1. Introduction
Lost foam casting has emerged as a popular manufacturing process due to its numerous advantages. It offers high precision in casting dimensions, excellent repeatability, flexibility in production, and good internal quality of the castings. This process has witnessed significant growth globally since the expiration of its patent in 1980 and has found extensive applications, especially in the production of complex shell components. However, like any manufacturing process, it is not without its challenges. This article focuses on analyzing the common defects that occur during the lost foam casting of flywheel housings and other components and presents effective solutions to address these issues.
1.1 The Significance of Lost Foam Casting
Lost foam casting has revolutionized the casting industry. It allows for the production of intricate and complex shapes with relative ease compared to traditional casting methods. The process involves creating a foam pattern of the desired component, coating it with a refractory material, and then pouring molten metal into the mold cavity created as the foam pattern vaporizes during the casting process. This unique approach eliminates the need for a separate pattern removal step, reducing labor and time requirements.
1.2 Common Defects in Lost Foam Casting
Despite its advantages, lost foam casting is prone to certain defects. These include sand burning-on, porosity, and sand washing. These defects can significantly affect the quality of the final casting, leading to increased scrap rates and higher production costs. Understanding the causes of these defects is crucial for implementing effective corrective measures.
2. Analysis of Sand Burning-on Defect
2.1 Causes of Sand Burning-on
Sand burning-on occurs when the molten metal adheres to the sand during the casting process. In the case of flywheel housings, several factors can contribute to this defect.
- Improper Placement and Design: The placement of the flywheel housing pattern in the sand box and its structural or process design can affect the compaction of the sand. If the pattern cannot be properly vibrated and compacted, it can lead to loose sand areas where the metal can adhere.
- Size and Thickness of the Component: Components like the 9661 flywheel housing, which have a large size area and relatively thin base wall thickness, are more susceptible to deformation. This can cause uneven compaction of the sand and result in sand burning-on.
2.2 Case Study: 9661 Flywheel Housing
The 9661 flywheel housing, made of HT250 with a weight of about 22 kg and dimensions of 440 mm x 440 mm x 220 mm, and a wall thickness of 5 mm, exhibited sand burning-on defects. The existing process had an inner gate size of 50 mm (length) x 30 mm (height) x 6 mm (width), an iron liquid tapping temperature of 1460 – 1470 °C, a pouring temperature of 1430 – 1440 °C, a vacuum degree of -0.025 MPa, without film coating and pressure retention. The main defect was sand inclusion in the top of the flywheel housing cavity, with a scrap proportion of 20%.
2.3 Control Measures for Sand Burning-on
To address the sand burning-on defect, the following measures were implemented:
- Adjusting Pattern Placement: The motor hole of the flywheel housing was placed upwards to facilitate better sand filling in the top area.
- Increasing Spacing: The distance between two flywheel housings was increased from 80 mm to 120 mm to enhance the compactness of the sand.
2.4 Production Verification
After implementing these measures, production verification was carried out. With the immersion coating process, pouring temperature, and vacuum degree remaining unchanged, production was scaled up from small batches to large batches. The sand burning-on defect was completely eliminated, demonstrating the effectiveness of the control measures.
3. Analysis of Porosity Defect
3.1 Causes of Porosity
Porosity in lost foam castings is often caused by the inability of the gases generated during the vaporization of the foam pattern to escape from the mold cavity in a timely manner. This can lead to the formation of pores in the casting.
- Pouring Temperature: If the pouring temperature is too low, the foam may not burn completely, leaving unburned residues and gases that can form pores.
- Coating Thickness and Permeability: Thick coatings or coatings with low permeability can prevent the gases from escaping, resulting in porosity.
- Vacuum Degree: Insufficient vacuum can also impede the removal of gases from the mold cavity.
- Lack of Exhaust Ports: Inadequate design of the casting with a lack of exhaust ports in critical areas can cause gas accumulation and porosity.
