The quality of a cast component greatly depends on its freedom from defects. However, despite careful process control, casting defects can still occur due to a variety of factors. Detecting these defects and rectifying them is a vital part of the casting process. This article outlines several common techniques used to detect and rectify defects in metal casting.
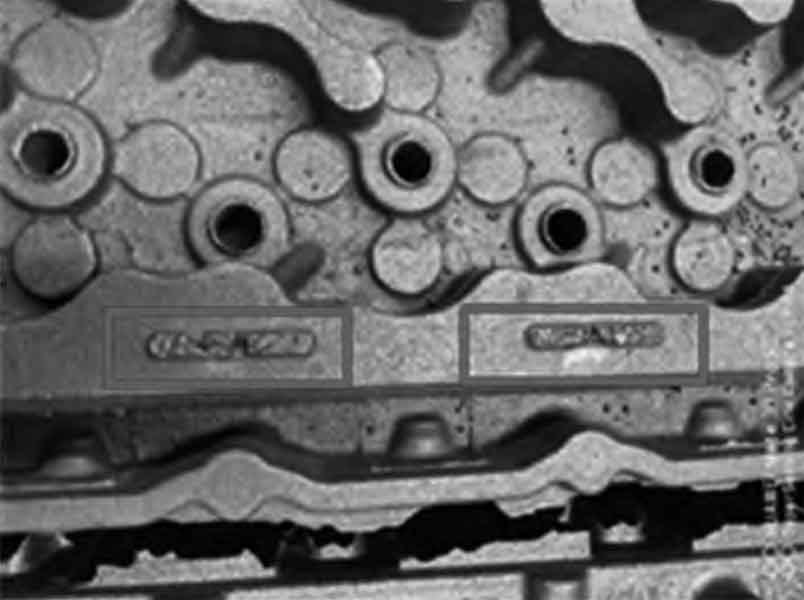
- Visual Inspection: The most basic method of detection, visual inspection involves examining the casting for any visible defects such as cracks, blowholes, and surface irregularities. While simple and inexpensive, visual inspection can only detect surface defects and is therefore often used in conjunction with other, more sophisticated methods.
- Radiographic Testing: Radiographic testing involves the use of X-rays or gamma rays to inspect the internal structure of the casting. This method can detect subsurface and internal defects such as inclusions, porosity, and shrinkage defects. Once identified, these defects can often be rectified through welding or grinding, or in severe cases, the casting may need to be scrapped and recast.
- Ultrasonic Testing: Ultrasonic testing uses high-frequency sound waves to detect defects within the casting. This technique can identify defects like inclusions, cracks, or voids that may not be visible on the surface. Depending on the nature and location of the defect, techniques like welding, heat treatment, or even redesigning the casting process might be required to rectify these defects.
- Magnetic Particle Inspection: This method is used for detecting surface and near-surface defects in ferromagnetic materials. The casting is magnetized, and iron particles are applied to the surface. If there is a defect, the magnetic field will be disturbed, and the iron particles will cluster around the defect, making it visible. Surface defects can usually be repaired by grinding or welding.
- Dye Penetrant Inspection: This method is used to detect surface-breaking defects. A brightly colored dye is applied to the surface, allowed to penetrate any defects, and then a developer is applied which draws out the dye, making the defect visible. As with magnetic particle inspection, defects found using this method can typically be repaired by grinding or welding.
- Eddy Current Testing: Eddy current testing uses electromagnetic induction to detect defects in non-ferrous materials. This technique can identify surface and near-surface defects, which can then be rectified through grinding, welding, or in some cases, recasting.
Detecting and rectifying defects in metal casting is crucial to ensuring the quality of the final product. By applying the appropriate testing techniques and remedial measures, manufacturers can significantly reduce the incidence of casting defects and produce high-quality, reliable components. As technology advances, newer and more effective methods of defect detection and rectification are likely to become available, further enhancing the casting process.