Casting, though an efficient and versatile method for manufacturing a wide range of components, is not without its potential flaws. Casting defects can greatly affect the functionality, durability, and aesthetics of the final product. This article will explore some common casting defects and share some effective preventive measures.
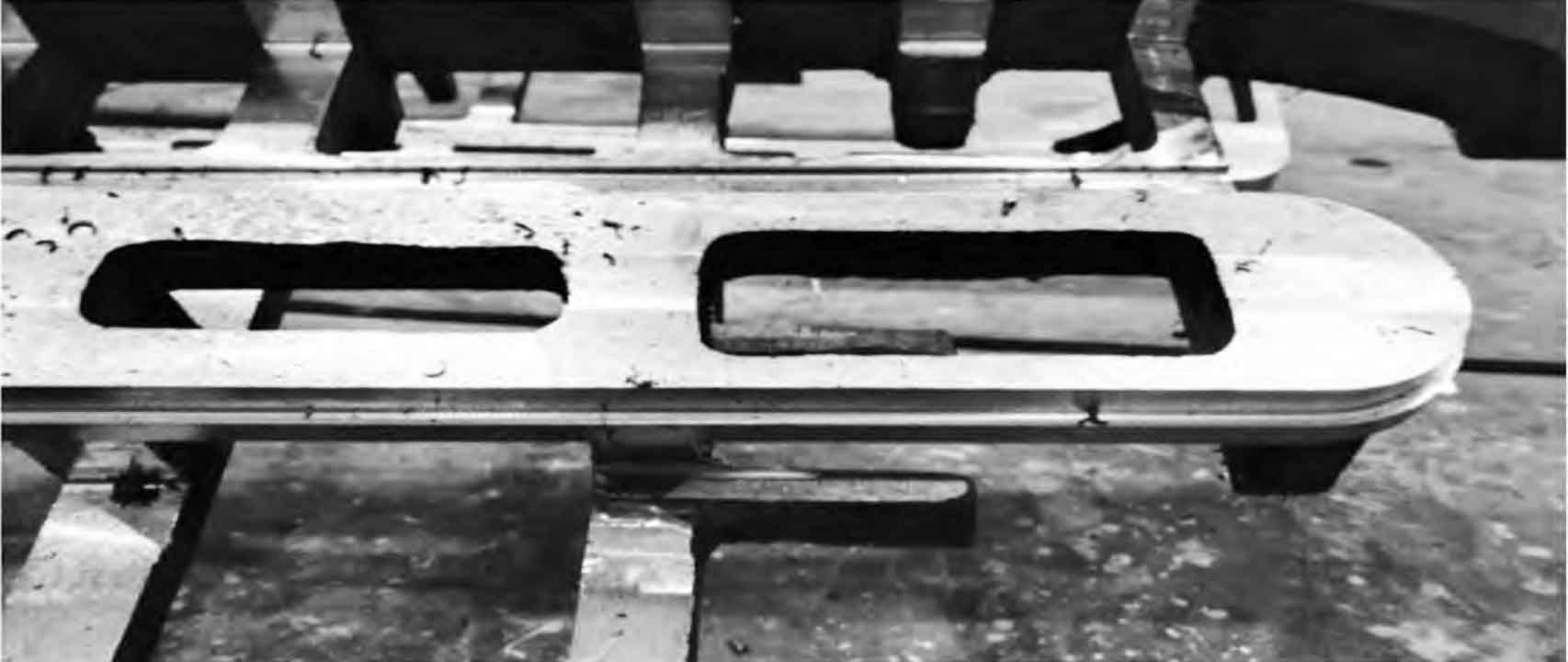
- Porosity: Porosity is the formation of cavities or pores within a casting, often caused by gas entrapment or shrinkage during solidification. To prevent porosity, foundries can optimize their pouring techniques, regulate the temperature of the molten metal, and design proper ventilation in the molds to allow gases to escape.
- Shrinkage: Shrinkage defects occur when the metal contracts during solidification and insufficient liquid metal is available to fill the shrinking volume. Proper riser design and placement, optimizing the casting process parameters like pouring temperature and rate, and appropriate alloy selection can mitigate shrinkage defects.
- Hot Tears: Hot tears are cracks that form in the casting during the final stages of solidification when the metal is weak and brittle. To prevent hot tears, foundries can ensure a uniform cooling rate and minimize the stresses on the casting by using appropriate mold materials and designs.
- Cold Shut: Cold shut defects occur when two streams of liquid metal flowing together in the mold fail to fuse completely, creating a seam or line on the casting. This defect can be prevented by improving the flow of the molten metal through the mold and maintaining the proper pouring temperature.
- Misruns and Cold Shots: Misruns occur when the molten metal fails to fill the mold cavity before solidifying, while cold shots are small globules of metal that solidify before integrating with the rest of the casting. These defects can be prevented by maintaining the appropriate pouring temperature and speed, and by optimizing the design of the gating system.
- Mold Material Defects: Defects can also result from inappropriate mold material or poor mold preparation. These can include cuts and washes, which are scratches or gouges in the casting surface, or scabs, which are raised areas caused by mold material breaking off and sticking to the casting. To prevent these defects, foundries should ensure the molds are correctly prepared and of the right material and strength.
Casting defects, if not addressed, can negatively impact the quality and performance of the final product. Therefore, foundries must be vigilant in their casting processes, from the design of the mold and gating system to the pouring and cooling of the metal. Regular inspections and testing can also help identify and rectify potential problems early, ensuring high-quality, defect-free castings.