Investment casting and die casting are two widely used manufacturing processes for producing metal parts with high precision and quality. Each process has its own advantages and limitations, making them suitable for different applications and requirements. This article provides a comparative analysis of investment casting parts and die casting parts, highlighting their characteristics, benefits, and applications.
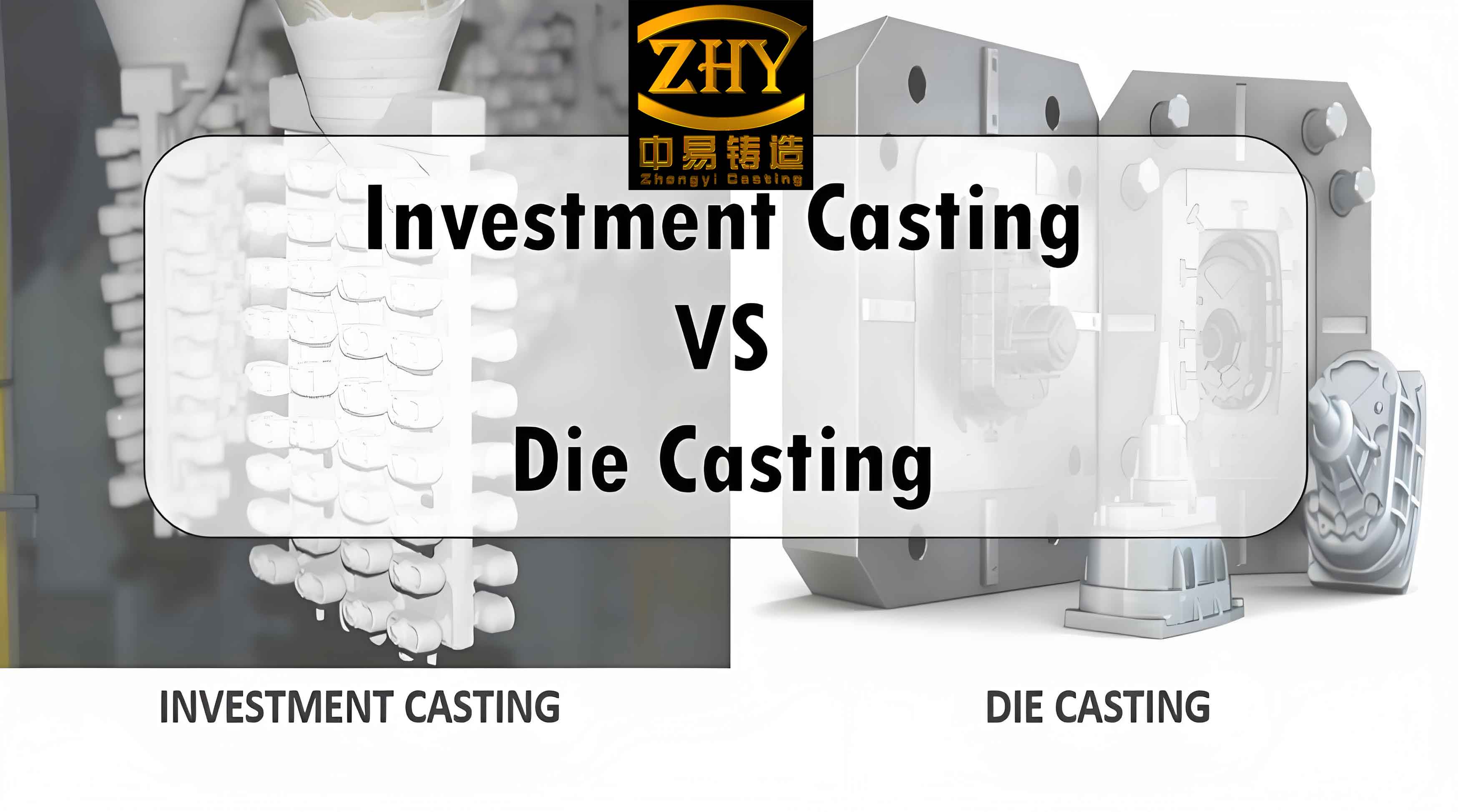
Introduction to Investment Casting and Die Casting
Investment Casting
Investment casting is a process that involves creating a wax model of the desired part, coating it with a refractory ceramic material, and then melting the wax out to leave a ceramic mold. Molten metal is then poured into the mold to create the final part. This process allows for the production of complex and intricate parts with high precision and excellent surface finish.
Die Casting
Die casting is a process that involves forcing molten metal into a mold cavity under high pressure. The molds, also known as dies, are usually made from high-grade steel and can be reused multiple times. Die casting is known for its ability to produce high-volume parts with excellent dimensional accuracy and smooth surfaces.
Comparative Analysis
Material Compatibility
Investment casting parts and die casting parts can be produced using a variety of metals and alloys. However, the material selection differs based on the process capabilities.
- Investment Casting Parts: Compatible with a wide range of metals including stainless steel, aluminum, bronze, and titanium.
- Die Casting Parts: Typically produced using non-ferrous metals such as aluminum, zinc, and magnesium.
