
- Sustainability Training: Providing training for employees on sustainable practices and encouraging them to contribute ideas for improving sustainability.
- Incentive Programs: Implementing incentive programs that reward employees for successfully implementing or suggesting sustainability improvements.
By adopting these sustainable practices, steel casting manufacturers can not only mitigate their environmental impact but also potentially reduce costs, improve their brand reputation, and comply with increasingly stringent environmental regulations. These practices also position manufacturers well for future industry shifts towards more sustainable and responsible manufacturing methods.