3.2 Case Study: Porosity in Flywheel Housing for SAIC Maxus
The flywheel housing for SAIC Maxus exhibited porosity defects. The iron liquid tapping temperature was 1460 – 1470 °C, the pouring temperature was 1430 – 1440 °C, the vacuum was -0.025 MPa, without film coating and pressure retention. The main defect was porosity in the motor hole at the top of the product, with a scrap proportion of 30%.
3.3 Control Measures for Porosity
To address the porosity defect, the following measures were taken:
- Increasing Pouring Temperature: The pouring temperature was raised from 1430 – 1440 °C to 1450 – 1460 °C.
- Reducing Coating Thickness: The coating thickness at the motor hole was reduced from 2.0 mm to 0.5 mm.
- Increasing Vacuum Degree: The vacuum degree was increased from -0.025 MPa to -0.045 MPa.
- Adding Exhaust Flakes: An exhaust flake of 50 mm (length) x 30 mm (height) x 5 mm (width) was added at the motor hole.
3.4 Production Verification
Production verification was carried out for the porosity defect. By varying one parameter at a time while keeping the others constant, different schemes were tested. Among them, adding an exhaust flake showed the best results, with zero porosity in subsequent large-scale production. This demonstrated the effectiveness of the control measures for porosity.
4. Analysis of Sand Washing Defect
4.1 Causes of Sand Washing
Sand washing occurs when sand is carried into the mold cavity by the molten metal during the casting process. This can be caused by several factors:
- Incomplete Sealing of the Pouring System: If the sprue, runner, or inner gate in the pouring system is not properly sealed, it can lead to a suction effect, causing sand to be drawn into the cavity.
- Unreasonable Design of the Pouring System: A poorly designed pouring system can result in uneven filling of the mold cavity, causing high local pressure in the inner gate and leading to coating rupture and sand entry.
4.2 Case Study: Sand Washing in Connecting Rod Frame Casting
The connecting rod frame casting had a sand washing defect. The material was HT200, weighing about 50 kg, with dimensions of 572 mm x 380 mm x 348 mm and a bottom plate thickness of 12 mm. The existing process introduced iron liquid through 3 inner gates on the side, with an inner gate size of 60 mm (length) x 30 mm (height) x 6 mm (width). The iron liquid tapping temperature was 1460 – 1470 °C, the pouring temperature was 1430 – 1440 °C, the vacuum was -0.03 MPa, without film coating and pressure retention. The main defect was sand washing, concentrated near the bottom inner gate, with a scrap proportion of 20%.
4.3 Control Measures for Sand Washing
To address the sand washing defect, the following measures were implemented:
- Increasing Coating Thickness: An additional immersion coating process was added to the inner gate, increasing the coating thickness to 2.2 mm.
- Increasing the Number of Inner Gates: An additional inner gate of the same size was added at the bottom.
4.4 Production Verification
Production verification was carried out for the sand washing defect. By keeping the pouring temperature and vacuum degree constant, different schemes were tested. Adding an additional inner gate at the bottom showed the best results, with zero sand washing in subsequent large-scale production. The final optimized pouring system had 3 inner gates at the bottom and 1 at the top, with the inner gates having a cross-sectional area of 60 mm x 8 mm, effectively solving the sand washing defect.
5. General Conclusions and Recommendations
5.1 Importance of Understanding Defect Causes
Understanding the causes of casting defects in lost foam casting is essential for improving the quality of the final product. By analyzing the specific factors contributing to sand burning-on, porosity, and sand washing defects, appropriate control measures can be implemented.
5.2 Process Optimization and Verification
The process of optimizing the casting process should be carried out in a systematic manner. This includes adjusting the pattern placement, optimizing the pouring system, and ensuring proper exhaust and slag discharge. During the verification process, it is crucial to start with small batches and gradually increase the production volume to avoid significant losses due to unforeseen issues.
5.3 Future Research Directions
Future research could focus on further improving the coating materials and techniques to enhance gas permeability and prevent defects. Additionally, exploring advanced design principles for the pouring system and pattern placement could lead to even better casting quality.
In conclusion, lost foam casting has great potential, but it requires careful attention to detail and continuous improvement to overcome the challenges associated with casting defects. By implementing the measures described in this article and continuing to explore new techniques and materials, the quality of lost foam castings can be significantly enhanced.
