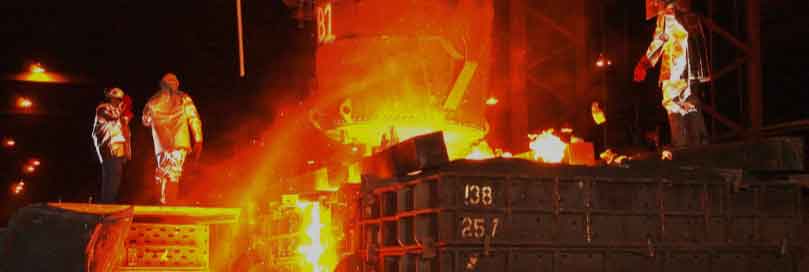
When selecting the right steel casting process, several considerations and selection criteria should be taken into account. Here are some key factors to consider:
- Design Complexity: Evaluate the complexity of the desired casting design. Some processes, such as investment casting (also known as precision casting), are better suited for intricate and complex designs with fine details and tight tolerances.
- Casting Size and Weight: Consider the size and weight of the casting. Different processes have limitations on the size and weight they can accommodate. For larger and heavier castings, processes like sand casting or centrifugal casting may be more suitable.
- Production Volume: Determine the production volume required. Some processes are more suitable for high-volume production, such as die casting or continuous casting, while others, like investment casting, are better for smaller production runs.
- Surface Finish and Precision: Assess the desired surface finish and precision of the casting. Processes like investment casting or die casting can achieve excellent surface finish and dimensional accuracy, while processes like sand casting may result in a rougher surface.
- Material Selection: Consider the specific steel alloy required for the casting. Different processes may have limitations or advantages in working with certain steel alloys. Ensure that the chosen process is compatible with the desired steel grade and its specific properties.
- Cost Considerations: Evaluate the overall cost of the casting process, including material costs, tooling costs, labor costs, and equipment costs. Some processes, such as sand casting, may be more cost-effective for larger production volumes, while others, like investment casting, may be more expensive but offer better precision for smaller production runs.
- Lead Time and Production Efficiency: Consider the desired lead time for the castings and the production efficiency of the chosen process. Some processes may have shorter lead times and faster production rates, while others may require longer setup times and slower production rates.
- Quality Requirements: Evaluate the required quality standards for the castings. Consider factors such as dimensional accuracy, surface finish, mechanical properties, and non-destructive testing requirements. Some processes may offer better control over quality parameters than others.
- Environmental Impact: Assess the environmental impact of the casting process. Some processes, such as sand casting, may generate more waste and have higher energy consumption, while others, like investment casting or die casting, may be more efficient and generate less waste.
By considering these factors and selection criteria, you can choose the most appropriate steel casting process that aligns with your specific requirements in terms of design complexity, casting size, production volume, surface finish, material selection, cost, lead time, quality, and environmental impact.