Dimensional Accuracy and Surface Finish
Both investment casting parts and die casting parts are capable of producing parts with high dimensional accuracy and good surface finish, but there are some differences.
- Investment Casting Parts: Known for excellent surface finish and high precision, often requiring little to no machining.
- Die Casting Parts: Also offer good surface finish and accuracy, but may require additional machining for tight tolerances.
Complexity and Design Flexibility
Investment casting parts and die casting parts offer different levels of design flexibility and complexity in the parts they can produce.
- Investment Casting Parts: Capable of producing highly complex and intricate shapes with fine details, making it suitable for parts with internal cavities and thin walls.
- Die Casting Parts: More suitable for simpler shapes and larger production runs, but advances in die design have improved its capability to produce moderately complex parts.
Production Volume and Cost
The choice between investment casting parts and die casting parts often depends on the production volume and associated costs.
- Investment Casting Parts: Ideal for low to medium production volumes due to the higher cost of creating wax patterns and ceramic molds.
- Die Casting Parts: More cost-effective for high-volume production runs due to the reusable nature of the dies and faster production rates.
Mechanical Properties
The mechanical properties of investment casting parts and die casting parts can vary based on the materials used and the specific process parameters.
- Investment Casting Parts: Generally offer superior mechanical properties due to the ability to use high-performance alloys and the uniform cooling process.
- Die Casting Parts: May have slightly lower mechanical properties compared to investment casting parts, but advancements in die casting techniques have narrowed this gap.
Table 1: Comparative Summary of Investment Casting Parts and Die Casting Parts
Criteria | Investment Casting Parts | Die Casting Parts |
---|---|---|
Material Compatibility | Wide range of metals including stainless steel, aluminum, bronze, and titanium | Non-ferrous metals such as aluminum, zinc, and magnesium |
Dimensional Accuracy | High precision, little to no machining required | Good accuracy, may require additional machining |
Surface Finish | Excellent surface finish | Good surface finish |
Design Complexity | High complexity, intricate shapes with fine details | Moderate complexity, simpler shapes |
Production Volume | Low to medium volumes | High volumes |
Cost | Higher initial cost, lower production cost for complex parts | Lower initial cost, more cost-effective for high volumes |
Mechanical Properties | Superior mechanical properties | Good mechanical properties |
Applications of Investment Casting Parts and Die Casting Parts
Investment Casting Parts
Investment casting parts are widely used in industries where high precision and complex shapes are required. Some common applications include:
- Aerospace: Turbine blades, structural components, and engine parts.
- Medical Devices: Surgical instruments, implants, and prosthetics.
- Automotive: Engine components, transmission parts, and suspension systems.
- Industrial Equipment: Pumps, valves, and machinery components.
Die Casting Parts
Die casting parts are commonly used in industries where high-volume production and good mechanical properties are essential. Some common applications include:
- Automotive: Engine blocks, gearbox housings, and brake components.
- Consumer Electronics: Housings for devices, connectors, and heat sinks.
- Appliances: Components for refrigerators, washing machines, and air conditioners.
- Telecommunications: Antenna mounts, connectors, and enclosures.
List: Key Industries Using Investment Casting Parts and Die Casting Parts
- Aerospace
- Medical Devices
- Automotive
- Industrial Equipment
- Consumer Electronics
- Appliances
- Telecommunications
Case Study: Investment Casting vs. Die Casting for an Automotive Component
Problem
An automotive manufacturer needed to produce a complex engine component with high precision and excellent mechanical properties. The choice between investment casting parts and die casting parts had to be made based on cost, production volume, and part requirements.
Solution
The manufacturer conducted a comparative analysis:
- Investment Casting Parts: Selected for its ability to produce complex shapes with high precision and superior mechanical properties. The higher initial cost was justified by the need for intricate details and minimal machining.
- Die Casting Parts: Considered for its cost-effectiveness in high-volume production and good mechanical properties. However, the complexity of the part and the need for high precision made investment casting the preferred choice.
Result
The investment casting process provided the desired quality and precision for the engine component, resulting in improved performance and reduced post-processing. The higher initial cost was offset by the benefits of reduced machining and higher part reliability.
Table 2: Case Study Results
Criteria | Investment Casting | Die Casting |
---|---|---|
Complexity | High complexity, intricate shapes achieved | Moderate complexity, simpler shapes |
Precision | High precision, minimal machining required | Good precision, additional machining |
Mechanical Properties | Superior mechanical properties | Good mechanical properties |
Cost | Higher initial cost, lower overall cost | Lower initial cost, higher post-processing cost |
Production Volume | Low to medium volumes | High volumes |
Conclusion
Investment casting parts and die casting parts are both highly effective manufacturing processes, each with its own advantages and suitable applications. Investment casting parts are ideal for low to medium volume production with high complexity and superior mechanical properties, while die casting parts are more cost-effective for high-volume production with good accuracy and mechanical properties. Understanding the strengths and limitations of each process allows manufacturers to choose the best method for their specific requirements, ensuring optimal performance and cost-efficiency in their products.