1 Preface
Lost foam casting (EPC for short), also known as negative compaction casting, has been invented by Americans since 1956 until the 80s of the last century It has developed to a considerable scale and has been successfully applied to industrial production. From single-piece small-batch large-piece production to large-scale small-piece assembly line production, from simple non-processed parts production to complex processed parts production, the United States, Italy, Germany, Japan and other countries are more representative of industrial production. By the 90s of last century, the use of lost foam casting method for automobile castings has gradually developed, so far, there have been more than 3,000 manufacturers using lost foam casting process in China, but most of them are small single pieces or small batch castings Give birth. At present, the lost foam casting technology in China is still in the mature stage of technology, and the characteristics and laws of casting need to be deeply understood, especially the filling characteristics of molten metal, the properties of coatings, and the pyrolysis characteristics of the pattern Theoretical research such as sex has not been fully mastered, resulting in castings are prone to some defects, such as carburization of castings, sand inclusion, sticky sand, deformation, and collapse of the box during pouring, and the paint is difficult to fall off after pouring. Since 2009, I have been committed to the research and development of lost foam casting process of carbon steel castings, this article will analyze the defects such as carburization, porosity, slag inclusion, reverse injection and negative pressure cutting that are easy to occur in the trial production process, and provide some guidance for the process to be better applied to the production of steel castings.
2 Common defects and preventive measures
2.1 Carbonization defects
Carburization is one of the common defects in the lost foam casting process of steel castings. The foam mold material is mainly composed of carbon and hydrogen, in Rapid decomposition under high-temperature molten steel to produce hydrogen and free carbon, because the affinity between hydrogen and oxygen is stronger than carbon, the high-temperature decomposition of hydrogen first combines with oxygen between the gap of the pattern as water vapor discharge, and decomposed
A large amount of free carbon remains in the mold, impregnated with the surface of the molten steel,
As a result, carburizing on the surface of the casting is produced, that is, carburization. According to the relevant literature And the experiment found that there is a certain regularity in carbon increase, that is, carbon increase is mainly produced Now the surface of the casting, the core almost does not add carbon, and the inner gate is nearby Without carbonization, the farther away from the inner gate, the more serious the carbonization. For carbon increase The following measures can basically control the carbon content of castings Within the scope of process requirements:
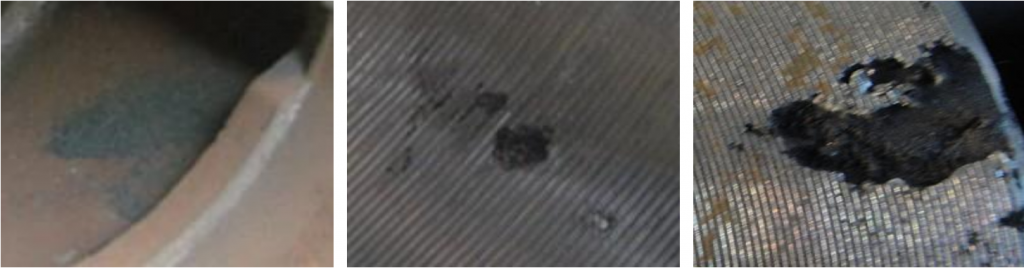
Figure 1 Carbon defect diagram of steel castings
(1) Use high-quality foam plastic The quality of foam directly affects the vaporization rate of the mold and the morphology of the cracking product during the pouring process. High quality foam plastic
The material has low carbon content, large molecular weight, and lower model density under the same foam strength. The use of raw beads with less gas generation and low carbon content and molding foam with low bulk density and light weight are lost foam casting The preferred conditions for steel parts are also the most effective way to solve the problem of carbon enhancement in cast steel.
(2) Choose a reasonable pouring process
The lost foam casting pouring process should be designed to accelerate the gasification of the mold and reduce and stagger the liquid and solid phases and steel in the decomposition product The contact and reaction time of the liquid, reducing or avoiding carburizing of steel castings. It mainly includes controlling the pouring temperature and pouring speed, good coating permeability and dry sand casting air permeability, suitable negative pressure of the mold wall, the use of anti-carburizing coatings, etc.
