Sand casting is a versatile manufacturing process that allows for the creation of complex metal parts. The durability and performance of sand casting parts heavily depend on the selection of appropriate alloys. Innovative alloy selection can significantly enhance the mechanical properties, wear resistance, and longevity of sand casting parts. This article explores the various alloys used in sand casting parts, their properties, and the benefits they bring to high-performance applications.
Introduction to Sand Casting
Sand casting involves creating a mold from a sand mixture, pouring molten metal into the mold, and allowing it to solidify. The mold is then broken away to reveal the metal part. This process is widely used due to its ability to produce large and intricate components at a relatively low cost. However, the choice of alloy is critical to ensure the final product meets the required specifications for durability and performance.
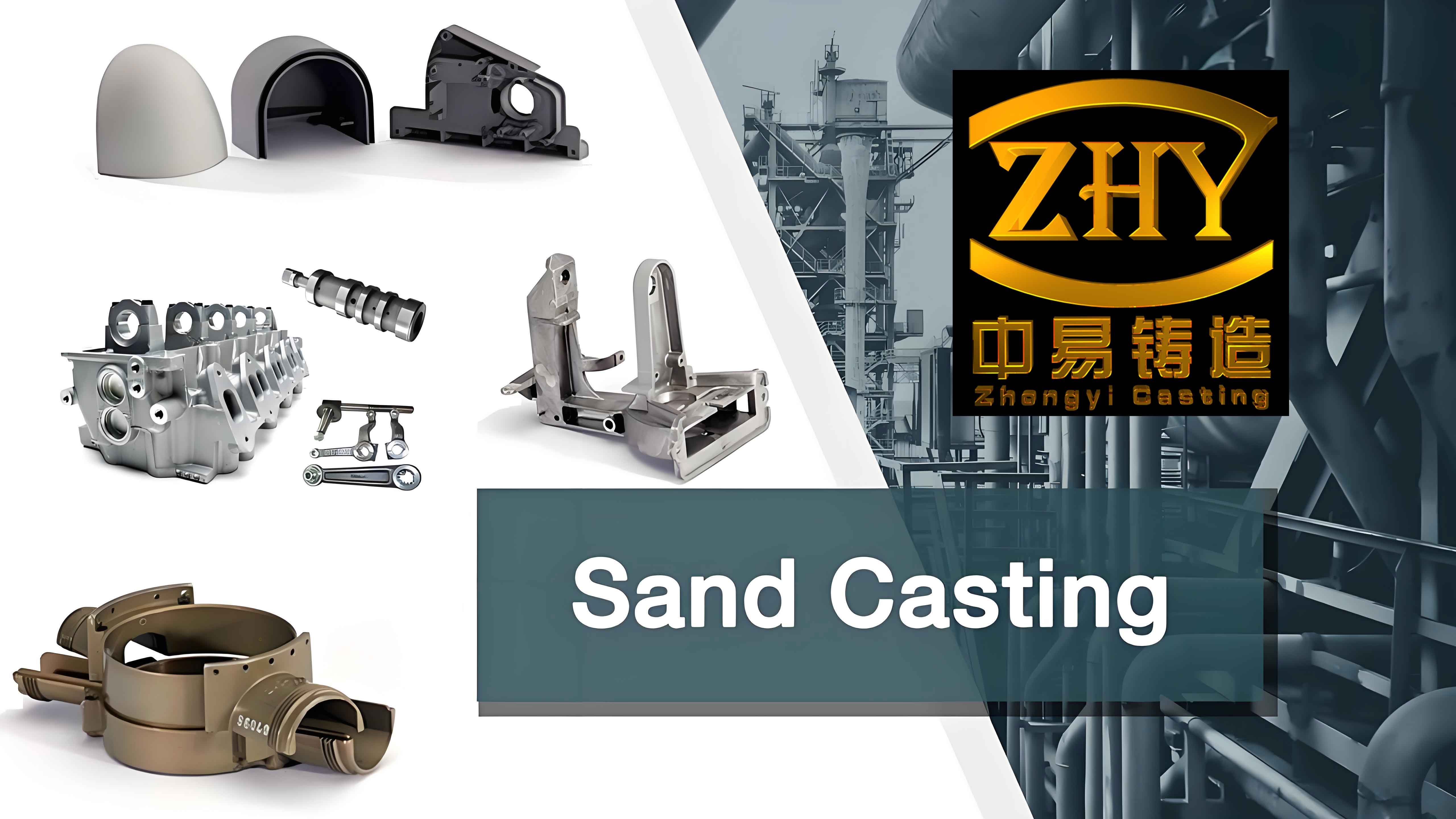
Importance of Alloy Selection in Sand Casting Parts
Selecting the right alloy is essential for achieving the desired mechanical properties and ensuring the durability of sand casting parts. The alloy must be able to withstand the operating environment, which includes factors such as temperature, stress, and exposure to corrosive elements.
Common Alloys Used in Sand Casting Parts
Gray Cast Iron
Gray cast iron is a popular choice for sand casting parts due to its excellent machinability and vibration damping properties.