Defect | Causes | Case Study | Control Measures | Production Verification Results |
---|---|---|---|---|
Sand Burning-on | Improper placement and design, component size and thickness | 9661 Flywheel Housing | Adjusting pattern placement, increasing spacing | Defect eliminated |
Porosity | Pouring temperature, coating thickness and permeability, vacuum degree, lack of exhaust ports | Flywheel Housing for SAIC Maxus | Increasing pouring temperature, reducing coating thickness, increasing vacuum degree, adding exhaust flakes | Defect eliminated |
Sand Washing | Incomplete sealing of pouring system, unreasonable design of pouring system | Connecting Rod Frame Casting | Increasing coating thickness, increasing number of inner gates | Defect eliminated |
6. Detailed Analysis of Lost Foam Casting Process
6.1 The Principle of Lost Foam Casting
Lost foam casting operates on a unique principle. A polystyrene foam pattern, which is an exact replica of the desired casting, is created first. This pattern is then coated with a refractory material to form a mold. When the molten metal is poured into the mold, the foam pattern vaporizes due to the heat of the molten metal. The space left by the vaporized foam is then filled with the molten metal, which solidifies to form the final casting. This process eliminates the need for a separate pattern removal step, as the foam pattern disappears during the casting process.
6.2 The Role of Coating in Lost Foam Casting
The coating applied to the foam pattern plays a crucial role in the lost foam casting process. It serves multiple purposes:
- Protecting the Pattern: The coating protects the foam pattern from the direct heat of the molten metal. Without the coating, the foam pattern would quickly burn and disintegrate, leading to an improper casting.
- Controlling Gas Evolution: The coating has a certain level of permeability that allows the gases generated during the vaporization of the foam to escape in a controlled manner. If the coating is too impermeable, it can lead to porosity defects as the gases get trapped inside the mold.
- Providing a Smooth Surface: The coating helps in creating a smooth surface on the final casting. It fills in the small pores and irregularities on the surface of the foam pattern, resulting in a better finish on the casting.
6.3 The Importance of Pouring System Design
The design of the pouring system is another critical aspect of lost foam casting. A well-designed pouring system ensures that the molten metal flows smoothly and evenly into the mold cavity. It should be designed to avoid turbulence and splashing of the molten metal, as these can lead to defects such as porosity and sand washing. The pouring system typically consists of a sprue, runners, and inner gates. The size and shape of these components should be carefully determined based on the size and shape of the casting, as well as the properties of the molten metal.
7. Advanced Techniques for Defect Prevention
7.1 Use of Vacuum in Lost Foam Casting
The application of vacuum in lost foam casting is a common technique for preventing defects. By creating a vacuum in the mold cavity, the gases generated during the vaporization of the foam pattern can be more effectively removed. This helps in reducing porosity defects. Additionally, the vacuum can also help in improving the filling of the mold cavity by the molten metal, as it reduces the resistance to the flow of the metal. However, the vacuum level needs to be carefully controlled, as too high or too low a vacuum can lead to other problems.
7.2 Advanced Coating Materials and Techniques
Research is ongoing to develop advanced coating materials and techniques for lost foam casting. New coating materials with improved gas permeability and heat resistance are being explored. These materials can help in better controlling the evolution of gases during the casting process and prevent defects such as porosity. Additionally, techniques such as plasma spraying and electrophoretic deposition are being investigated for applying the coating more uniformly and effectively.
7.3 Computer-Aided Design and Simulation
Computer-aided design (CAD) and simulation tools are increasingly being used in lost foam casting. These tools allow engineers to design the casting and the pouring system more accurately before the actual production. By simulating the casting process, potential defects can be predicted and corrective measures can be taken in advance. This helps in reducing the trial-and-error process and saving time and resources.
8. Comparison with Other Casting Methods
8.1 Lost Foam Casting vs. Sand Casting
Lost foam casting offers several advantages over traditional sand casting. In sand casting, a separate pattern removal step is required, which is time-consuming and labor-intensive. Lost foam casting eliminates this step, reducing production time and costs. Additionally, lost foam casting can produce more complex shapes with better dimensional accuracy compared to sand casting. However, sand casting may be more suitable for some applications where a large number of simple castings are required, as the setup costs for sand casting may be lower.