(3) Taking advantage of the characteristics that the farther away from the inner gate, the more serious the carbon increase, set the tail at the farthest end from the inner gate or at the highest point of the casting
port, so that the molten steel with serious carbonization pollution that first enters the mold cavity enters the riser, and the casting body obtains a purer molten steel.
(4) “Burn first and then pour”, that is, burn the foam plastic in the cavity to form a cavity, and then pour molten metal.
2.2 Stomatic defects
According to the cause, the pores generated by lost foam casting steel castings are divided into the following four categories:
(1) The pores generated by the foam pattern cracking product involved in the molten metal produce turbulence during the pouring and filling process, or during the gasification process, part of the pattern is surrounded by the metal liquid and cracked, and the gas produced cannot be discharged from the molten metal, and pores will be formed. This pores are large and numerous, and there is carbon black on the inner surface. Prevention measures: improve the process to make the molten steel fill smoothly without turbulence; Reasonably increase the pouring temperature and increase the negative pressure (if turbulence causes pores, reduce the negative pressure); Improve the coating
and molding sand air permeability. (2) Porosity caused by foam pattern and poor drying of paint
When the foam pattern coating is poorly dried and the foaming agent content is too high, a large amount of gas will be generated during pouring and cause porosity. Prevention measures: fully dry the foam pattern (according to the characteristics of the foaming molding process of the mold material); The coating must dry thoroughly and the amount of blowing agent added is strictly controlled.
(3) Too much mold adhesive causes pores
The mold binder has a large amount of gas, excessive use, and slow gasification, which is easy to roll the gas into the molten steel to form pores. Prevention measures: choose a model binder with low outgassing, and under the premise of ensuring strong adhesion, the less adhesive the better.
(4) When pouring, air is involved to form pores When pouring, the straight runner is not full, easy to be involved in air, if these gases cannot be discharged in time, it is easy to cause pores. Preventive measures: design a reasonable pouring system, fill the gold type The liquid flow is stable and does not roll up; When pouring with a closed gating system, ensure that there is a certain amount of molten metal in the gate cup to ensure that the straight runner is full; The use of hollow straight runner molds reduces the amount of air generated and helps prevent porosity.
(5) The porous carbon steel smelting process caused by the quality of molten steel smelting contains gas, which needs to be pre-deoxidized and final deoxidized, if the deoxidation is insufficient, oxygen will remain in the molten steel to form pores. Preventive measures: melting process
, strictly follow the smelting process, deoxidation treatment is carried out before pouring, and molten steel is purified.
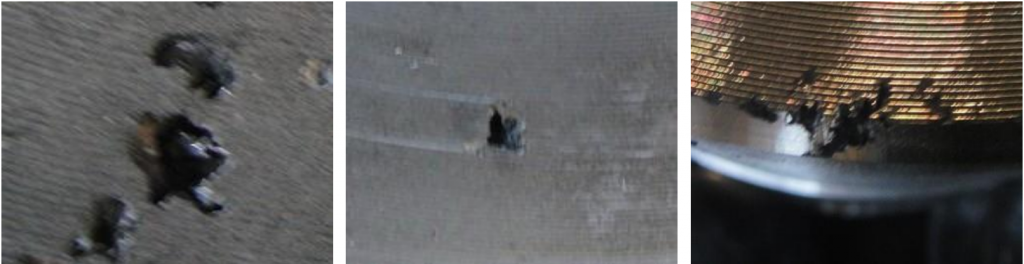
Figure 2 Diagram of porous defects in steel castings
2.3 Slag inclusion defects
Slag inclusion defects refer to the defects formed by dry sand, paint and other inclusions entering the casting with molten iron during the pouring process. It is a relatively common defect in the production of lost foam casting. On the surface of the machined casting, white or black-gray inclusion spots can be seen, single or in pieces, white for quartz sand particles, black gray for slag, paint, foam model after pyrolysis residue and other inclusions. After the lost foam casting is cooled out of the box, according to the surface condition of the casting and the pouring system, it can be determined whether there are sand ingress and slag inclusion defects. In production practice, if the gate cup, straight runner, cross runner, inner gate and gate surface or connection are glued, as well as the casting surface If the sand is severe or crack-like sticky sand is present, sand ingress may be caused in all parts from the gate cup, straight runner, cross runner, inner runner to casting. Among them, the straight runner is not tightly closed and other factors are created The most important cause of sand or slag inclusion defects. In addition, the size of the net head of the pouring system, the pouring temperature, the negative pressure, as well as the dry sand particle size, the mold transportation process, the packing operation and other process parameters are all important causes of casting slag inclusion and sand feeding defects. Slagging inclusion defects are a major problem in lost foam casting production.It is a systematic project, only by taking systematic measures and careful operation in these links can the slag inclusion defects of castings be reduced and basically eliminated, and high-quality castings can be obtained.