- Applications: Engine blocks, machine frames, pipe fittings
- Properties: Good wear resistance, high compressive strength, excellent machinability
Ductile Iron
Ductile iron, also known as nodular iron, offers higher strength and ductility compared to gray cast iron.
- Applications: Automotive components, hydraulic components, agricultural machinery
- Properties: High tensile strength, good impact resistance, excellent wear resistance
Aluminum Alloys
Aluminum alloys are favored for their lightweight and good corrosion resistance, making them ideal for various high-performance applications.
- Applications: Aerospace components, automotive parts, heat exchangers
- Properties: Lightweight, good thermal and electrical conductivity, excellent corrosion resistance
Steel Alloys
Steel alloys provide exceptional strength and durability, suitable for demanding environments.
- Applications: Structural components, heavy machinery parts, tools
- Properties: High tensile strength, excellent toughness, good wear resistance
Table 1: Common Alloys and Their Properties
Alloy | Applications | Properties |
---|---|---|
Gray Cast Iron | Engine blocks, machine frames, pipe fittings | Good wear resistance, high compressive strength, excellent machinability |
Ductile Iron | Automotive components, hydraulic components | High tensile strength, good impact resistance, excellent wear resistance |
Aluminum Alloys | Aerospace components, automotive parts | Lightweight, good thermal and electrical conductivity, excellent corrosion resistance |
Steel Alloys | Structural components, heavy machinery parts | High tensile strength, excellent toughness, good wear resistance |
Innovative Alloys for Enhanced Durability
High-Silicon Cast Irons
High-silicon cast irons are known for their excellent corrosion resistance, making them suitable for harsh environments.
- Applications: Pumps, valves, chemical processing equipment
- Properties: Superior corrosion resistance, good wear resistance, moderate strength
Alloyed Ductile Irons
Adding alloying elements such as nickel, chromium, and molybdenum to ductile iron can significantly enhance its mechanical properties and resistance to wear and corrosion.
- Applications: Mining equipment, heavy-duty gears, crankshafts
- Properties: High strength, excellent wear resistance, good corrosion resistance
High-Strength Aluminum Alloys
Advanced aluminum alloys, such as Al-Si-Mg and Al-Cu-Mg alloys, offer improved strength and durability, making them ideal for aerospace and automotive applications.
- Applications: Structural components, aerospace fittings, high-performance automotive parts
- Properties: High strength-to-weight ratio, good fatigue resistance, excellent corrosion resistance
Alloyed Steels
Alloyed steels, incorporating elements like chromium, nickel, and vanadium, provide exceptional strength and toughness for heavy-duty applications.
- Applications: Industrial machinery, cutting tools, pressure vessels
- Properties: High tensile and yield strength, excellent toughness, good wear and corrosion resistance
Table 2: Innovative Alloys and Their Benefits
Alloy | Applications | Properties |
---|---|---|
High-Silicon Cast Irons | Pumps, valves, chemical processing equipment | Superior corrosion resistance, good wear resistance, moderate strength |
Alloyed Ductile Irons | Mining equipment, heavy-duty gears | High strength, excellent wear resistance, good corrosion resistance |
High-Strength Aluminum Alloys | Structural components, aerospace fittings | High strength-to-weight ratio, good fatigue resistance, excellent corrosion resistance |
Alloyed Steels | Industrial machinery, cutting tools | High tensile and yield strength, excellent toughness, good wear and corrosion resistance |
Factors Influencing Alloy Selection
Operating Environment
The operating environment plays a crucial role in determining the suitable alloy for sand casting parts. Factors such as temperature, exposure to corrosive elements, and mechanical stresses must be considered.
- High-Temperature Applications: Alloys with high thermal stability, such as alloyed steels and high-silicon cast irons, are ideal for high-temperature environments.
- Corrosive Environments: Alloys with excellent corrosion resistance, like high-silicon cast irons and certain aluminum alloys, are suitable for corrosive environments.
Mechanical Properties
The required mechanical properties, such as tensile strength, ductility, and wear resistance, are critical factors in alloy selection.
- High Strength: For applications requiring high strength, alloyed steels and high-strength aluminum alloys are preferred.
- Wear Resistance: For parts subjected to abrasion and wear, ductile iron and alloyed ductile irons offer excellent wear resistance.
Cost Considerations
The cost of the alloy and the overall cost of production are important considerations. While advanced alloys may offer superior properties, they may also be more expensive.
- Cost-Effective Solutions: Gray cast iron and standard aluminum alloys provide a balance of good properties at a lower cost.
- High-Performance Requirements: For applications demanding superior performance, the investment in advanced alloys like alloyed steels and high-strength aluminum alloys is justified.
List: Key Considerations for Alloy Selection
- Operating environment (temperature, corrosive elements, mechanical stresses)
- Required mechanical properties (tensile strength, ductility, wear resistance)
- Cost considerations (material cost, production cost)
Conclusion
Innovative alloy selection is essential for optimizing the performance and durability of sand casting parts. By understanding the properties and benefits of various alloys, manufacturers can choose the most suitable materials for their specific applications. Advances in alloy technology continue to enhance the capabilities of sand casting, enabling the production of high-quality, durable parts for a wide range of industries. As the demand for high-performance components grows, the importance of selecting the right alloy for sand casting parts cannot be overstated.