8.2 Lost Foam Casting vs. Investment Casting
Compared to investment casting, lost foam casting has a simpler process. Investment casting requires the creation of a wax pattern, which is then coated with a ceramic shell. The wax pattern is then melted out, leaving a cavity for the molten metal. Lost foam casting, on the other hand, uses a foam pattern that vaporizes during the casting process. Lost foam casting can also produce larger castings compared to investment casting, as the foam pattern can be easily scaled up. However, investment casting may offer better surface finish and dimensional accuracy for some small and complex components.
9. Case Studies of Successful Applications
9.1 Automotive Industry
In the automotive industry, lost foam casting has been widely used for manufacturing various components such as engine blocks, cylinder heads, and flywheel housings. For example, a major automotive manufacturer used lost foam casting to produce flywheel housings. By implementing the defect prevention measures described in this article, they were able to significantly reduce the scrap rate and improve the quality of the castings. The final castings had excellent dimensional accuracy and a smooth surface finish, meeting the high standards of the automotive industry.
9.2 Aerospace Industry
The aerospace industry also benefits from lost foam casting. Components such as turbine housings and structural parts have been successfully produced using this process. In one case, an aerospace company used lost foam casting to produce a turbine housing. The use of advanced coating materials and techniques, along with a well-designed pouring system, ensured that the casting had a high quality with no porosity or other defects. The casting also met the strict weight and strength requirements of the aerospace application.
10. Future Trends and Challenges
10.1 Environmental Considerations
As environmental regulations become more stringent, the casting industry, including lost foam casting, needs to address environmental concerns. The use of polystyrene foam patterns in lost foam casting can lead to the release of harmful substances during the vaporization process. Research is being conducted to develop more environmentally friendly alternatives to polystyrene foam, such as biodegradable foams. Additionally, the disposal of used sand and coating materials also needs to be managed in an environmentally responsible manner.
10.2 Quality Control and Standardization
With the increasing demand for high-quality castings, quality control and standardization in lost foam casting become crucial. There is a need for more accurate and reliable testing methods to detect defects in castings. Standardized procedures for the casting process, including pattern making, coating, and pouring, should be established to ensure consistent quality across different production batches. This will help in meeting the quality requirements of various industries and improving the competitiveness of lost foam casting in the market.
10.3 Technological Advancements
The future of lost foam casting will depend on continuous technological advancements. This includes the development of new coating materials, pouring system designs, and simulation tools. The integration of artificial intelligence and machine learning in the casting process can also provide new opportunities for defect prediction and process optimization. By staying at the forefront of technological advancements, lost foam casting can continue to improve its performance and expand its applications in various industries.
In conclusion, lost foam casting is a promising manufacturing process with many advantages. However, it also faces several challenges related to defect prevention, environmental impact, quality control, and technological advancements. By addressing these challenges through research and development, lost foam casting can achieve higher quality and more sustainable production, further enhancing its value in the manufacturing industry.
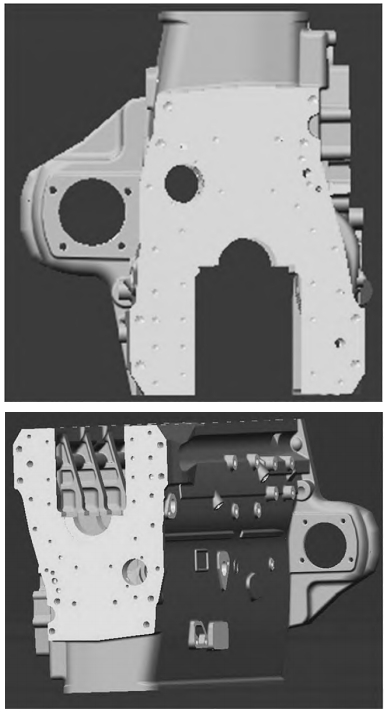