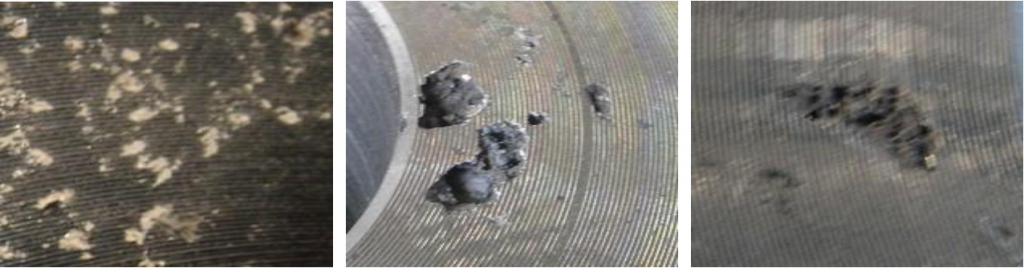
Fig. 3 Slag inclusion defect diagram of steel castings
(1) Select coatings with good comprehensive performance In addition to the general required performance, steel casting coatings are also required to have high strength, high refractory resistance, good heat burst and crack resistance,A series of properties such as coating, suspension, and non-flowing. To prevent slagging defects, the coating first requires high strength and fire resistance, and the straight gate is tightly closed when the molten steel enters the mold, and the coating layer on the surface of the casting and casting system does not fall off or crack. In addition, the coating applied to the white mold surface is required to have sufficient room temperature strength and not crack during drying and transportation. Furthermore, the coating layer should have good high-temperature strength, that is, during the pouring process, Under the long-term erosion of high-temperature metals, the paint does not fall off or crack, and the coating layer must have a certain thickness.
(2) Standardize the packing operation
When packing, the mold group should be stable when placed on the bottom sand of the sand box, and the sand shaking molding should be started when it is not allowed to be suspended to avoid cracking the coating layer. Do not add sand violently to the pattern, you should first use flexible sand to prevent the material layer from breaking, and tightly seal and close the straight gate to avoid sand. The whole packing and molding operation process should be very careful and careful, be sure to ensure that the coating layer of the mold group before pouring does not have any peeling, cracking and cracks, and before pouring, it should be confirmed again that the gate cup is free of floating sand, dust and debris.
(3) Reasonably set the pouring indenter, temperature and time, the higher the indenter when pouring, the greater the scouring of the pouring system and mold, the greater the possibility of sand ingress caused by the washed coating, and the indenter of different sizes of castings should also be different. Choose a pouring package with a suitable capacity, reduce the pouring height as much as possible, and the spout is as close to the sprue cup as possible to avoid pouring small tasks with large bales. Choose the appropriate pouring temperature, because the higher the pouring temperature, the higher the requirements for the performance of the coating, and the easier it is to produce defects such as sticky sand inclusion.
(4) Reasonable determination of negative pressure size lost foam casting pouring process is generally carried out under vacuum conditions, the role of negative pressure is to compact dry sand, accelerate exhaust, improve filling capacity, the size of negative pressure has a great impact on the quality of castings. Excessive negative pressure increases the possibility of inhalation of dry sand and inclusions when the molten metal flows through cracks and cracks, and also increases the sticky sand defects of castings. At the same time, the negative pressure is too large and the filling speed is too fast, which increases the erosion strength of the metal to the sprue and mold, which is easy to make
The paint falls off and enters the metal, and it is also easy to wash the paint layer and cause sand ingress. For steel castings, the suitable negative pressure is generally -0.030-0.045MPa.
(5) When setting the design of the slag stopper, skimming and slag riser pouring system, the function of slag stopper and slag skimmer should be considered, and the slag riser set on the casting is helpful to improve the sand infeed and slag inclusion defects.
(6) Adopt molten steel purification technology Molten steel smelting must pay attention to the purification problem, which is the lost mold One of the key technologies of casting, including melting from molten steel, superheating, The whole process of deoxidation until pouring into the mold should consider purification treatment.
2.4 Backspray
During the pouring process, due to the excessive amount of gas emitted by the thermal decomposition of the gas mold, and it cannot be eliminated in time, the air pressure in the casting cavity rises sharply
liter, easy to cause fire or molten metal, resulting in the scrapping of castings. Preventive measures are:
(1) EPS pattern density is controlled at 0.015~0.020 g/cm3 The appearance should be dried, and it should be dried after coating to reduce the moisture content and gas volume.
(2) Choose a coating with good air permeability, and adjust the thickness of the coating (1.0~2.0mm is appropriate) so that the gas is timely after the pattern cracking Escape.
(3) Control the air permeability and particle size of dry sand; The design of the sand box should be scientific, reasonable and applicable. control of negative pressure (vacuum pump suction),
The pattern is vaporized under the condition of true vacant oxygen, and rarely burns, reducing the amount of gas.
(4) Control the pouring temperature and pouring speed, use the heat of the molten steel to ensure the gasification of the mold, and control the pouring speed when the mold produces gas in large quantities, so as to avoid the pouring speed being too fast and promoting a large burst of cracking gas.
(5) Design a reasonable pouring system to ensure that the molten metal filling mold fills the mold smoothly, balancedly and quickly to ensure the mold The pyrolysis gas escapes outside the cavity and is sucked out.
2.5 Negative pressure cutting
The main reason: the sand box is under vacuum, due to the damage of the mold during the pouring process, causing the outside air to be sucked into the mold; The strong air flow penetration process has a penetrating and flushing force against the unsolidified molten metal
The formation of cutting phenomenon, we call it “negative pressure cutting” phenomenon.
The main reasons for this phenomenon:
The negative pressure is too high during pouring, the thickness of the paint is too thin or broken, pouring
The holding time after injection is too long. According to different casting structure size quality
The equal factor determines the process parameters, and the negative pressure in the sand box is generally in the general pouring Suitable negative pressure: -0.020-0.035MPa, coating thickness maintenance The certificate is 1.0-2.0mm, and the pouring package should be reduced as much as possible when pouring Injection height, spout as close as possible to the gate cup, holding time after pouring Control in 3-7 minutes.
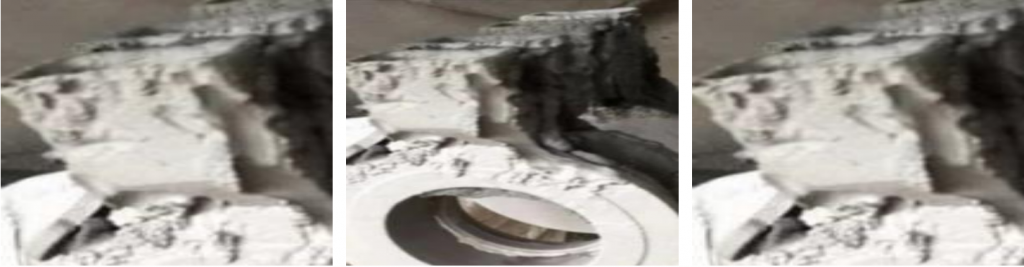
3 Summary
Steel casting lost foam casting has a large space for development in China’s lost foam casting industry, as long as effective production operations are adopted The control method carries out production operation control management, and strictly controls the melting process of castings, reduces and eliminates the process conditions of carbonization in the pouring process, combines the actual production conditions, increases the training of skilled technicians, improves the overall level of the team, and strictly controls each process in the process to produce fully qualified steel casting products.